Tweco Torch Data User Manual
Torch operation, Torch parts selection, Pre-setting power supply controls
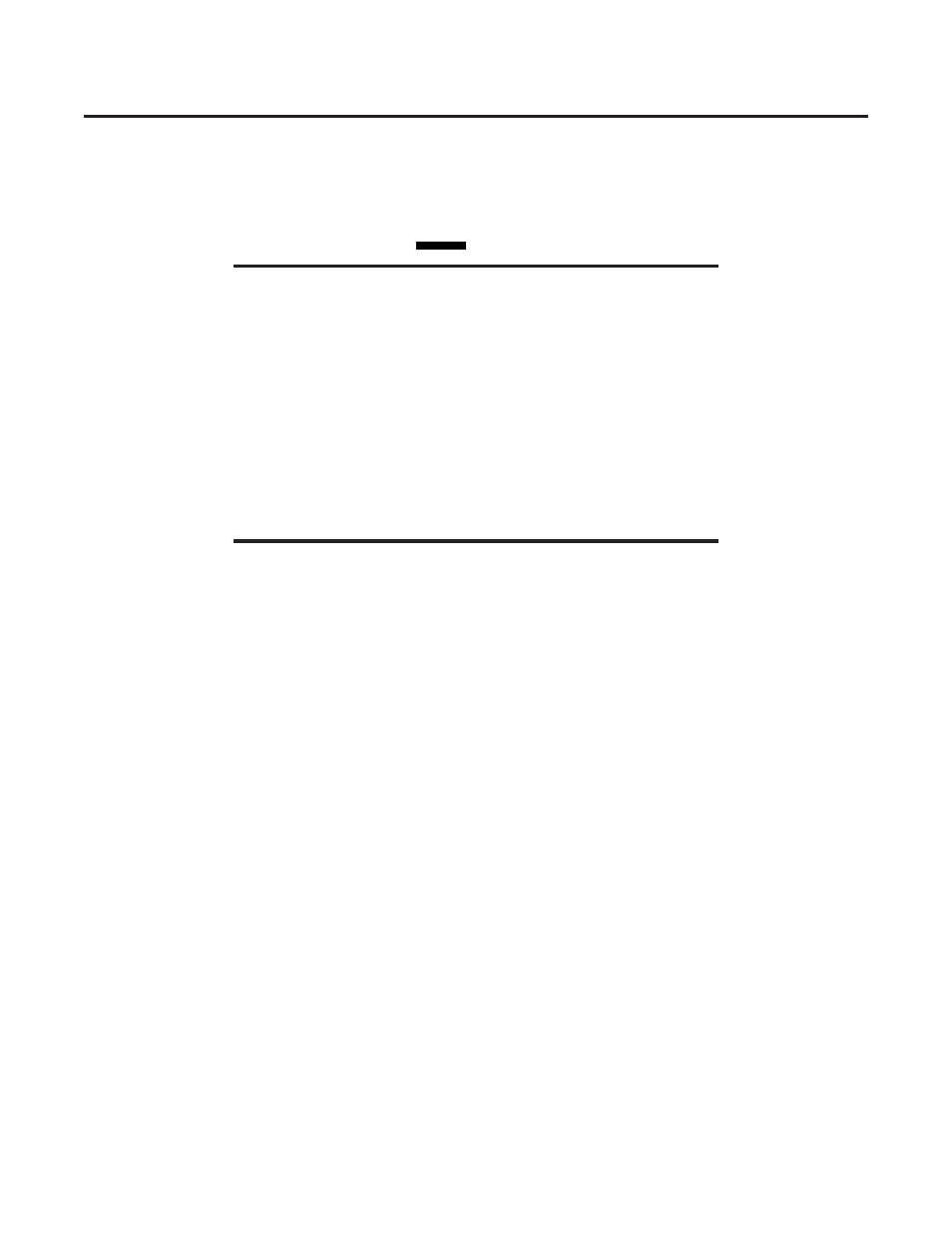
Manual 0-4730 Rev. AF
8-1
TORCH DATA
8. TORCH OPERATION
Torch Parts Selection
The application will determine which torch parts must be used. Refer to the cut charts for the proper torch parts to
install for a selected application.
CAUTION
Do not interchange parts. Make sure all torch parts correspond with the plasma and shield
gases in use for the application.
Pre-Setting Power Supply Controls
Set the Power Supply controls prior to operating the system as described in the power supply Operating Manual.
Refer to the cutting charts for the proper cutting parameters for the application.
Recommended Cutting Speeds
Cutting speed depends on material and thickness. The following factors may affect system performance:
•
Torch parts wear; gas quality and mass flow / pressure; operator experience; torch standoff height; proper
work cable connection; alloy content of material; cutting table capabilities & accuracy.
NOTE
This information represents realistic expectations using recommended practices and well-
maintained systems. Actual speeds may vary from those shown in the charts depending on
the alloy content of the selected material. Voltage ratings may vary depending on the CNC,
cutting table, or height controller.
For complete cutting speed chart data refer to the following pages.
Consumables Notes
Always assemble the consumable parts properly. Improper assembly may damage the parts or the torch head.
Ensure that parts are seated together correctly.
Always check the shield gas distributor for charring when changing parts. Do not use the distributor if it is charred.
Replace the shield gas distributor regularly to ensure proper performance.
Operational Notes
Always purge the torch after changing consumables or if the power supply has been shut off. The power supply's
built-in purge function may not be enough to properly purge the torch. Manually flow gas with the 'Test Cut Flow' and
'Test Pre-Flow' functions to help remove any remaining coolant from the lines.
Slightly increasing the preflow pressure may increase piercing ability on thicker materials. However, increasing the
preflow pressure too much may affect plasma starting reliability (misfiring).
Decreasing preflow pressure may improve piloting. Preflow pressure can be reduced without affecting cut perfor-
mance as long as the pilot arc still transfers to the plate well. Decreasing preflow pressure too much will affect the
ability to transfer the arc to the plate and cause damage to the tip.
Notes on Chart Measurements
Pressure measurements in the charts are in psi(g), not psi(a). 0 psi(g) = 14.7 psi(a) (1 atmosphere).
Ball settings are at the center of the gauge ball.
Ohmic Sensing
Ohmic sensing is not recommended with water shield. Water on the plate interferes electrically with the ohmic
sensing circuit.