5 practicing with the encapsulator, using water, Practicing with the encapsulator, using water, 6 .5 practicing with the encapsulator, using water – BUCHI Encapsulator B-390 User Manual
Page 35
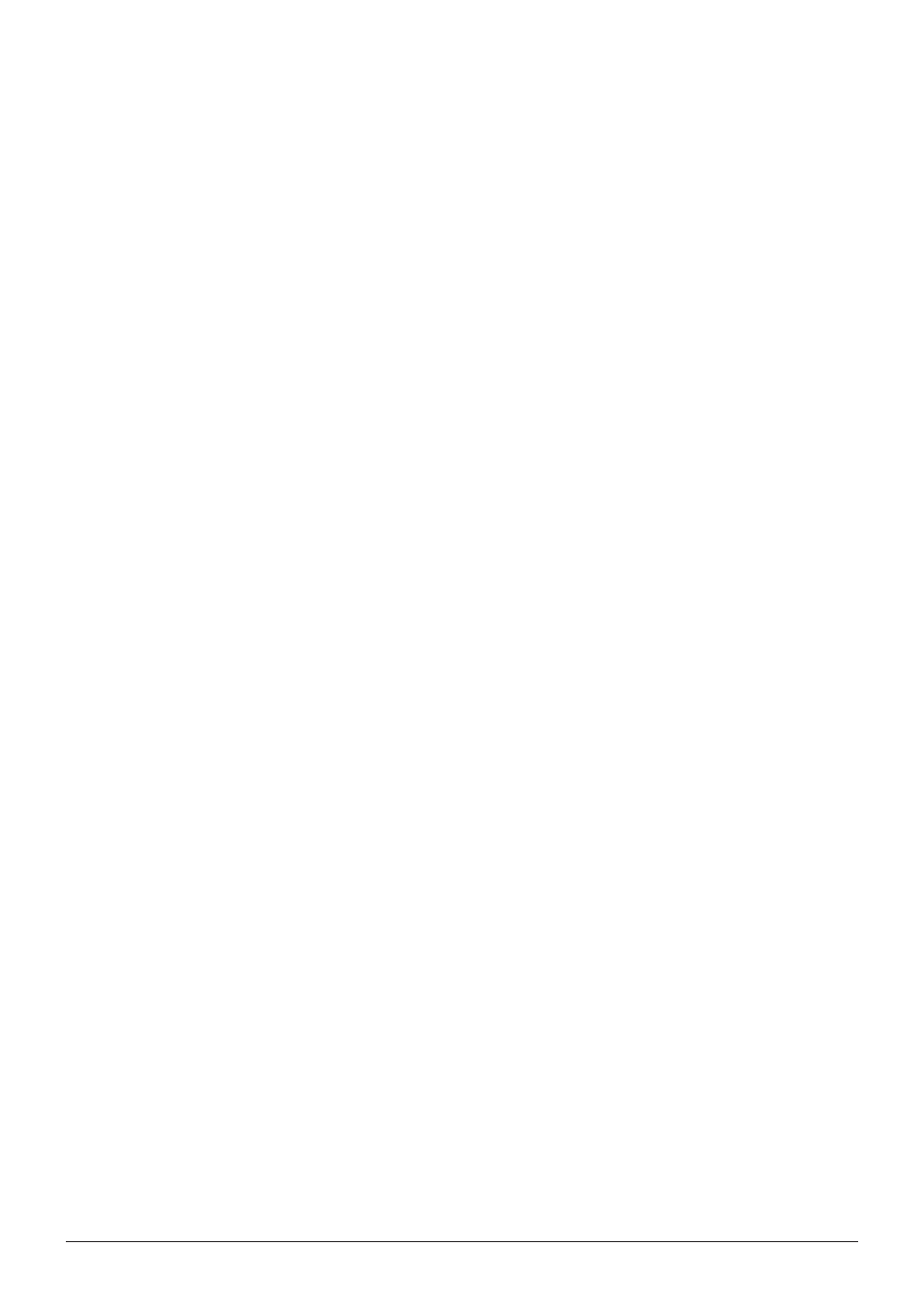
6 Operation
35
B-390
Operation Manual, Version C
6 .5
Practicing with the Encapsulator, using water
Before working with encapsulation polymers, use water for practicing with the Encapsulator to
become familiar with the effects of the controls.
1. Assemble the bead producing unit, screw the 0.30 mm single nozzle to the bead producing unit
and attach all on the carrier plate with the screw (M3×25). Fix the electrode. Place the vibration
unit on the bead producing unit.
2. Fill the pressure bottle with 200 to 300 mL distilled water and screw on the assembled cap. Pass
the silicon tube (4×7 mm) between the blades of the flow regulating valve and attach the male luer
lock fitting of the silicon tube to the female luer lock fitting of the bead producing unit. Squeeze the
valve by turning the knob clock wise so that the silicon tube is closed.
3. Open the external pressurized air supply. The air inlet pressure is optimally at 1.5 to 2 bar (20 to 30
psi). However the system tolerates air inlet pressures of up to 7 bar (100 psi).
4. Set the air outlet pressure to 0.2 bar with the pressure regulating valve. Check the readout periodi-
cally to verify that the air pressure still corresponds to the set value. Activate the vibration control
system and set the frequency at 800 Hz.
5. Open the flow regulating valve by turning the knob counter-clock wise until the water flows
through the silicone tubing and the bead producing unit to the nozzle where it forms a continuous
liquid jet. Adjust the liquid flow and/or the frequency to obtain a good bead chain in the light of the
stroboscope lamp. The desired setting is when the beads within the bead chain are clearly sepa-
rated for several centimeters, starting 3 to 5 mm below the nozzle. Record the position of the flow
regulating valve for this desired setting.
6. Increase the vibration frequency until the bead chain becomes unstable. Then increase the liquid
flow rate by slowly increasing the air pressure until a uniform bead chain is restored. Repeat this in
the opposite direction by decreasing the flow rate and compensating by decreasing the vibration
frequency. This may be done until you become familiar with the relationship between these two
settings. Record the values in table 6-1.
NOTE
• The liquid flow rate and the vibration frequency influence each other within a given working range.
The working range itself is mainly determined by the nozzle diameter and the viscosity of the polymer
mixture.
• An air pressure setting between 0.05 to 0.15 bar is sufficient to pump distilled water.
Greater
working pressures indicate problems such as a clogged nozzle.
General Rules:
• Higher frequencies generate smaller bead sizes.
• Lower liquid flow rates generate smaller bead sizes.