SilentKnight SK-Duct Addressable Photoelectric Duct Detector User Manual
Page 4
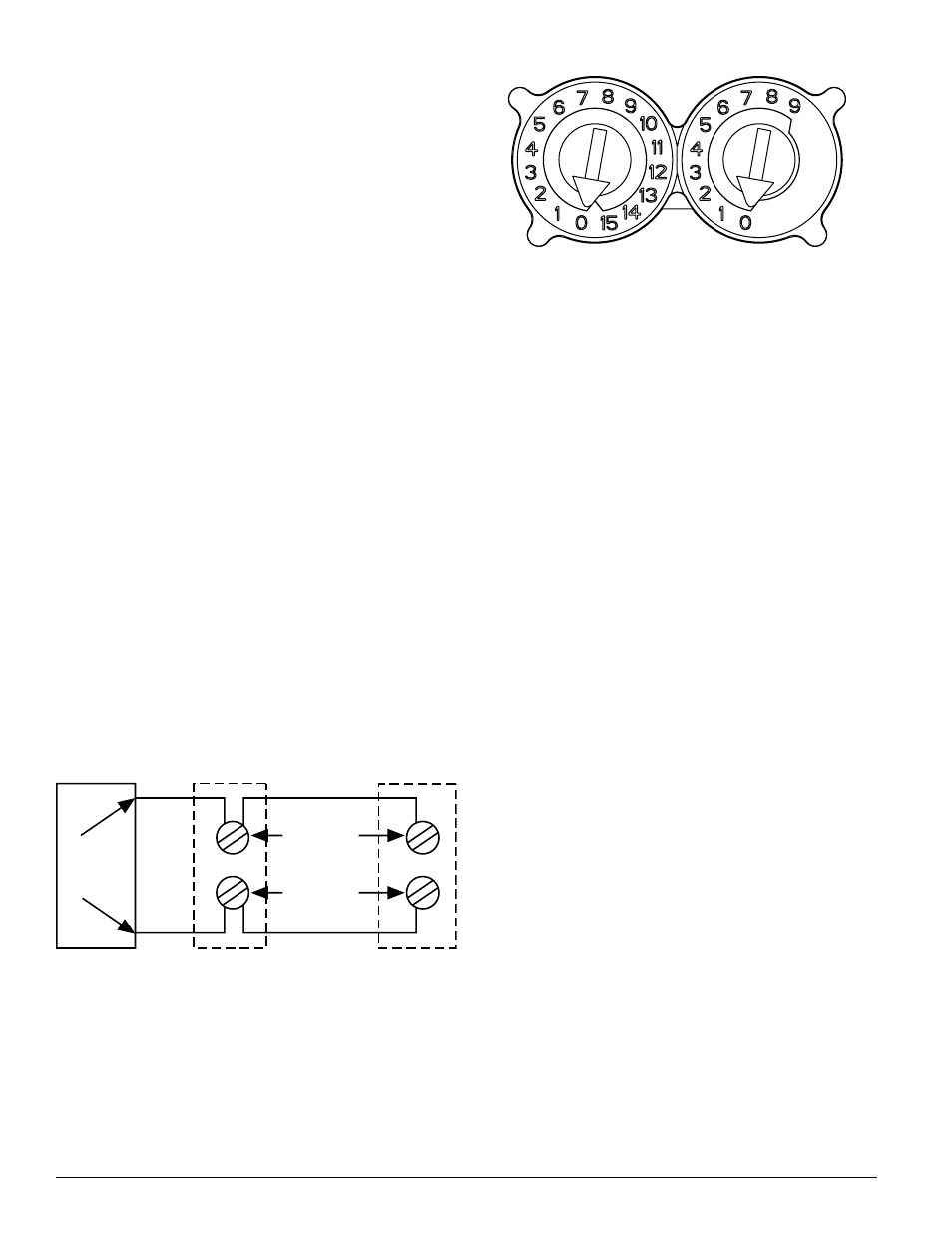
of water and no more than 1 .11 inches of water . Because most commercially
available manometers cannot accurately measure very low pressure differen-
tials, applications with less than 500 FPM of duct air speed may require one
of the following: 1) the use of a current-sourcing pressure transmitter (Dwyer
Series 607) or 2) the use of aerosol smoke, see below for test descriptions .
[6.2]LOw fLOw AIR fLOw TEST USINg DwyER SERIES 607
DIffERENTIAL PRESSURE TRANSMITTER
Verify the air speed of the duct using an anemometer . Air speed must be at
least 100 FPM . Wire the Dwyer transmitter as shown in Figure 5 . Connect the
leads of the meter to either side of the 1000Ω resistor . Allow unit to warm up
for 15 seconds . With both HIGH and LOW pressure ports open to ambient air,
measure and record the voltage drop across the 1000Ω resistor (measurement
1), 4 .00 volts is typical . Using flexible tubing and rubber stoppers, connect the
HIGH side of the transmitter to the sampling tube of the duct smoke detec-
tor housing, and the LOW side of the transmitter to the exhaust tube of the
duct smoke detector housing . Measure and record the voltage drop across the
1000Ω resistor (measurement 2) . Subtract the voltage recorded in measure-
ment 1 from the voltage recorded in measurement 2 . If the difference is greater
than 0 .15 volts, there is enough air flow through the duct smoke detector for
proper operation .
[7]fIELD wIRINg; INSTALLATION gUIDELINES
All wiring must be installed in compliance with the National Electrical Code
and the local codes having jurisdiction . Proper wire gauges should be used .
The conductors used to connect smoke detectors to control panels and acces-
sory devices should be color-coded to prevent wiring mistakes . Improper con-
nections can prevent a system from responding properly in the event of a fire .
For signal wiring (the wiring between detectors or from detector to auxiliary
devices), it is usually recommended that single conductor wire be no smaller
than 18 gauge . The duct smoke detector terminals accommodate wire sizes up
to 12 gauge . Flexible conduit is recommended for the last foot of conduit; solid
conduit connections may be used if desired .
Duct smoke detectors and alarm system control panels have specifications for
Signaling Line Circuit (SLC) wiring . Consult the control panel manufacturer’s
specifications for wiring requirements before wiring the detector loop .
[7.1]wIRINg INSTRUCTIONS
Disconnect power from the communication line before installing the SK-Duct
duct smoke detector .
The SK-Duct detectors are designed for easy wiring . The housing provides a
terminal strip with clamping plates . Wiring connections are made by sliding
the bare end under the plate, and tightening the clamping plate screw . See
Figure 6 on below for system wiring .
[7.2] SET ThE ADDRESS
Set the desired address on the sensor head code wheel switches on the back
of the sensor head .
fIgURE 7. ROTARy ADDRESS SwITChES
[8] VERIfICATION Of OPERATION
[8.1]INSTALL ThE COVER
Install the covers making sure that the cover fits into the base groove . Tighten
the seven screws that are captured in the covers . Note that the cover must be
properly installed for proper operation of the sensor .
NOTE: Verify sensor cover gasket is properly seated on cover prior to cover
installation .
[8.2] POwER ThE UNIT
Activate the communication line on terminals COM + and COM – .
[8.3] DETECTOR ChECK
Standby – If programmed by the system control panel, look for the presence of
the flashing LEDs through the transparent housing cover . The LED will flash
with each communication .
Trouble – If programmed by the system control panel and the detector LEDs
do not flash, then the detector lacks power (check wiring, missing or improp-
erly placed cover, panel programming, or power supply), the sensor head is
missing (replace), or the unit is defective (return for repair) .
[8.4]DUCT SMOKE DETECTOR TEST & MAINTENANCE PROCEDURES
Test and maintain duct smoke detectors as recommended in NFPA 72 . The
tests contained in this manual were devised to assist maintenance personnel
in verification of proper detector operation .
Before conducting these tests, notify the proper authorities that the smoke
detection system will be temporarily out of service . Disable the zone or system
under test to prevent unwanted alarms .
[8.4.1]TEST ThE UNIT
1 . M02-04-00 Magnet Test – This sensor can be functionally tested with a
test magnet . The test magnet electronically simulates smoke in the sens-
ing chamber, testing the sensor electronics and connections to the control
panel .
2 . Remote Test Accessory – The use of a remote accessory for visible indica-
tion of power and alarm is recommended .
Verify system control panel alarm status and control panel execution of all
intended auxiliary functions (i .e . fan shutdown, damper control, etc .) .
Two LEDs on the sensor are controlled by the panel to indicate sensor
status . Coded signals, transmitted from the panel, can cause the LEDs
to blink, latch on, or latch off . Refer to the control panel technical docu-
mentation for sensor LED operation and expected delay to alarm .
[8.4.2] ThE DETECTOR MUST BE RESET By ThE SySTEM CONTROL PANEL
[8.4.3]SMOKE ENTRy TEST USINg AEROSOL SMOKE
This test is intended for low-flow systems (100-500 FPM) . If the air speed is
greater than 500 FPM, use a conventional manometer to measure differential
pressure between the sampling tubes, as described under Measurement Tests
on Page 3 .
Drill a
1
⁄
4
-inch hole 3 feet upstream from the duct smoke detector . With the air
handler on, measure the air velocity with an anemometer . Air speed must be
at least 100 FPM . Spray aerosol smoke* into the duct through the
1
⁄
4
-inch hole
for five seconds . Wait two minutes for the duct smoke detector to alarm . If the
duct smoke detector alarms, air is flowing through the detector . Remove the
duct smoke detector cover and blow out the residual aerosol smoke from the
chamber and reset the duct smoke detector at the panel . Use duct tape to seal
the aerosol smoke entry hole . Remember to replace the cover after the test or
the detector will not function properly .
SK-300-000
4
I56-3432-001R
fIgURE 6. SySTEM wIRINg DIAgRAM fOR SK-DUCT:
HO572-00
COMM.
LINE (+)
UL/FM LISTED
CONTROL
PANEL
1ST
DETECTOR
IN LOOP
2ND
DETECTOR
IN LOOP
COMM.
LINE (–)
COMM.
LINE
HO112-01