Checkline DCF-900 User Manual
Page 3
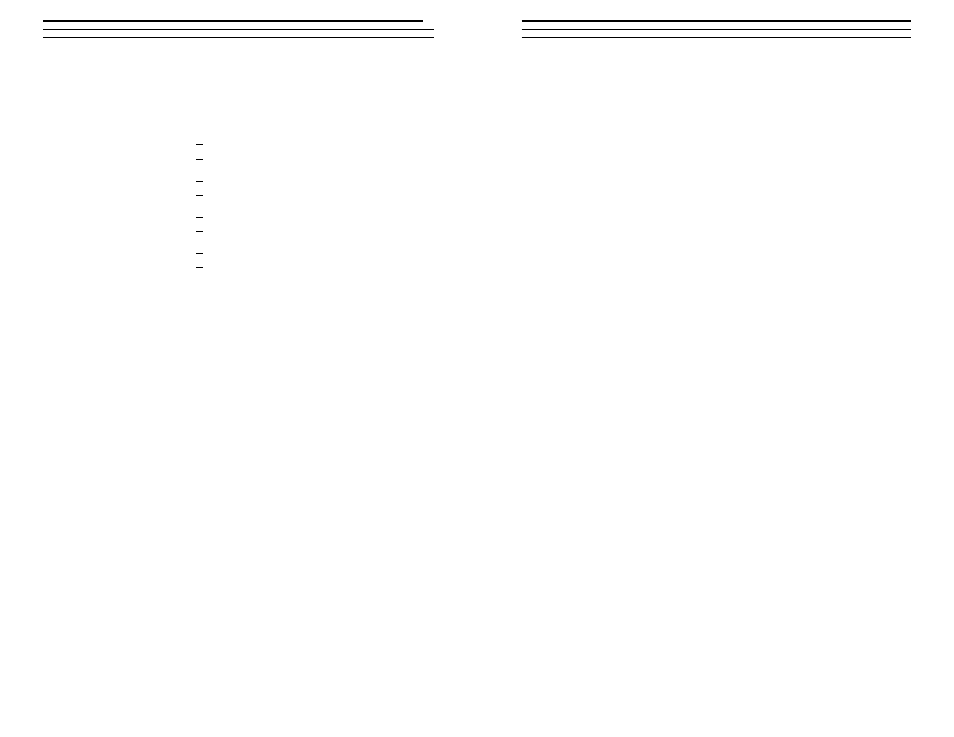
– 14 –
– 3 –
1 0 .0 Spe c ific a t ions
Range:
0.1–40.0 mils (1–999 µm)
Accuracy:
DCF-900
+ 0.1 mil
:
0–10.0 mils
+ 1% reading : 10.0-40.0 mils
+ 1 µm :
0–250 µm
+ 1% reading
:
250-999 µm
DCN-900
+ 0.1 mil
:
0 – 5.0 mils
+ 2% reading :
5.0 –40.0 mils
+ 1 µm :
0–50 µm
+ 2% reading
:
50-999 µm
Note: Accuracy limits require that
calibration be made near the measured
thickness.
Resolution:
0.1 mil (1 µm)
Battery/Life:
9 Volt Alkaline / Approx. 6 months
Dimensions:
5.7 x 3.1 x 1.5" (145 x 79 x 38 mm)
Weight:
9 oz. (250 g)
Temp. Limits:
Material: 15 to 140° F (–10 to 60° C)
Ambient: 32 to 125° F (0 to 50° C)
Cal. Standards: One steel plate (DCF),
One aluminum plate (DCN)
and two plastic calibration shims
Warranty:
1 year
2 .0
Ope ra t ing Princ iple & Applic a t ions
2.1 DCF-900
When a magnet is brought into direct contact with a bare magnetic
metal surface, a magnetic flux circuit is created. The amount of
flux created depends on the strength of the magnetizing force and
the magnetic reluctance of the bare metal. A non-magnetic coating
or metal plating placed in the path of a magnetic flux circuit will
create a “magnetic gap” which will increase the reluctance of the
circuit. This will then cause a decrease in the circuit flux, propor-
tional to the thickness of the coating or plating. CHECK•LINE®
Coating Thickness Gauges measure this decrease in flux intensity
to provide an accurate, direct indication of the coating or plating
thickness being measured.
The Model DCF-900 gauge measures the thickness of all non-mag-
netic coatings, finishes and metal plating on iron, steel and other
magnetic alloy surfaces. (Examples: paint,powder coatings, plastic,
paper, ceramic, rubber, chrome, electroless nickel, brass, non-mag-
netic stainless steel, tin, zinc, cadmium, etc. . . on iron or steel
2.2 DCN-900
An eddy-current-producing probe brought into direct contact with a
bare metal surface, creates a magnetic flux circuit. The amount of
flux depends on the frequency and strength of the eddy-current
force and the magnetic reluctance of the bare metal. A non-metal-
lic, non-conducting coating placed in the path of a magnetic flux
circuit will create a “magnetic gap” which will increase the reluc-
tance of the circuit. This causes a decrease in the circuit flux, pro-
portional to the thickness of the coating. CHECK
•
LINE
®
Coating
Thickness Gauges measure this decrease in flux intensity to pro-
vide an accurate, direct indication of the coating thickness.
The Model DCN-900 gauge will measure the thickness of all
non-metallic, non-conducting coatings, finishes and films on all
non-ferrous metals. (Examples: Anodizing, paint, powder coatings,
plastic, paper, ceramic and rubber on aluminum, brass, bronze,
titanium, non-magnetic stainless steel, zinc, etc.)