Taylor-Wharton High Capacity GST Storage Tanks User Manual
Page 22
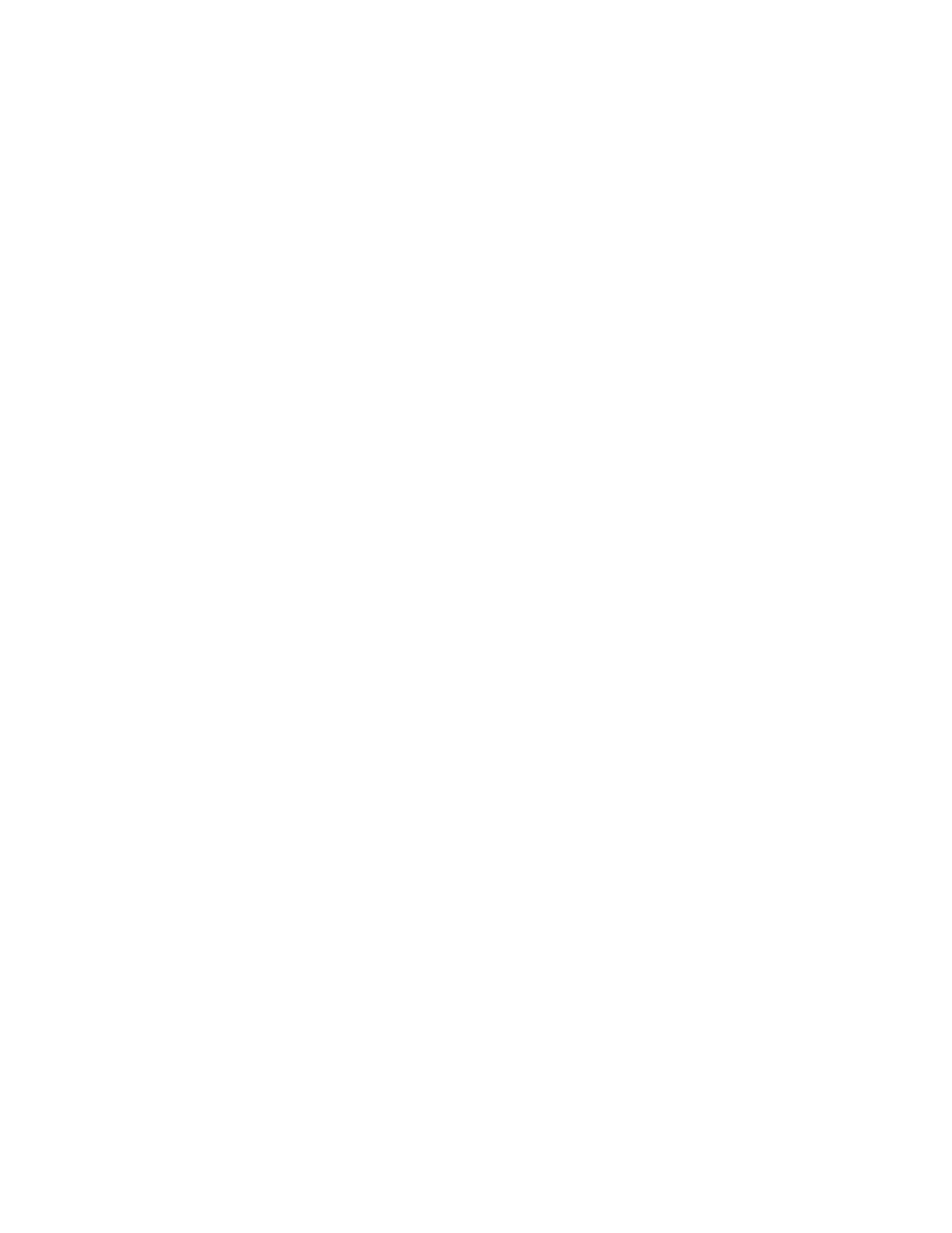
22
MAINTENANCE
GENERAL
The need for maintenance usually becomes apparent from inspection of the tank before filling,
routine observation during and after filling, and indications of improper operation. Typical trouble
indications would be unusually high or low tank or pipeline pressure, leakage from valves or piping
connections, and excessive venting through relief valves. Prompt action to correct damage or
malfunction is required to assure reliable operation. Keep a permanent log of all inspections,
vacuum readings, and repairs performed. Such a log can be valuable in evaluating tank
performance and scheduling maintenance.
Always observe the safety precautions at the front of this manual and follow the instructions given
in this section. Before working on the tank or piping system, isolate the piping section to be
repaired from the tank, and relieve pressure on the component or piping.
Do not allow unqualified persons to attempt repairs on this equipment. Field repairs to instruments
and controls must be made by a qualified instrument specialist. Refer to the Trouble-Remedy
Guide in this manual for assistance in troubleshooting.
Make certain all parts that will come in contact with cryogenic liquid or gaseous product have been
cleaned for in conformance with CGA Pamphlet G-4.1, "Cleaning Equipment for Oxygen Service",
or other equivalent standard. If parts are purchased cleaned for oxygen service, they should be
suitably packaged to prevent contamination.
LEAK TESTING
After making repairs requiring disassembly or part replacement, leak test all valves or piping joints
that were taken apart and reconnected. Apply the leak detector to the test surface per the
manufacturer's instructions. Large leaks instantly form large bubble clusters, while fine leaks
produce white foam that builds up more slowly. All leaks must be repaired and retested before the
tank is returned to service.
WARNING: For O
2
System Users: Residue of leak detectors can be flammable. All
surfaces to which the leak detector solutions have been applied must be
adequately rinsed with potable water to remove all traces of residue.
Reference CGA G-4.1. Section 5.
HAND VALVES
The most common trouble with manual valves will be leakage at the stem packing. Packing leaks
are usually indicated by frost or ice accumulation more than half way up the valve stem extension.
If packing leakage cannot be stopped by tightening, add or replace packing. Use preformed
packing, which can be ordered from the valve manufacturer.
Standard maintenance practices apply to the replacement of seats and discs in globe and gate
valves. Replacement parts may be ordered from the valve manufacturer. Provide the factory part
number marked on the valve for identification.