Taylor-Wharton High Capacity GST Storage Tanks User Manual
Page 12
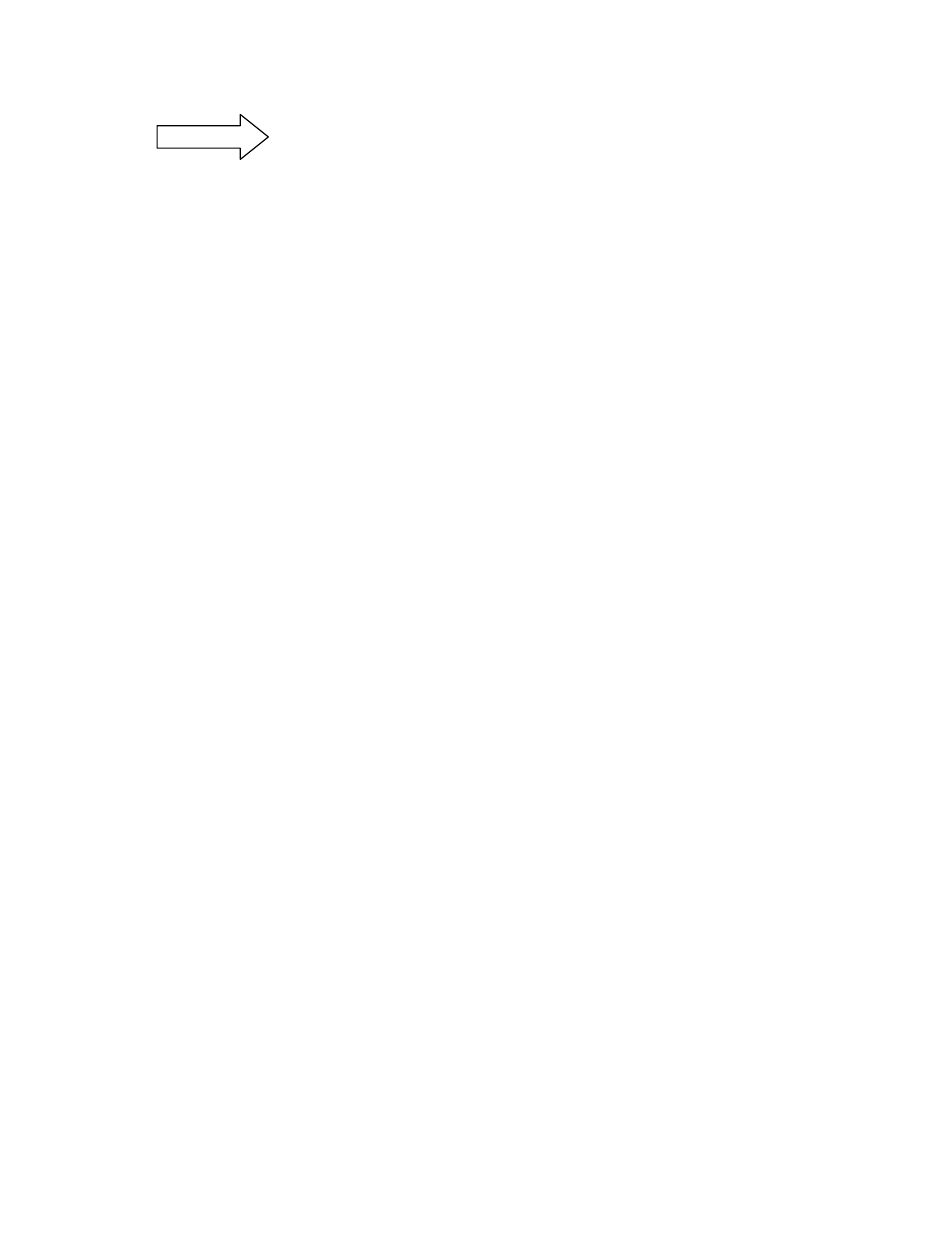
12
rigging equipment has adequate rated capacity to handle the tank weight listed in the specifications.
This tank must be shipped and lifted empty, and with a warm inner vessel.
CAUTION
: To prevent possible tip over, do not leave the tank standing upright unless it
is on a specified foundation or other hard surface capable of supporting its
weight. Loading on the tank legs is great enough to cause them to sink into
most surfaces other than reinforced concrete.
INSTALLATION CHECKS
Before off-loading the tank, inspect it carefully for possible shipping damage. Report any damage
to the carrier and the factory. In addition, check tank pressure and vacuum as follows:
1.
Tanks are shipped pressurized with nitrogen gas at 20 psig (1.38 bar/138 kPa). Open the
gauge VAPOR PHASE ISOLATION VALVE and read tank pressure indicated on
PRESSURE GAUGE or a pressure gauge installed by user. Record the "as received" tank
pressure. Close the VAPOR PHASE ISOLATION VALVE.
Tank pressure may change due to temperature variations, accidental opening of valves,
packing leaks, or minor leaks at the FILL CONNECTION. If a positive pressure is not
indicated on the pressure gauge and no repairable leaks are found, contact the factory in
accordance with conditions specified in the tank warranty.
2.
Check insulation space vacuum by connecting a Hasting-Raydist Model TV-4A or VT-6
vacuum gauge to the tank VACUUM PROBE. Open the tank VACUUM PROBE
ISOLATION VALVE, wait 30 minutes, and take a reading. If the "as received" vacuum
(tank at ambient temperature) is greater than 250 microns (0.25 mm Hg) absolute, contact
the factory.
3.
Attach a tag to the tank at the FILL CONNECTION indicating the normal operating
pressure range of the tank. This information enables an operator to monitor tank pressure
during a tank fill and prevents pressure upsets caused by improper fill procedures.
CUSTOMER INSTALLED EQUIPMENT
Designing safe and effective cryogenic systems requires extensive knowledge and experience.
Persons lacking the necessary skills are urged to seek competent advice before attempting to design
cryogenic system.
When installing vaporizing and control equipment, be sure to follow accepted design practices for
cryogenic equipment. All equipment must be cleaned for oxygen service. Be sure to include
pressure relief valves in piping where product could be trapped between closed valves, regulators,
etc. and cause over-pressurization due to fluid expansion.