Supplying material to gun, Safety precautions – Graco 226-167 SERIES"A" User Manual
Page 6
Attention! The text in this document has been recognized automatically. To view the original document, you can use the "Original mode".
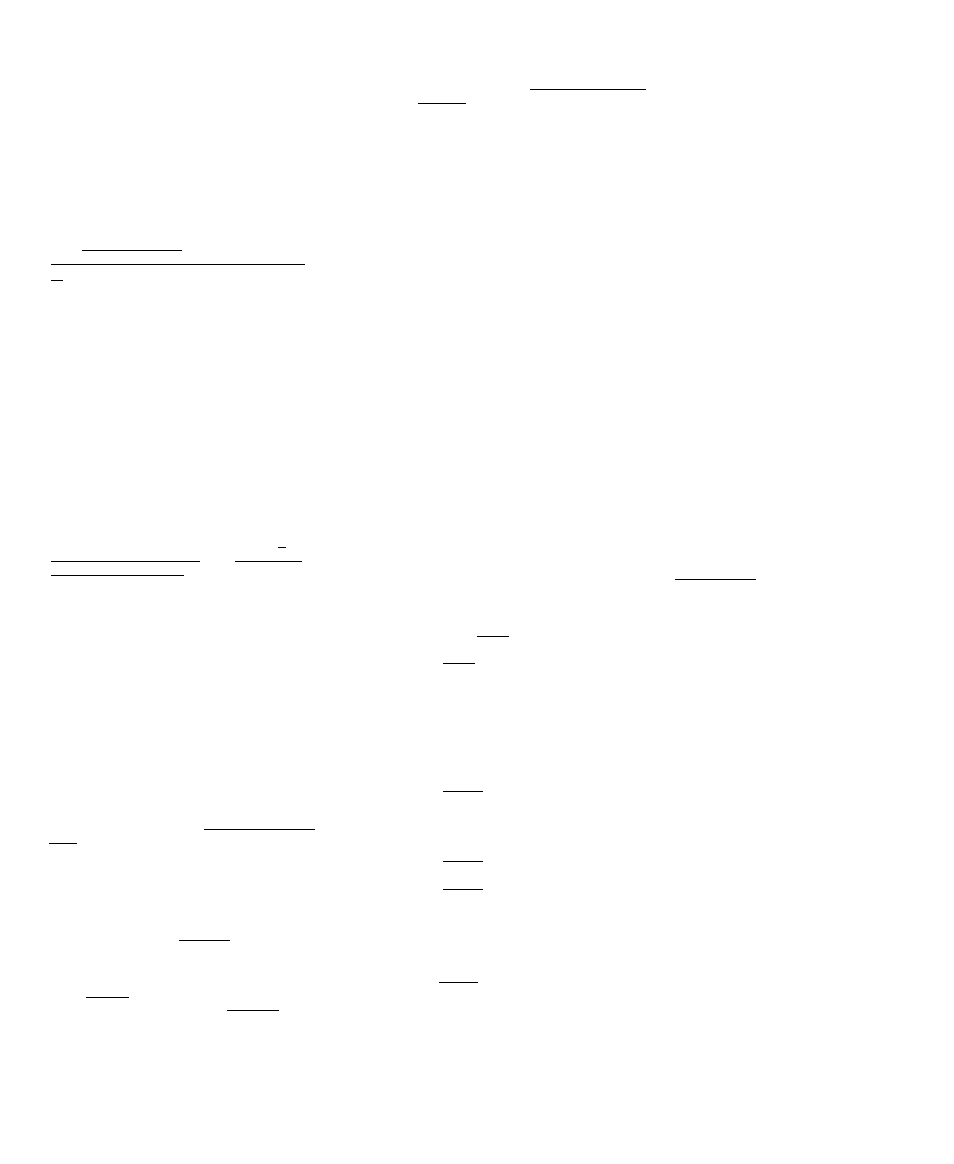
НОТЕ: If manufacturer of material does not re-
ommend a specific type of solvent, check the com-
atability of the solvent to-be used for thinning
he material by dropping a single drop of the materi-
1 into a small container of the solvent. If the
laterial drop clouds or disperses readily, the sol-
■ent is compatible. If drop tends to string or
orm a ball, the solvent is not compatible and
.efinitely should not be used.
•
AGITATION OF MATERIAL
Thorough agitation of material should be
lecomplished prior to Dumping material to spray
Agitation can best be obtained as follows ;
am
1.
Snap air line coiçler 202-437 onto agi-
:ator air fitting and agitator will be energised,
lefer to Fig. 1.
2.
Turn agitator air valve 205-528, two or
nore turns to the left to start agitator air
notor. Refer to Fig. 1. Speed of agitation
nay be adjusted to suit the particular viscosity
3f material used. NOTE:
Excessive agitation
speed may cause vibration and foaming of material,
dse moderate agitation speeds at all times.
3.
Open manifold dung) valve and start pump.
This permits pump circulate the material under
light load.
4" Lift hinged inspection plate and examine
progress of agitation through hole in cover. It
is extr^^maly impcirtant that all solids are put in
suspension and held there dbring the entire spray
operation.
5. Allow agitator to continuev operation .
hüe unit is supplying material to spray gun.
SUPPLYING MATERIAL TO GUN
1.
Stop puag) and close manifold dump valve
iter material has been circulated sufficiently
jid before attempting to spray. When closed,
ïiob of dump valve is in a horizontal position.
2.
Open material shutoff valves 205-583
accessory), if used. Handles are parallel to
■alve body when open. Refer to Fig. 2*
3.
Open ON-OFF pump air control petcock
102-338. With petcock open, manifold dump valve
losed and air regulator 205-360 set to control
ihe air pressure admitted, the pumping action of
lump is controlled by operation of spray gun.
iqueezing trigger of spray gun open automatically
(tarts pump operating, forcing material, under ^
iressure, from gun spray tip.
4* Adjust pump to minimum pressure required
;o obtain desired breakup and spray pattern of
aaterial. This setting will vary due to viscosity
daterial, orifice diameter and fan angle of spray
;ip. To increase air pressure to pump, turn ad
justing knob of regulator 205-360 clockwise and
pressure turn it counterclockwise.
JOTE: The amount of air pressure supplied to the
dump determines the pressure of the material
Torced through the orifice in spray tip. Pump
ievelops material pressure 28 times that of the
6
inbound air pressure. Do not set higher than
100 p.B.i.
5- While spraying be sure at all times to
hold spray gun perpendicular (approx. 90“) to '
surface to be sprayed, with its spray tip 12 to
14 inches from surface or greater if the material
spray will cover satisfactorily. NOTE:
Good
Hydra-Spray technique is very similar to con
ventional spraying with air, except for the
greater distance spray tip should be held from
work surface, the larger coating thickness pro
duced which results in less pattern overlapping
and the positive action used vdien triggering gun.
NOTE: Refer to the SERVICE DIAGNOSIS CHART
in this Instruction Sheet for assistance in lo
cating troubles which may occur during spraying.
Also refer to separate Instruction Sheets for
specific information pertaining to the spray gun,
pump, regulator and manifold or filter.
SAFETY PRECAUTIONS
The Ifydra-Spray equipment develops extremely
high material pressure which remains in the system
until relieved by shutting off the air to pump
and releasing the material pressure by opening
manifold dump valve. In operation, if the fine
high pressure stream of material released from
spray gun is allowed to come in direct contact
with the hand or any part of human body it could
penetrate the skin and cause physical harm.
HANDLE THE HYDRA-SPRAY GUN AS CAPTIOUSLY AS
YOU WOULD ANY GUN: LOADED CR UNLOADED. The fol
lowing safety precautions should be observed;
Never point gun directly at the face.
Never put the hand or fingers directly over
the spray tip. (Use of protective leather gloves
is recommended.)
Never place the tip or gun nozzle directly
in contact with any part of the body.
Always shut off air pressure to pump and re
lieve material pressure in system before attempt
ing to remove gun tip or screen and/or removing
gun for service.
Always remove tip from gun to clean it.
Always tighten threaded connections care
fully and securely, and handle hose carefully to
prevent leaks that could cause physical harm same
as pressurized stream coming from orifice in gun
tip.
Always be sure that the equipment supplying
the material to spray gun is properly grounded
to prevent sparking. The high velocity flow of
material through the spray tip may cause static
electricity to be developed. Use only metal
braid material dispensing hoses or static pro
tected hose. Also be sure to provide for the
proper grounding out of the compressor.