LAARS Pennant PNCV (Sizes 200, 300, 400) - Install and Operating Manual User Manual
Page 16
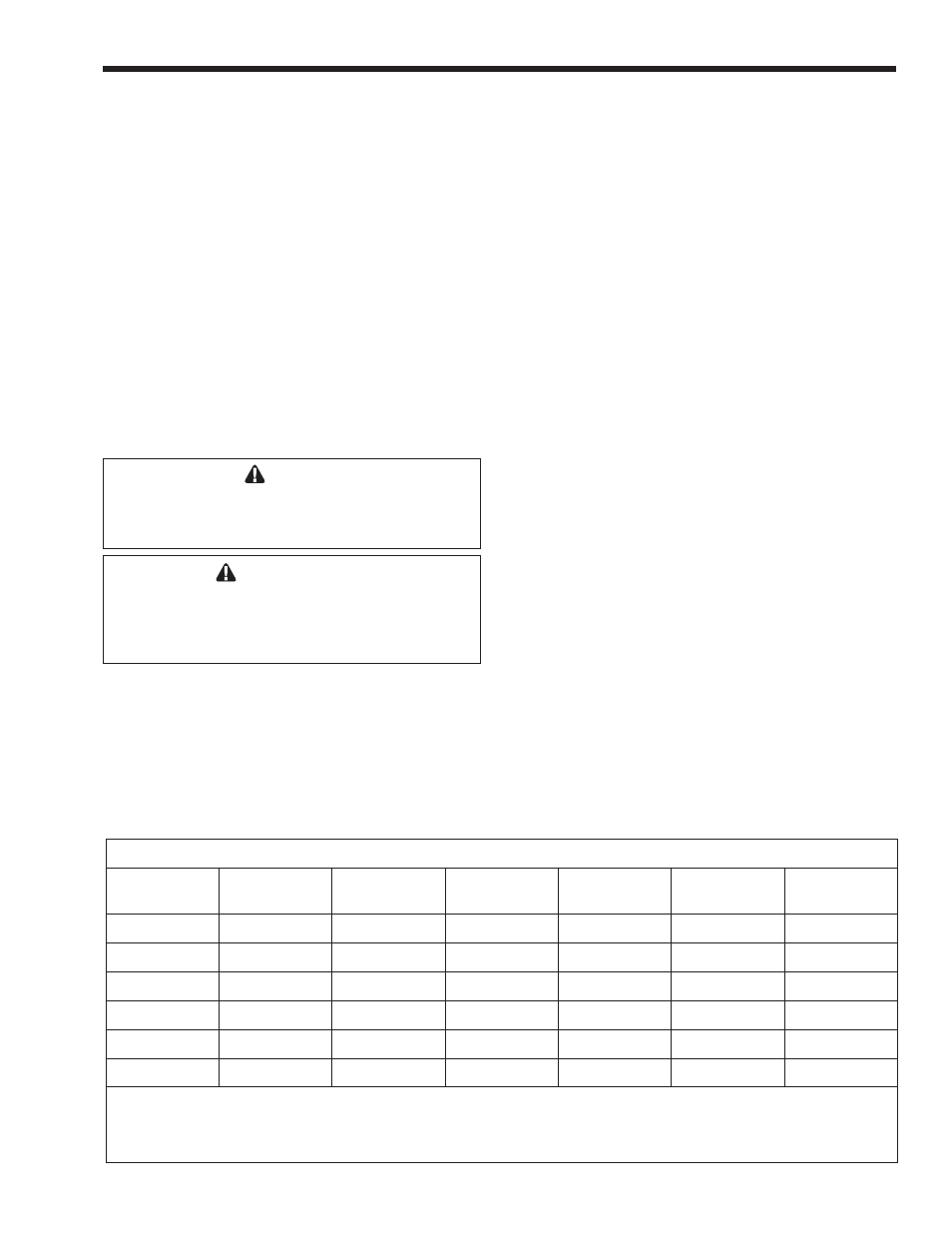
LAARS Heating Systems
Page 14
Pennant 200, 300, 400
Page 15
5. Locate and install manual shutoff valves in
accordance with state and local requirements.
6. A sediment trap must be provided upstream of
the gas controls.
7. All threaded joints should be coated with
piping compound resistant to action of liquefied
petroleum gas.
8. The appliance and its individual shutoff valve
must be disconnected from the gas supply piping
during any pressure testing of that system at test
pressures in excess of 0.5 psig (3.45 kpa).
9. The unit must be isolated from the gas supply
system by closing its individual manual shutoff
valve during any pressure testing of the gas
supply piping system at test pressures equal to or
less than 0.5 psig (3.45 kpa).
10. The appliance and its gas connection must be
leak tested before placing it in operation.
11. Purge all air from gas lines.
WARNING
Do not use open flame to check for leaks. An open
flame could lead to explosion, which could result in
property damage, serious injury or death.
AVERTISSEMENT
Ne recherchez pas les fuites avec une flamme nue.
Une flamme nue peut provoquer une explosion qui
peut causer des dommages matériels, de sérieuses
blessures corporelles ou la mort.
NOTE: The Pennant appliance and all other gas
appliances sharing the gas supply line must be
firing at maximum capacity to properly measure
the inlet supply pressure. The pressure can be
measured at the supply pressure port on the gas
valve. Low gas pressure could be an indication of
an undersized gas meter, undersized gas supply
lines and/or an obstructed gas supply line.
SECTION 4A.
Water Connections —
Pennant Boiler
4A.1 Heating System Piping:
Hot Supply Connections — Boiler
NOTE: This appliance must be installed in a closed
pressure system with a minimum of 12 psig (82.7
kPa) static pressure at the boiler.
Hot water piping should be supported by suitable
hangers or floor stands. Do not support piping with
this appliance. Due to expansion and contraction of
copper pipe, consideration should be given to the type
of hangers used. Rigid hangers may transmit noise
through the system resulting from the piping sliding in
the hangers. It is recommended that padding be used
when rigid hangers are installed. Maintain 1" clearance
to combustibles for hot water pipes.
Pipe the discharge of the relief valve (full size)
to a drain or in a manner to prevent injury in the event
of pressure relief. Install an air purger, an air vent,
a diaphragm-type expansion tank, and a hydronic
flow check in the system supply loop. Minimum fill
pressure must be 12 psig (82.7 kPa). Install shutoff
valves where required by code.
Suggested piping diagrams are shown in Figures
4, 5, 6, 7 and 8. These diagrams are meant only as a
guide. Components required by local codes must be
properly installed.
Note the recommended location of the
temperature sensor on the diagrams; you must provide
a location for the additional sensor shipped with the
Pennant. This sensor may be strapped onto pipe from
1" to 4" diameter, or inserted into an immersion well.
Distance from Gas Meter or Last Stage Regulator
Model and
Gas Type
0-100'
0-31 m
100-200'
31-61m
200-300'
61-91m
200 natural
11⁄4"
3.2 cm
11⁄4"
3.2 cm
11⁄4"
3.2 cm
200 propane
1"
2.5 cm
1"
2.5 cm
11⁄4"
3.2 cm
300 natural
11⁄4"
3.2 cm
11⁄2"
4.0 cm
11⁄2"
4.0 cm
300 propane
1
2.5 cm
11⁄4"
3.2 cm
11⁄4"
3.2 cm
400 natural
11⁄4"
3.2 cm
11⁄2"
4.0 cm
2"
5.0 cm
400 propane
11⁄4"
3.2 cm
11⁄4"
3.2 cm
11⁄2"
4.0 cm
Notes:
1. These figures are based on 1/2" (0.12 kPa) water column pressure drop.
2. Check supply pressure and local code requirements before proceeding with work.
3. Pipe fittings must be considered when determining gas pipe sizing
.
Table 7. Gas Piping Size.