Culligan Iron-Cleer User Manual
Page 19
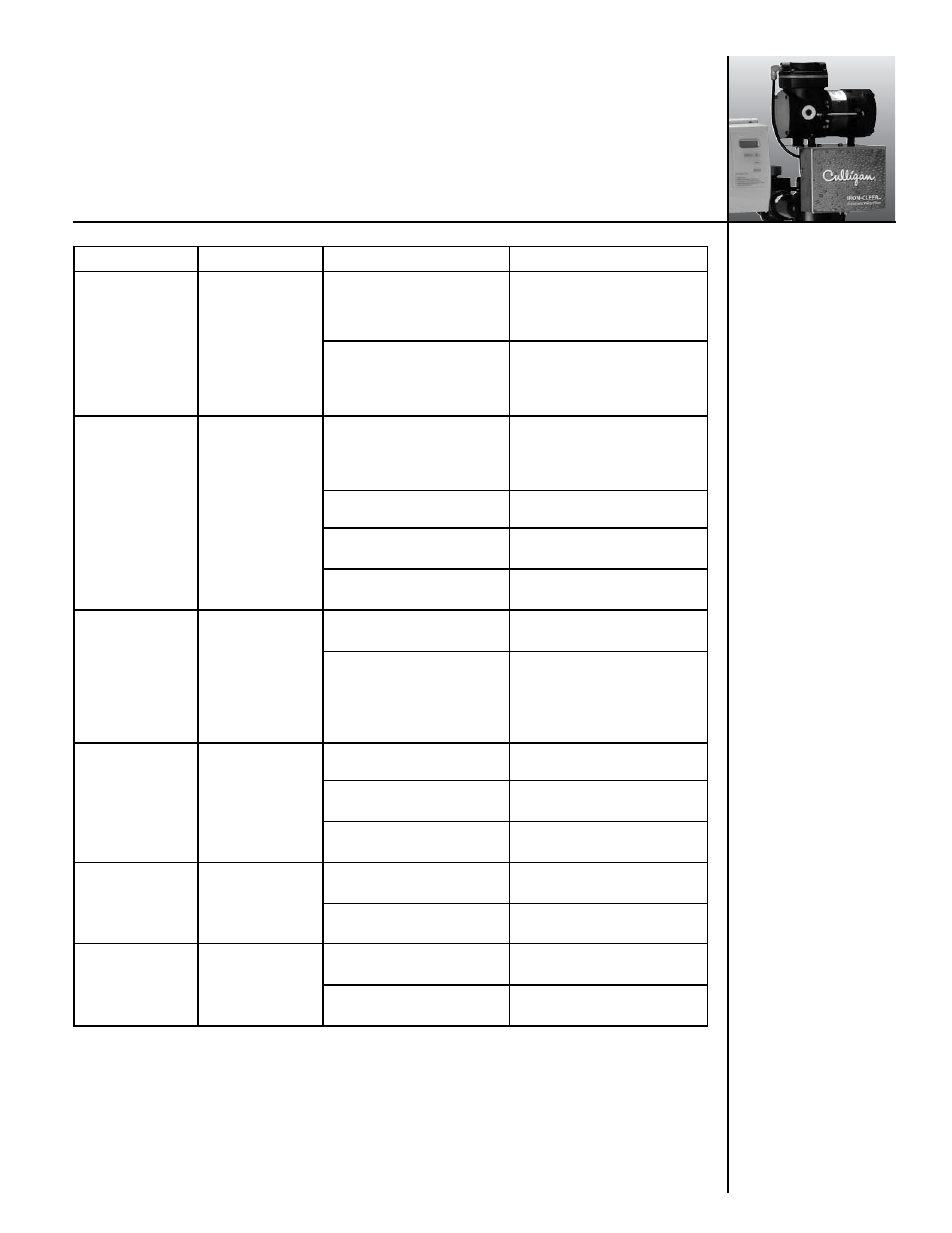
15
Complaint
Problem
Cause
Solution
Excessive
noise during
regeneration.
A. Howling
or whistling
noise during
regeneration
cycle.
1. Inadequate drain line
size.
1. Call your Culligan dealer
for service.
2. Drain line is vibrating
against other pipes,
conduits, pipe hangers, heat
ducts, floor joists,etc.
2. Call your Culligan dealer
for service.
Water is
running to drain
continuously.
A. Control
valve is stuck
in regeneration
cycle.
1. Electrical service
to control(s) has been
interrupted.
1. Assure continuous
electrical service is available.
(check plug, breaker, fuse,
etc.)
2. Faulty circuit board.
2. Replace circuit board..
3. Faulty drive motor.
3. Call your Culligan dealer
for service.
4. Foreign material lodged
in piston.
4. Call your Culligan dealer
for service.
Blue green
staining.
A. Corrosive
water condition in
copper distribution
piping system.
1. Low pH condition of the
raw water supply.
1. Call your Culligan dealer
for service.
2. In rare occasions,
highly aerated water in
combination with a specific
water supply can create a
slightly corrosive condition.
2. Call your Culligan dealer
for service.
Compressor
doesn’t run.
1. Compressor unplugged.
1. Plug it in.
2. Relay settings incorrect.
2. Call your Culligan dealer
for service.
3. Bad relay.
3. Call your Culligan dealer
for service.
Compressor run
with excessive
noise.
1. Dead head pressure is
65 psi.
1. Call your Culligan dealer
for service.
2. Dead head pressure is
65 psi.
2. Call your Culligan dealer
for service.
Compressor runs
continuously.
1. Incorrect relay settings
1. Call your Culligan dealer
for service.
2. Bad relay.
2. Call your Culligan dealer
for service.