Intake centerline method – COMP Cams COMP4-102 User Manual
Page 3
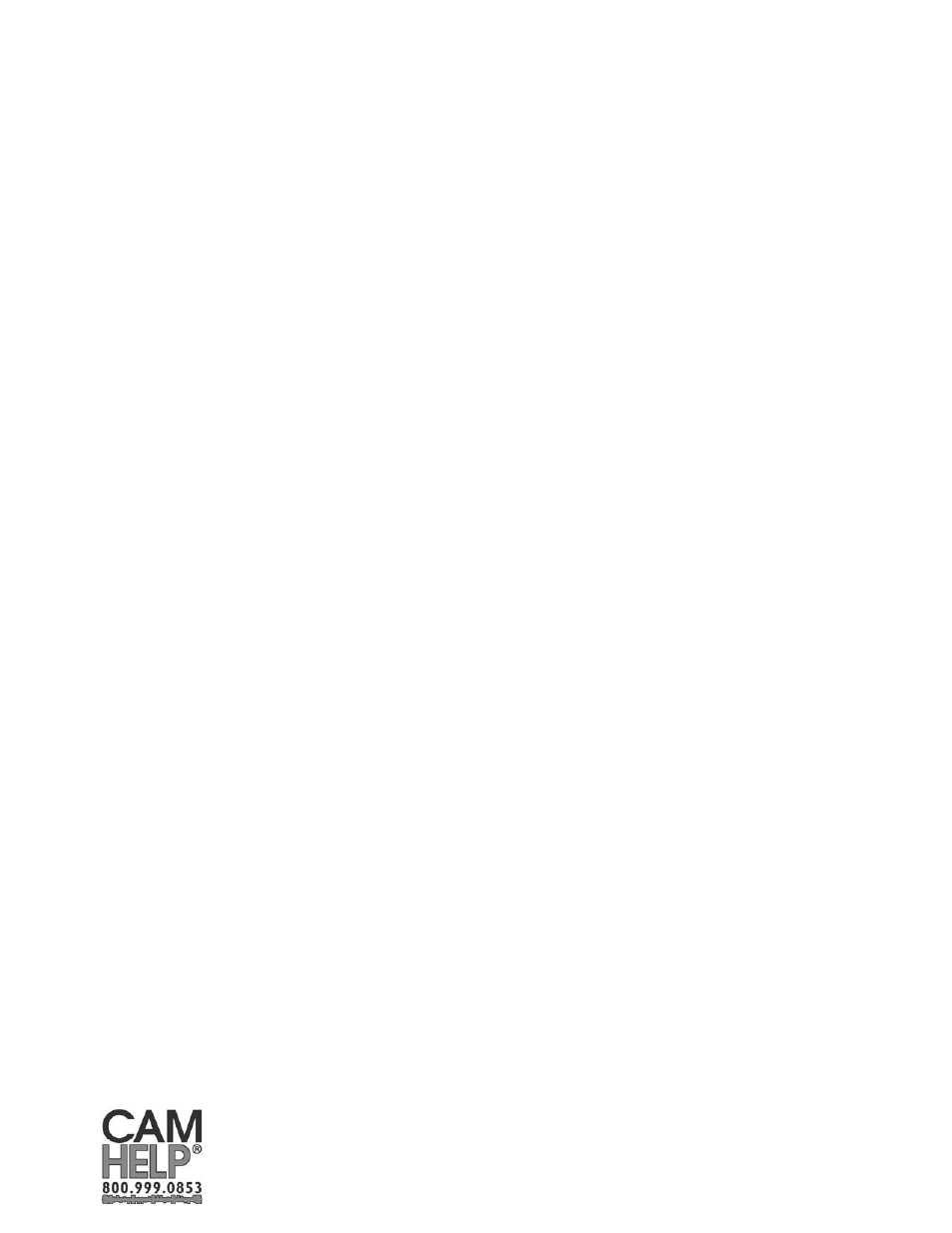
COMP Cams®
3406 Democrat Rd.
Memphis, TN 38118
Phone: (901) 795-2400 Fax: (901) 366-1807
www.compcams.com
Part # COMP4-102
Revised 7/10/06
Intake Centerline Method
There are several accepted ways to degree a camshaft. COMP Cams® suggests the intake centerline method as
the easiest and most accurate. This method of cam degreeing is very practical and indifferent to engine design
characteristics. It simply involves positioning the center, or point of maximum lift, of the #1 intake lobe with
Top Dead Center (TDC) of the #1 piston. The intake centerline method still requires accuracy to be correct, but
it is somewhat forgiving. Once you have degreed a camshaft using this method, you will be surprised at its ease.
Step 1: The camshafts and timing chains have been installed. Make sure that the timing marks on the cam and
crank gears are aligned properly with the copper coated timing chain links as per the camshaft installation
instructions.
Step 2: Position the #1 piston at Top Dead Center (TDC). Attach the degree wheel to the balancer or crank
socket, and install the assembly on the crankshaft. The crank may be rotated from either the front or from the
flywheel end. Obviously, if the engine is in the car, you must rotate from the front. Remember, the greater the
leverage, the smoother the crank rotation and the more accurately you can rotate the crankshaft. Install degree
wheel and pointer and set the pointer to zero on the degree wheel. Note: Never use the starter to turn the
engine while degreeing a cam.
Step 3: Rotate the crankshaft opposite the engine rotation direction about 15-20 degrees. This will lower the
piston enough to permit the installation of the piston stop in the #1 spark plug hole. Rotate the crankshaft
clockwise until the piston hits the stop, and record the number indicated on the degree wheel. Next, rotate the
crankshaft counterclockwise until the piston hits the stop from the other direction, and again record the number
on the degree wheel.
Step 4: Remove the piston stop after marking the two points on the degree wheel. Rotate the crankshaft to the
midpoint of the two marks (this is determined by adding the two points that you marked on the degree wheel
together, then dividing by 2). This point is TDC for cylinder #1.Without rotating the crankshaft adjust the degree
wheel to read 0 degrees at the pointer. You are now ready to locate the exhaust lobe centerline relative to TDC.
If you are not absolutely sure that your zero degree mark is set at TDC, repeat this procedure. This step is
critical to proper camshaft alignment.
Step 5: Attach the dial indicator to the dial indicator mount. Position the dial indicator mount so the tip of the
dial indicator extension/plunger will contact the retainer of the #1 exhaust valve spring. Note that although this
is the “intake centerline” method, the exhaust cam drives the intake cam on a 4.6-liter 4 valve engine, which
necessitates verifying the exhaust centerline first. It is important that the indicator plunger be parallel to the
valve stem. Any variance in the angle of the indicator will introduce geometric errors into the lift readings.
Step 6: Rotate the clockwise until the camshaft reaches maximum exhaust lift. The dial indicator will begin to
change direction at the point of maximum lift. At this point, set the dial to zero.
Step 7: Rotate the crankshaft counterclockwise until the dial indicator reads .100”. Next, turn the engine
forward in the normal direction of rotation until the dial indicator reads .050” before maximum lift. Record the
degree wheel reading.
Step 8: Continue to rotate the engine over in its normal direction of rotation until the indicator goes past zero to
.050” on the closing side of maximum lift. Again, record the degree wheel reading.
Step 9: Add the two numbers together and divide by 2. The resulting number will be the location of maximum
lift of the exhaust lobe in relation to the crank and piston. This is the exhaust centerline. For example: The first
degree wheel reading was 106 degrees. The second reading was 130 degrees. These two numbers (106 + 130)
added together will be 236. 236 divided by 2 will equal 118. Your actual exhaust centerline is 118 degrees.
Verify that your measured exhaust centerline matches that listed on your camshaft specification card.