LAARS EBP 175 MBTU/h - Installation, Operation and Maintenance Instructions User Manual
Page 34
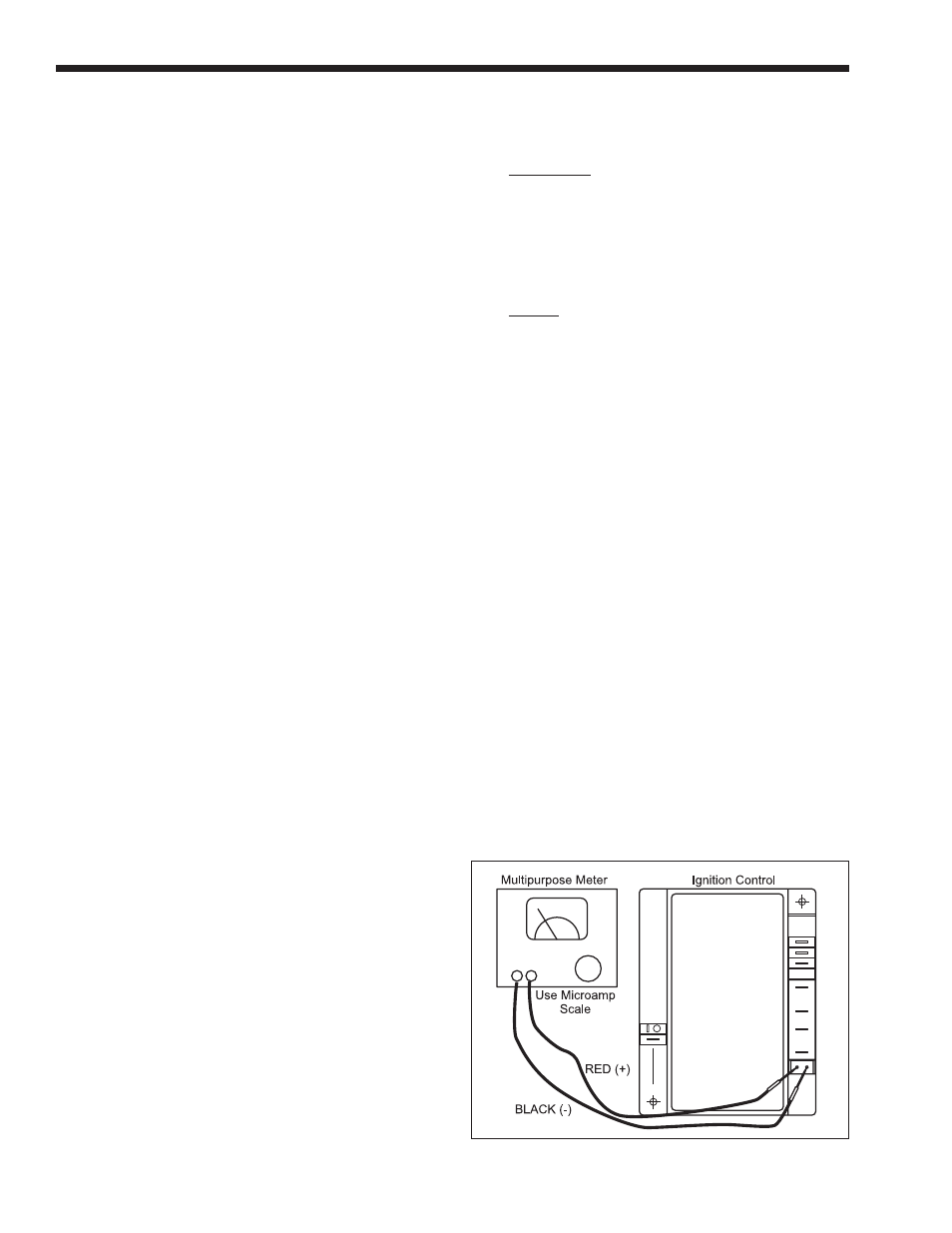
Page 34
LAARS Heating Systems
d. Ignitor failure: If the boiler goes through a
normal start cycle but combustion does not occur,
ignitor failure should be suspected.
Check the ignitor by unplugging the ignitor plug
and measuring the ignitor resistance. It should be
50-100 (
Ω
) ohms. If the resistance is not 50-100
ohms (
Ω
), replace the ignitor. If the resistance is
correct, reset the boiler and check for 120 VAC
at the ignitor plug during the start cycle. If there
is no voltage, replace the boiler control or faulty
ignitor wires.
e. Blocked or contaminated air source: Before
proceeding, ensure that the vent terminal (Direct
Vent installations) or the air inlet (Category IV
installations) is not obstructed. In general, only
direct vent installations have the potential for
cross contamination (flue products entering the
combustion air stream) of the combustion air
source. This may be caused by leaky joints in the
3" flue pipe located inside the 5" combustion air
pipe. If this is suspected, remove the front panel
from the appliance, reset the boiler and allow it
to go through a normal cycle. If during this cycle
there is no flue odor, repair the leaky joints in the
flue pipe.
f.
Safety limit trip: The safety limit on the
Endurance is interlocked with the boiler control.
If this limit detects outlet water temperature
greater than 230°F (110°C), or if there is a
component failure, the limit will open the
boiler circuit and the boiler control will
indicate LO on the display. The safety limit will
automatically reset when the water temperature
drops. If the temperature has exceeded 230°F
(110°C), determine the cause of the high water
temperature and correct. If the switch is tripped
when the water has not reached 230°F (110°C),
replace the switch.
SECTION 10.
Air Orifice and Gas
Valve Adjustment
If poor combustion is suspected because of a
strong exhaust smell, pulsation in the exhaust, or
nuisance flame failure lockouts (shown as “LO” on
LED), the air orifice may need to be adjusted.
Note: Direct vent installations may experience
poor combustion that results from cross contamination
of the combustion air source. Check for cross
contamination before attempting offset pressure
adjustment (see
Section 9.2.3 step 5
).
To adjust the air orifice, remove the door panel,
and remove the plug in the flue stack. Perform a CO
2
analysis while the boiler is running at the maximum
firing rate. (Pressing the enter button and the up arrow
on the boiler control, and holding them for 2 seconds,
places the Endurance in high fire for 5 minutes).
Natural Gas:
•
If CO
2
is greater than 9.6, open the holes on
the adjustable inlet. Adjust the cover until
CO
2
is within the range listed in
Table 5
.
•
If CO
2
is less than 9.0, close off the
adjustable inlet. Adjust the cover until CO
2
is within the range listed in
Table 5
.
LP Gas:
•
If CO
2
is greater than 10.1, open the holes
on the adjustable inlet. Adjust the cover
until CO
2
is within the range listed in
Table 5
.
•
If CO
2
is less than 9.7, close off the
adjustable inlet. Adjust the cover until CO
2
is within the range listed in
Table 5
.
Reinstall the flue stack plug when finished
testing.
If CO
2
is still out of range, adjust the gas valve
calibration (always adjust the air orifice first).
To adjust the gas valve calibration, see
Figure
35
for the location of the offset pressure port and the
offset adjustment. When adjusting the offset pressure,
the CO
2
will reduce as the offset pressure is adjusted
more negative. Adjust the offset pressure to achieve
the values shown in
Table 5
. Note that during the pre-
purge cycle, the gauge will indicate several inches w.c.
negative pressure.
Always check the CO
2
after making adjustment
to the gas valve.
IMPORTANT NOTE: FINAL ADJUSTMENT OF THE
OFFSET PRESSURE MUST ALWAYS RESULT IN A
NEGATIVE PRESSURE UPON COMPLETION.
Figure 37. Flame Sensor Current Check.