Pressure, Re-establishing proper booster / horn interfaces – Sonics 1596 Actuator User Manual
Page 20
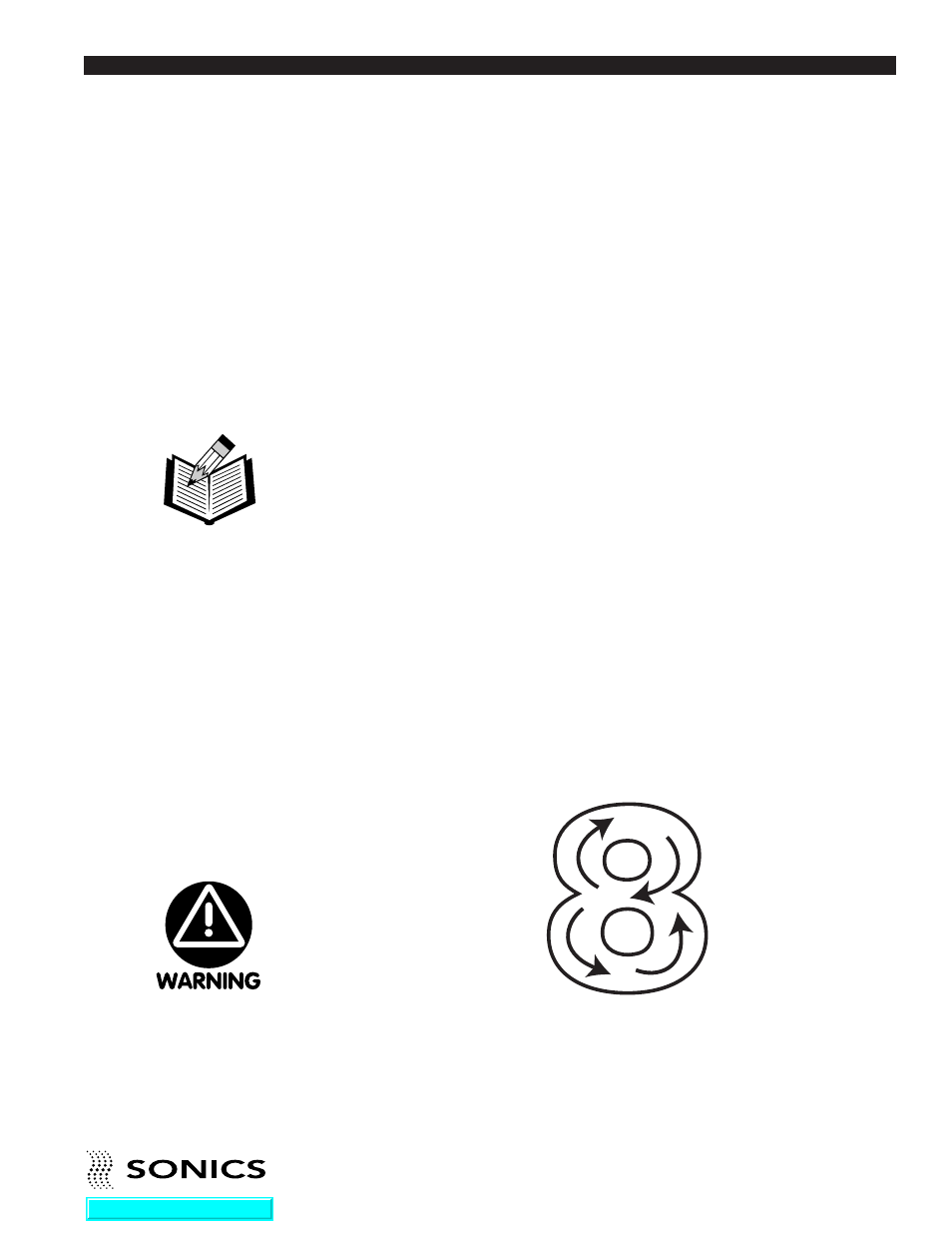
• • • • • • • • • • • • • • • • • • • • • • • • • • • • • • • • • • • • • • • • • • • • • • • • • • • • • • • • • • • • • • • • • • • • • • • • • • • • • • • • • • • • • • • • • • • • • • • • • • • • • • • • • • • •
I N S T R U C T I O N M A N U A L • M O D E L 1 5 9 5 / 1 5 9 6
19
PRESSURE
During the welding process, sufficient pressure should be applied to the part
so that the mating surfaces contact each other. If the pressure is too low, the
process will run inefficiently causing unnecessarily long weld time cycles,
marking of the parts or poor welding. If the pressure is too high, the horn may
stop vibrating, the part(s) might fracture, or the power supply might overload.
Refer to the Applications manual for additional information on pressure
settings. In general, a starting setting of between 25-30 psig (172 kPa/1.7 -
207 kPa/2 bar) can be used as a guideline, but you will need to adjust the air
pressure to a desired setting based upon the application results.
RE-ESTABLISHING PROPER BOOSTER / HORN
INTERFACES
To re-establish proper interfaces, follow these instructions:
1. Using open-ended wrenches, separate the booster from the horn. Clean
each item and then examine interfaces for irregularities (scoring).
2. If irregularities are present, remove the stud.
3. Tape a sheet of 400 grit emery cloth to a smooth, flat surface. (Do not use
coarser than 400 grit.)
4. Grasp the lower portion of the booster or horn and move it across the
emery cloth. To ensure proper lapping, a) hold the part straight, b) apply
light downward pressure, and c) move in one direction only in a figure 8
pattern.
Repeat the figure 8 pattern once more.
NOTE: Contact
between the booster
and horn should be
parallel. When
encountering symptoms
such as loud noises or
tuning difficulties,
examine the booster /
horn interfaces for
parallelism, corrosion,
galling or foreign
deposits. Also check
the tightness of the
stud.
DO NOT use anything
coarser than 400 grit
emery cloth.
Go To Top Of Document