5 high gas consumption – LAARS EDN Series - Installation, Operation and Maintenance Instructions User Manual
Page 34
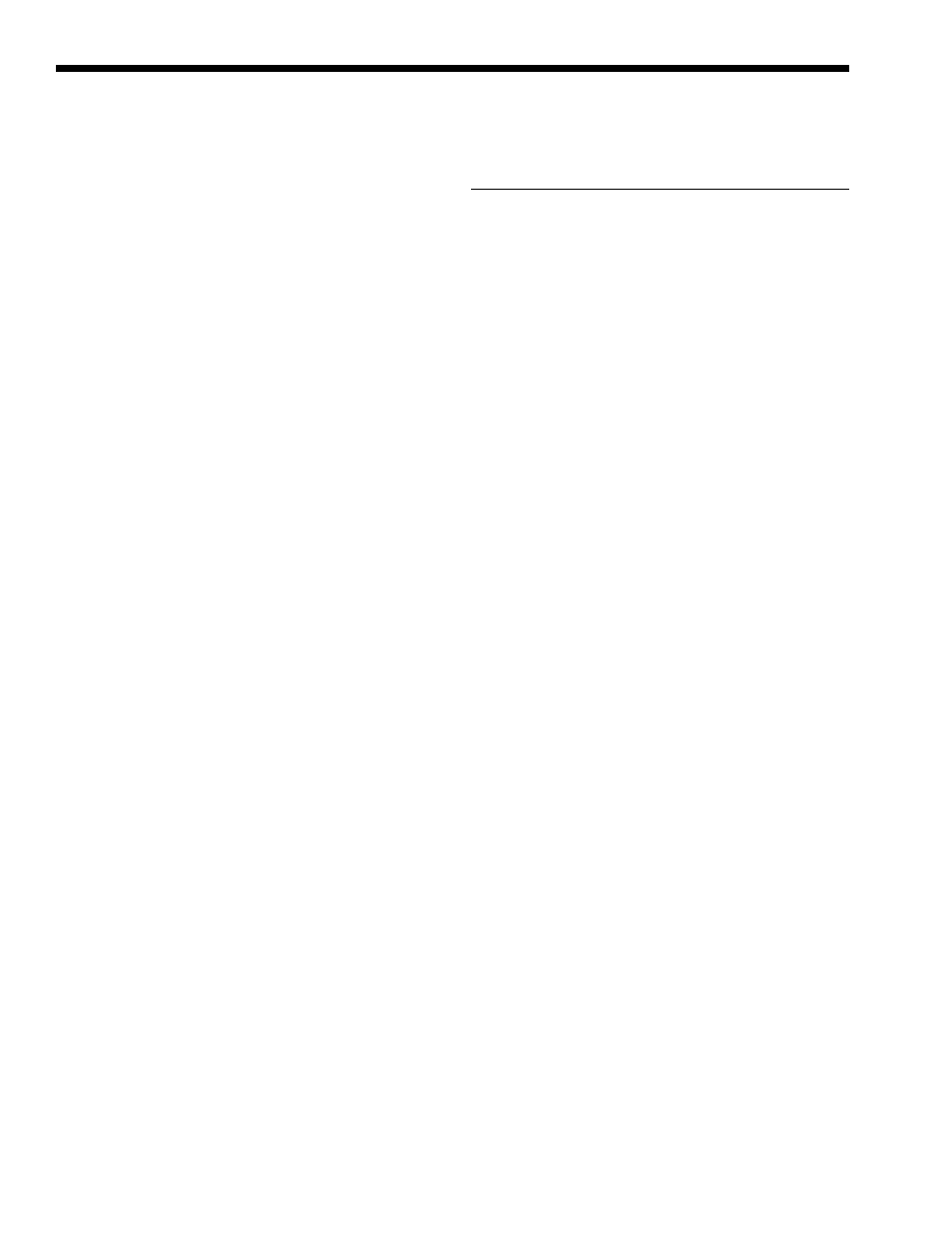
Page 34
LAARS HEATING SYSTEMS
SECTION 11.
Parts Identification
Description
Part Number
1. PAN, COMBUSTION CHAMBER T0P
2400-502
2. PAN, COMBUSTION CHAMBER BOTTOM
2400-504
3. INSULATION, COIL COVER
2400-506
4. INSULATION, BOILER COIL
2400-508
5. COIL, BOILER, EBP/EDP/EDN 110 (ASSY.)
2400-510
6. COIL, BOILER, EBP/EDP/EDN 175 (ASSY.)
2400-512
7. GASKET, BURNER
2400-514
8. BURNER, EBP/EDP/EDN 110
(GASKETS INCLUDED)
2400-516
9. BURNER, EBP/EDP/EDN 175
(GASKETS INCLUDED)
2400-518
10. TRANSFER TANK
2400-520
11. BOILER DRAIN (BEHIND PANEL-EBP)
2400-522
12. BLOWER, COMBUSTION AIR
(GASKETS INCLUDED)
2400-524
13. IGNITOR/FLAME SENSOR
(GASKET INCLUDED)
2400-526
14. GASKET, IGNITOR/FLAME SENSOR
2400-528
15. COIN VENT
1-592
16. COMBUSTION AIR INLET,
ADJUSTABLE, KIT
2400-142
17. VALVE, ANTI CONDENSING,
REPAIR KIT
2400-538
18. GASKET, BLOWER
2400-540
19. WATER FLOW SWITCH
2400-542
20. BOILER CONTROL (BEHIND PANEL) (EBP)
2400-546
21. GAS VALVE, HONEYWELL,
NEG. REG. PRESSURE
2400-548
22. SAFETY LIMIT, 230 °F
2400-550
23. SENSOR, TANK ( EBP ONLY )
2400-552
24. SENSOR, BOILER FLOW
2400-554
25. SENSOR, BOILER RETURN
2400-556
26. THERMOSTATIC UNION EDP (NOT SHOWN)2400-030
27. GAS SHUTOFF VALVE
2400-560
28. PUMP, EBP/EDP 110
2400-592
29. PUMP, EBP/EDP 175
2400-386
30. GASKETS, PUMP FLANGE
2400-566
31. RESET SWITCH
2400-568
32. HEAT EXCHANGER, DOM. HOT WATER
2400-570
33. GASKETS, DHW HEAT EXCHANGER
2400-572
34. BUTTON, ON/OFF (PART OF 2400-546)
-
35. BUTTON, TEMP/MESSAGE
(PART OF 2400-546)
-
36. GAUGE, PRESSURE (NOT SHOWN)
2400-574
37. PRESSURE RELIEF VALVE
(30 PSIG, NOT SHOWN)
2400-112
38. BOILER CONTROL (BEHIND PANEL)
(EDP/EDN)
2400-558
39. PUMP, EDN 110
2400-388
40. PUMP, EDN 175
2400-388
41. THERMOSTATIC UNION EDN (NOT SHOWN)47-026
42. TRANSFORMER (NOT SHOWN)
2400-562
Failure of the mixing valve will allow cold water
to be mixed with the hot water from the DHW heat
exchanger during a DHW draw regardless of the
setting of the mixing valve or the temperature of the
water leaving the DHW heat exchanger. The failure
can be detected by observing the temperature of the
three pipes connected to the mixing valve. If the “mix”
temperature is luke warm or cool and the “hot”
temperature is hot and the “cold” temperature is cold
then the mixing valve is either faulty or incorrectly
adjusted and must be replaced or adjusted.
DHW heat exchanger scaling may occur in some
areas of the country where there are high
concentrations of minerals in the water. These
minerals may cause fouling of the DHW heat
exchanger over an extended period of time (lime build
up). Other minerals, which react more quickly in well
systems (mostly magnesium), cause slime on the
inside of the heat exchanger and prevent adequate heat
transfer. These minerals must be filtered out by a
special incoming water filter or by the addition of an
inhibitor to protect the coil and provide acceptable
water quality. Minerals may be removed when
necessary by flushing the coil with a cleaner such as
“Unlime®” or “Sizzle®”.
10.5 High Gas Consumption
Boilers operating with an improper air/fuel ratio
are very inefficient and consequently, have very high
gas consumption. Because efficiency is high when the
CO
2
is high, boilers operating with low CO
2
(especially LP boilers) consume more gas. Adjust the
CO
2
or O
2
for optimum efficiency. If no combustion
analyzing equipment (CO
2
or O
2
) is available then a
proper adjustment of the air/fuel ratio (CO
2
) can not
be accomplished. However, by briefly sniffing the flue
gases it is possible to determine if the CO
2
or O
2
is
within the proper range. There is no significant flue
gas odor when combustion is proper. A strong
piercing smell indicates poor combustion and
generally a lean mixture (low CO
2
). Check gas valve
calibration (offset adjustment) and adjust if indicated.
Do not attempt to correct combustion by reorificing
without an O
2
or CO
2
kit.