Preventative maintenance – Viking Pump TSM000: General Information User Manual
Page 7
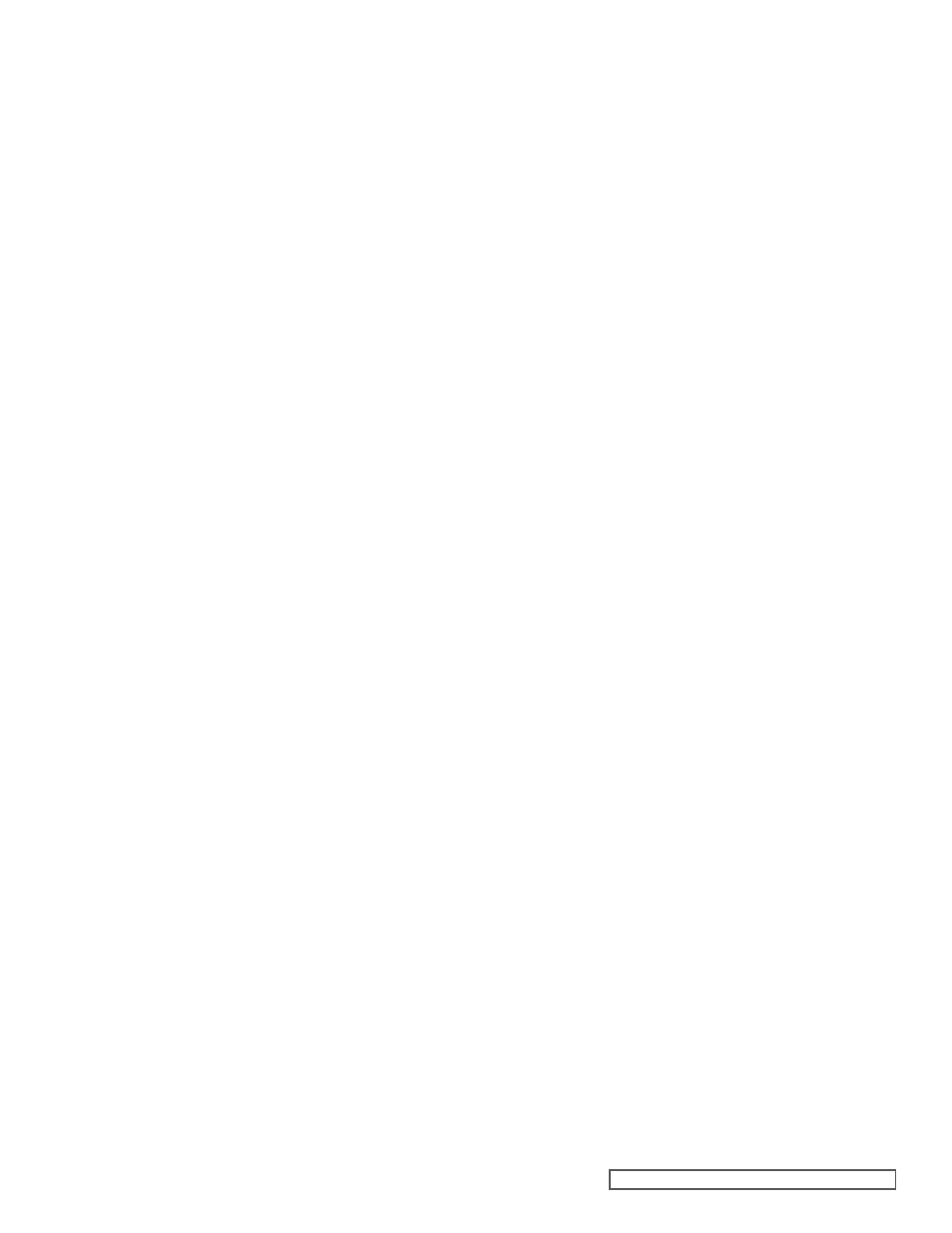
SECTION TSM 000
ISSUE
I
PAGE 7 OF 8
pressure gauge - discharge port
1. high reading would indicate -
a) High viscosity and small and/or long discharge line
b) Gate valve partially closed
c) Filter plugged
d) Vertical head did not consider a high specific gravity liquid
e) Line partially plugged from build up on inside of pipe
f) Liquid in pipe not up to temperature
g) Liquid in pipe has undergone a chemical reaction and has
solidified
h) Relief Valve set too high
2. Low reading would indicate -
a) Relief valve set too low
b) Relief valve poppet not seating properly
c) Bypass around the pump partially open
d) Too much extra clearance
e) Pump worn
3. fluttering, jumping, or erratic reading -
a) Cavitation
b) Liquid coming to pump in slugs
c) Air leak in suction line
d) Vibrating from misalignment or mechanical problems
Some of the following may also help pinpoint the problem:
A) pump does not pump.
1. Lost its prime - air leak, low level in tank, foot valve stuck
2. Suction lift too high
3. Rotating in wrong direction
4. Motor does not come up to speed
5. Suction and discharge valves not open
6. Strainer clogged
7. Bypass valve open, relief valve set too low, relief valve
poppet stuck open
8. Pump worn out
9. Any changes in the liquid system, or operation that
would help explain the trouble, e g new source of
supply, added more lines, inexperienced operators, etc
10. Too much end clearance
11. Head position incorrect See fig. 3.
b) pump starts, then loses its prime.
1. Supply tank empty
2. Liquid vaporizing in the suction line
3. Air leaks or air pockets in the suction line; leaking air through
packing or mechanical seal
4. Worn out
C) pump is noisy.
1. Pump is being starved (heavy liquid cannot get to pump fast
enough) Increase suction pipe size or reduce length
2. Pump is cavitating (liquid vaporizing in the suction line)
Increase suction pipe size or reduce length; if pump is
above the liquid, raise the liquid level closer to the pump; if
the liquid is above the pump, increase the head of liquid
3. Check alignment
4. May have a bent shaft or rotor tooth Straighten or replace
5. Relief valve chatter; increase pressure setting
6. May have to anchor base or piping to eliminate or reduce
vibration
7. May be a foreign object trying to get into the pump through
the suction port
d). pump not up to capacity.
1. Starving or cavitating - increase suction pipe size or reduce
length
2. Strainer partially clogged
3. Air leak in suction piping or along pump shaft
4. Running too slowly; is motor the correct speed and is it
wired up correctly
5. Bypass line around pump partially open
6. Relief valve set too low or stuck open
7. Pump worn out
Performing a few preventative maintenance procedures will extend
the life of your pump and reduce the overall cost of ownership
A) Lubrication - Grease all grease fittings after every 500 hours
of operation or after 60 days, whichever occurs first If service
is severe, grease more often Do it gently with a hand gun
Use a NLGI #2 grease for normal applications For hot or cold
applications use appropriate grease
See Engineering Service
bulletin ESb-515.
b) packing Adjustment - Occasional packing adjustment may
be required to keep leakage to a slight weep; if impossible to
reduce leakage by gentle tightening, replace packing or use
different type See Technical Service Manual on particular
model series for details on repacking
C) End Clearance Adjustment - After long service the running
clearance between the end of the rotor teeth and the head
may have increased through wear to the point where the pump
is losing capacity or pressure Resetting end clearance will
normally improve pump performance See TSM on particular
model series for procedure on adjusting end clearance for
pump involved
d) Examine internal parts - Periodically remove the head,
examine idler and bushing and head and pin for wear
Replacing a relatively inexpensive idler bushing and idler pin
after only moderate wear will eliminate the need to replace
more expensive parts at a later date See TSM on particular
model series for procedure in removing head of the pump Be
sure idler does not slide off idler pin as head is removed and
drop and hurt someone or damage the part
E) Cleaning the pump - A clean pump is easier to inspect,
lubricate, adjust, and runs cooler; plus, it looks better
f) Storage - If pump is to be stored, or not used for six months or
more, pump must be drained and a light coat of non-detergent
SAE 30 weight oil must be applied to all internal pump parts
Lubricate fittings and apply grease to pump shaft extension
Viking suggests rotating pump shaft by hand one complete
revolution every 30 days to circulate the oil Retighten all
gasketed joints before using the pump
prEvENTATivE MAiNTENANCE
8. Too much end clearance
9 Head position incorrect See fig. 3.
E) pump takes too much power.
1. Running too fast - Is correct motor speed, reducer ratio,
sheave size, etc being used?
2. Is liquid more viscous than unit sized to handle; heat the
liquid, increase the pipe size, slow the pump down, or get a
bigger motor
3. Discharge pressure higher than calculated, check with
pressure gauge Increase size or reduce length of pipe,
reduce speed (capacity), or get bigger motor
4. Packing gland drawn down too tight
5. Pump misaligned
6. Extra clearance on pumping elements may not be sufficient
for operating conditions Check parts for evidence of drag or
contact in pump and increase clearance where necessary
f) rapid wear.
On most applications the pump will operate for many months
or years before it gradually loses its ability to deliver capacity or
pressure Examination of such a pump would show a smooth
wear pattern on all parts Rapid wear, occurring in a few minutes,
hours or days, shows up as heavy grooving, galling, twisting,
breaking or similar severe signs of trouble
SEE ChArT, pAgE 7.