LAARS Pennant PNCV (Sizes 200, 300, 400) - Install and Operating Manual User Manual
Page 26
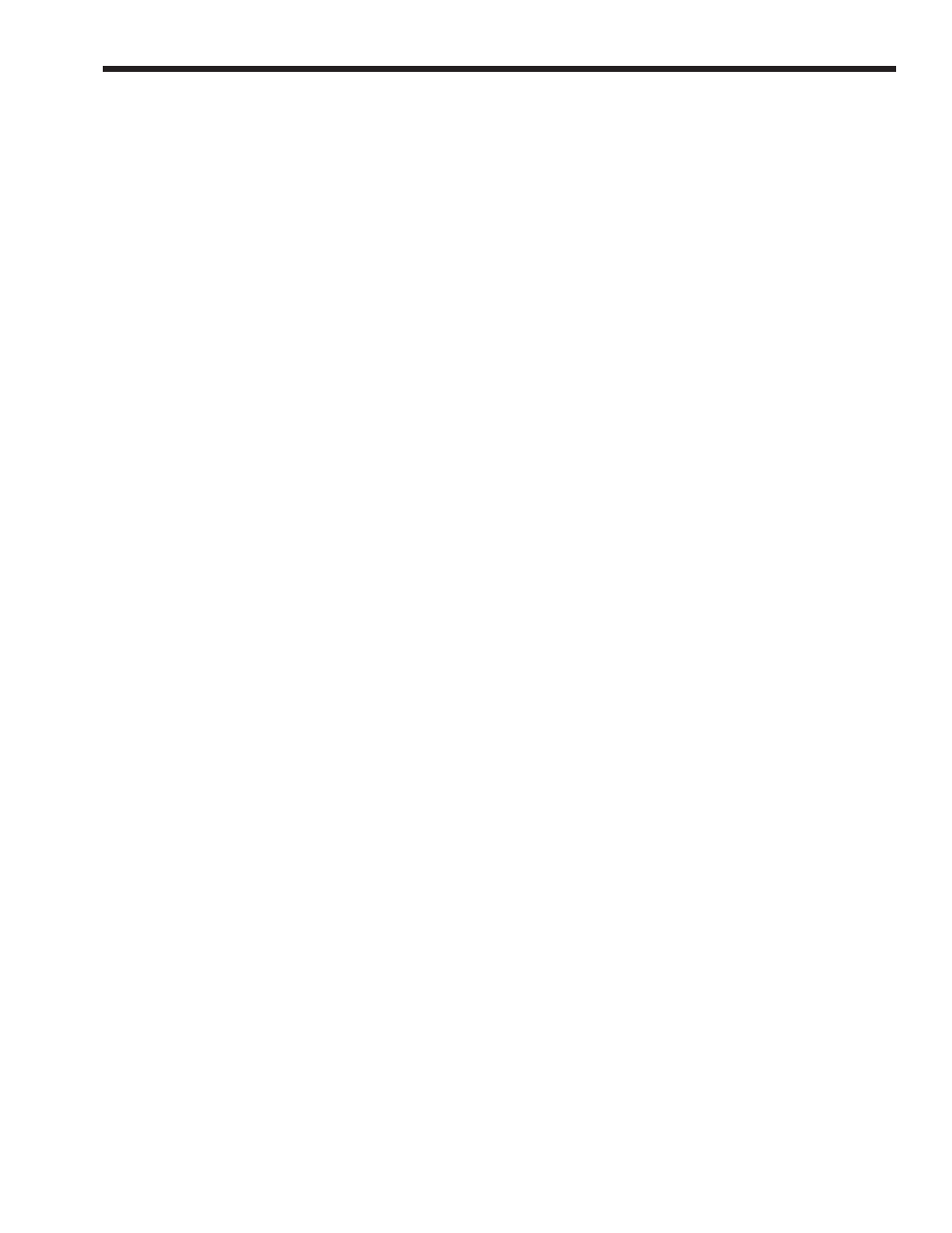
LAARS Heating Systems
Page 24
Pennant 200, 300, 400
Page 25
Single pole switches, including those of safety
controls and protective devices must not be wired in a
grounded line.
All electrical connections are made in the field
wiring terminal strip, which is located to the left of the
blower.
NOTE: All internal electrical components have been
pre-wired. No attempt should be made to connect
electrical wires to any other location except the
wiring box.
5.1 Main Power
Connect a 15 amp. fused, 120-volt supply to the
main power switch (hot leg is connected directly to
switch). Neutral leg is connected directly to the white
wire. Ground wire can be connected to the grounding
screw in the box or on the switch.
Wiring diagrams are shown in Figures 13 and 14.
5.2 Field Wiring
Terminal strips are supplied for field wiring
connections under the flip-up control panel.
Connections must be made as specified by the
Connection Diagram (Figure 13). The following may
be connected to the terminal strips as field wiring:
Temperature Sensor
: The sensor supplied loose
with the Pennant is installed in the piping or tank, per
the suggested piping diagrams. The sensor, Thermistor
2, is connected to the “9” and “10” terminals.
Field Installed Pump
: A pump contactor can be
wired to the “P1” and “P2” terminals. These terminals
are attached to dry contacts of an adjustable delay
on break relay. The contacts may be used to switch a
larger pump contactor or can be used to directly switch
the hot leg of a circulator pump, up to 1hp at 120 VAC
or 3/4hp at 240 VAC.
Note that in some cases, the pump is run
continuously.
External Alarm
: An external power supply and
alarm can be connected to the “1” and “2” terminals.
In the event of an ignition time out, a contact closure
occurs across these terminals.
BAS Connections
: To use an external control
to call Pennant units for heat, connect to terminals
"3" and "4". Then put the Local/Remote Switch in the
"Remote" mode.
Other Field Interlocks
: To install other field-
wired switches (proving switches, flow switches, etc.),
remove the jumper between the terminals labeled “7”
and “8”.
Auxiliary Contacts
: The contacts between
terminals “11” and “12” will close whenever Loop 2
is enabled and there is a call for heat on Loop 2. Use
these terminals to enable field devices under these
circumstances
SECTION 6.
Operating Instructions
6.1 Filling the Boiler System
1. Ensure the system is fully connected. Close all
bleeding devices and open make-up water valve.
Allow system to fill slowly.
2. If make-up water pump is employed, adjust
pressure switch on pumping system to provide
a minimum of 12 psi (81.8 kPa) at the highest
point in the heating loop.
3. If a water pressure regulator is provided on the
make-up water line, adjust the pressure regulator
to provide at least 12 psi (81.8 kPa) at the highest
point in the heating loop.
4. Open bleeding devices on all radiation units
at the high points in the piping throughout
the system, unless automatic air bleeders are
provided at such points.
5. Run system circulating pump for a minimum of
30 minutes with the boiler shut off.
6. Open all strainers in the circulating system,
check flow switch operation, and check for
debris. If debris is present, clean out to ensure
proper circulation.
7. Recheck all air bleeders as described in Step 4.
8. Check liquid level in expansion tank. With the
system full of water and under normal operating
pressure, the level of water in the expansion tank
should not exceed 1⁄4 of the total, with the balance
filled with air.
9. Start up boiler according to the procedure in this
manual. Operate the entire system, including the
pump, boiler, and radiation units for one (1) hour.
10. Recheck the water level in the expansion tank. If
the water level exceeds 1⁄4 of the volume of the
expansion tank, open the tank drain, and drain to
that level.
11. Shut down the entire system and vent all
radiation units and high points in the system
piping, as described in Step 4.
12. Close make-up water valve and check strainer in
pressure reducing valve for sediment or debris
from the make-up water line. Reopen make-up
water valve.
13. Check gauge for correct water pressure and also
check water level in the system. If the height
indicated above the boiler insures that water is at
the highest point in the circulating loop, then the
system is ready for operation.
14. Refer to local codes and the make-up water
valve manufacturer’s instructions as to whether
the make-up water valve should be left open or
closed.