LAARS EBP 175 MBTU/h - Installation, Operation and Maintenance Instructions User Manual
Page 35
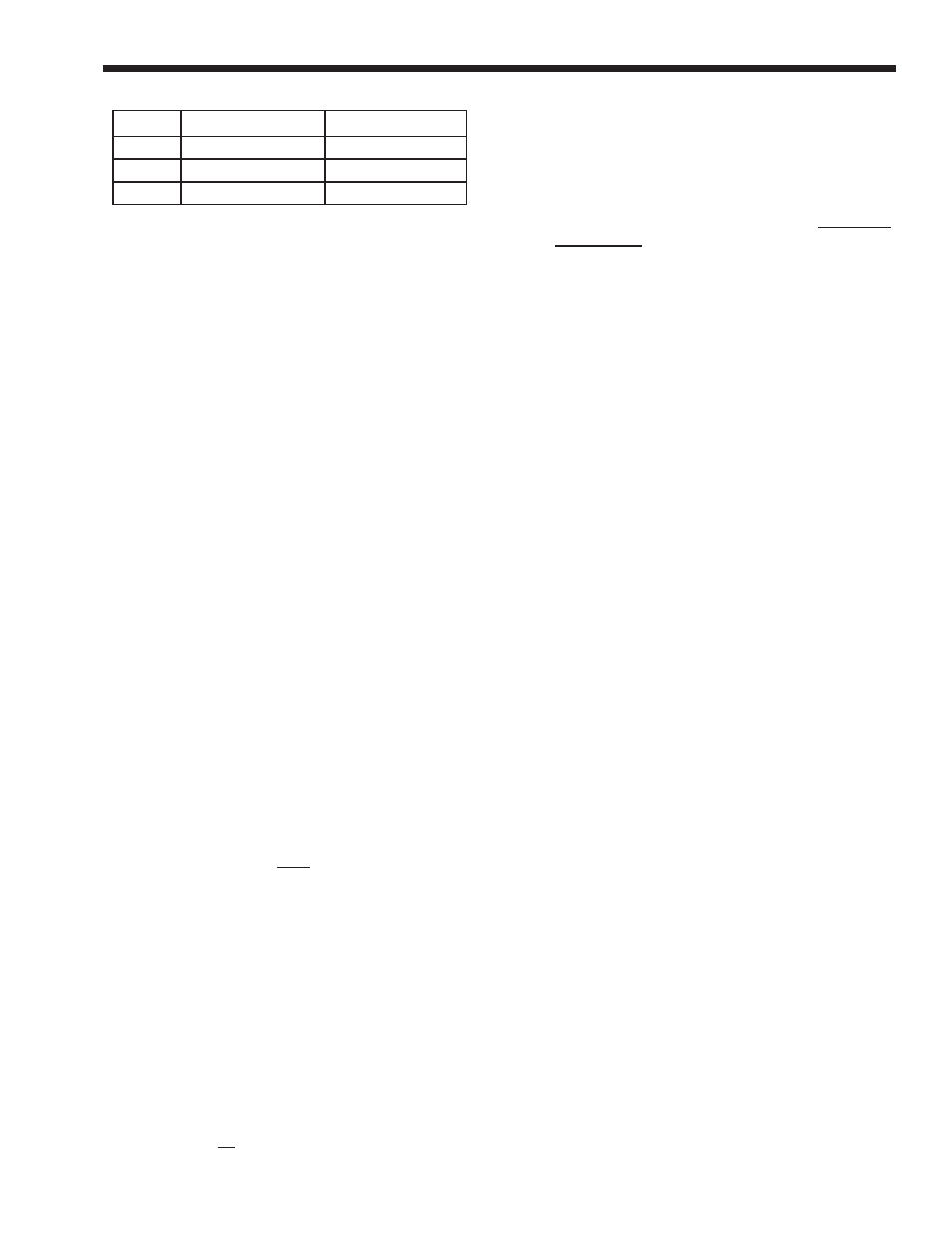
Endurance
Page 35
Natural Gas
LP Gas
CO2
9.0 to 9.6%
9.7 to 10.1%
O2
4.5 to 5.0%
4.5 to 5.0%
Offset
-0.01 to -0.10 in. w.c.
-0.01 to -0.10 in. w.c.
Table 5. Combustion Parameters.
SECTION 11.
Symptom Evaluations
11.1 Delayed ignition
Possible Causes
a. High lockup pressure (LP boilers) - occurs on
start-up.
b. Gas valve regulation problem - occurs on start-up.
c. Incorrect gas orifice (Natural gas orifice in an LP
boiler) - occurs on start up
d. Defective burner - occurs on startup or at burner
shutdown.
High lock up pressure is the most common cause
of delayed ignitions on LP fueled boilers. It may result
from an improper second stage regulator selection or
from a faulty regulator.
Lock up can be detected by measuring the gas
supply pressure to the boiler at the inlet pressure tap
on the gas valve. The gas supply to the boiler must be
shut off before making this connection. Use a water
manometer or pressure gauge with a scale reading of
at least 25 in. w.c. or 15 oz/in
2
. Loosen the screw in
the gas valve pressure port one full turn and install a
hose from the pressure gauge over the pressure port.
Turn on the gas supply. The ENDURANCE boiler is
designed to operate with supply pressures of 4-13 in.
w.c. (2.3 - 7.5 oz/ in²). If the supply pressure exceeds
13 in. w. c. (7.5 oz/ in²) with the boiler not operating
it is possible that this may be the cause of delayed
ignitions and the pressure must be reset to ~ 9 in. w.c.
(5.2 oz/ in²). Restart the boiler and then switch it off
again. Lock up pressures must be measured when the
boiler is not operating and preferably immediately
after boiler shutdown. If the gas pressure again
exceeds the allowable values, correct the lock up
problem.
Gas valve regulation problems can also cause
delayed ignitions. See “Gas valve calibration”.
Incorrect gas orifice – Check orifice size.
A defective burner can cause a delayed ignition
during operation or at shutdown. If the gas supply
pressure is proper the gas valve is functioning properly
and the gas orifice is correct, the burner should be
inspected. To inspect it, remove the blower. The burner
is retained by the blower and it will drop out of the
bottom of the chamber when the blower is removed.
There should be no distortion or perforations in
the burner other than the punched holes. Replace if
indicated.
11.2 Short Cycling
Possible causes
a. Anti-condensing valve not opening.
b. T-T wires cross connected (jumped) – improper
installation
c. Leakage of flue products into the combustion
air stream – Direct Vent Installations only, see
Section 9.2.3
, Resolving Lockouts.
11.3 Noisy Operation
There are two principal sources of noisy
operation:
a. Combustion - high pitched noise - whistle or
hoot.
b. Boiling (kettling) - lower frequency noise which
varies with temperature - moan.
Many times it is difficult to determine the source
of the noise or if it is combustion related or boiling
related. Combustion noises always have the same
frequency; however, their volume may change from
the time that the burner first fires to the time that
it shuts off. A boiling noise is identified by rapidly
raising or lowering the system water pressure while
the noise is present. A change in the pitch or intensity
of the noise indicates a boiling problem.
Combustion noise occurs at any boiler discharge
temperature and is heard the loudest at the flue outlet
(especially on units that are sidewall vented). There
are two basic causes for the noise, rich mixture (high
CO
2
or low O
2
) or cross contamination. The mixture
is determined by measuring the percent O
2
or CO
2
in
the flue products. O
2
readings lower than 4½% or CO
2
readings higher than 9¼% (natural gas) and 10.8%
(LP) will often cause combustion related noise. The
rich mixture could be caused by the mis-calibration of
the gas valve (offset adjustment) or by the gas orifice
size. To eliminate the noise; first, check the gas valve
calibration. If it is correct, install a smaller gas orifice
so that the O
2
will rise above 4½% or the CO
2
will
drop to 8½% (natural) or 9½% (LP).
The CO
2
& O
2
readings may be influenced by
cross contamination. Suspect cross contamination if
the noise returns when the front panel is replaced.
Boiling (kettling) may occur at boiler discharge
temperatures from 170°F to 210°F. The temperature
at which it starts will vary from one installation to
another. The primary cause of the problem is poor heat
transfer on the inside of the boiler coil. This may be
caused by foaming due to excessive concentration of
antifreeze in the system or by scaling from the boiler
water due to hardness of make up water.
Plumbing antifreezes should never be used in a
boiler system. Only boiler antifreezes, with effective