1 screw connections, 2 cleaning, 3 modification of the safety valve – Richter KSE-C/F Series Safety Valves User Manual
Page 15: 4 adjustment of the test pressure, 5 important notes on dismantling / installation, 6 replacement of components, 1 dismantling of the plug, Screw connections, Cleaning, Modification of the safety valve
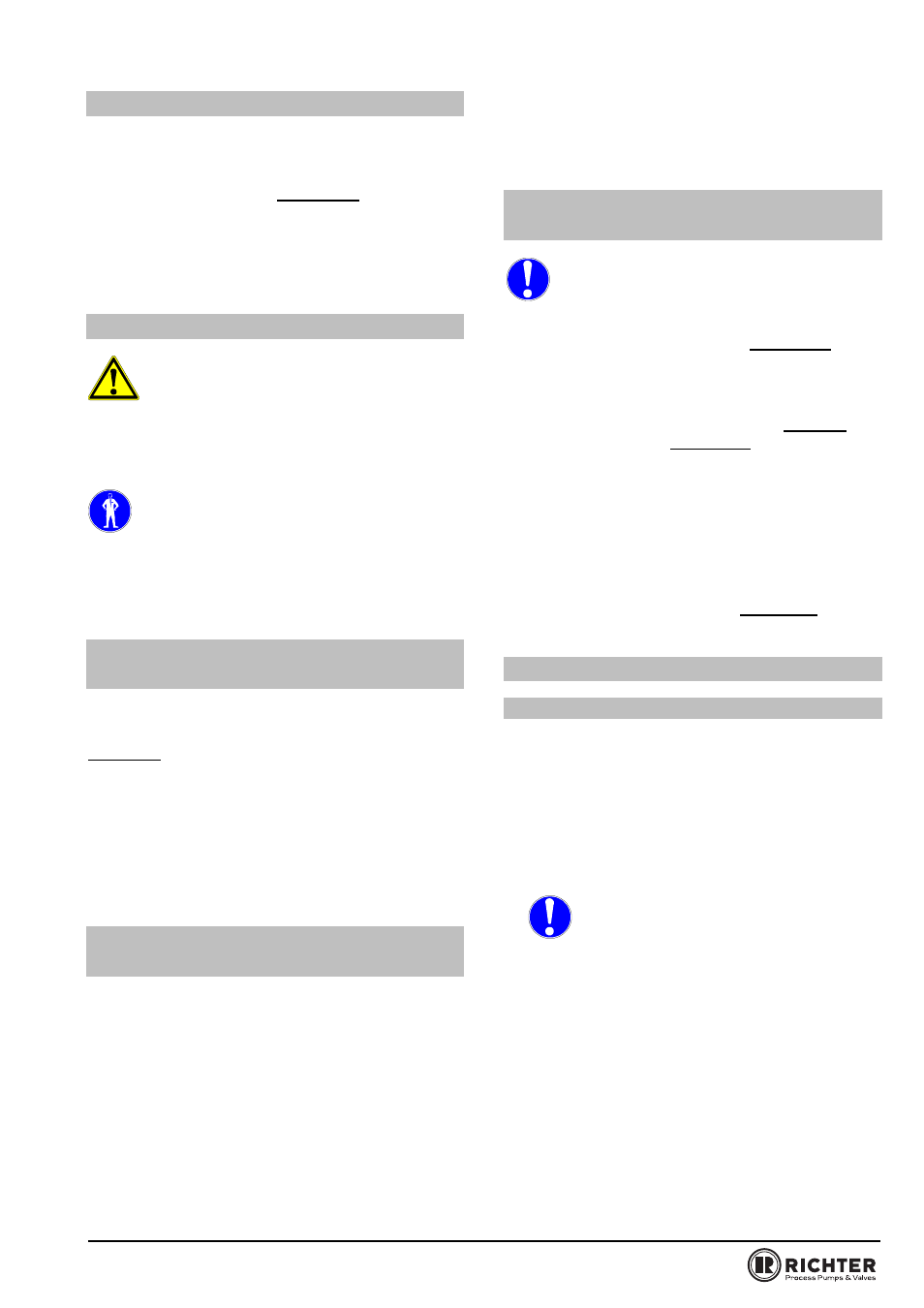
Series KSE/F, KSE-C/F
Page 15
9530-050-en
Revision 04
TM 7489
Edition 03/2009
9.1 Screw connections
To prevent leaks, a regular check of the connection
screws should be made in line with the operating
requirements.
For tightening torques, see Section 1.3.
To prevent screw connections from becoming loose in
the event of pressure fluctuations or plant vibrations,
we recommend the installation of expansion joints or
pulsation dampers.
9.2 Cleaning
Prior to starting any repair work, the valve is
to be thoroughly cleaned. Even if the valve
has been properly emptied and rinsed,
residual medium may still be found in the valve, e.g.
between the lining and body or in the bonnet.
Plastic parts may absorb medium which gradually
emerges from the material after cleaning.
Wear the prescribed protective clothing!
Safety valves which have been cleaned with water or
other media must be dried before re-assembly of the
parts and installation of the valve in the plant.
9.3 Modification of the safety
valve
If modifications to the valve are required, the
manufacturer must always be consulted.
Examples: Modification with changed test pressure,
replacement of the spring or adaption to the mass flow
by reducing the travel.
After
approval
by
the
manufacturer,
these
modifications can be performed either by the
manufacturer or by the customer under the guidance
of a technical supervisory agency or any other
approval authority.
9.4 Adjustment of the test
pressure
Undo locking plate 539, dismantle lifting lever 238
and unscrew the lifting cap 535.
Undo nut 920/3.
Adjust the spring tension with the adjusting screw
538 to the specified test pressure.
Counter adjusting screw 538 with a hex. thin nut
920/3 resp. with centering nut 555 (DN 25/50).
Check test pressure.
Screw on lifting cap 535 and tighten.
Insert lifting lever 238.
Mount locking plate 539.
Have the valve lead-sealed.
The data specified in the test certificates are to be
observed.
9.5 Important notes on
dismantling / installation
First relieve plug 204 and lift it off the seat.
The seat and plug could otherwise be destroyed.
Read the precise instructions in Section 9.6.
Then undo the screws between the body 100 and
the inlet nozzle 122 or between the bonnet 513
and body 100.
Always replace the seat and plug pairwise and
always rework them completely.
Reworking of the seat and plug requires
specialised knowledge of the material as well as
special lapping wheels.
It is therefore recommended to have this work
carried out by the manufacturer.
After dismantling, check all parts for wear and
damage.
Observe sectional drawings in Section 10.
9.6 Replacement of components
9.6.1 Dismantling of the plug
Undo locking plate 539, dismantle lifting lever 238
and unscrew lifting cap 535.
Mark the position of the stem nut 534.
Unscrew the prevailing torque type hexagon nut
929/1 and stem nut 534 off the stem 802.
When undoing or tightening the prevailing torque
type hexagon nut 929/1, carefully hold the spindle
tight with pliers to prevent it from turning.
Do not turn the entire spindle 802!
There is a risk that the insert sleeve 308
will be screwed out of the bellows 206 and
the folds or the spring-type pin 939/1 will be
damaged!
Mount a suitable distance sleeve (not included in
the scope of delivery) over the stem 802.
Screw the stem nut 534 against the distance
sleeve. The plug 204 is lifted off the seat 205 and
the closing force of the valve becomes ineffective.
Loosen the bolts 901/1, 936/1, 936/2 and 920/2 (in
the case of KSE/F and KSE-C/F 100/150 902/2,
934/1, 936/1 and 920/2) and lift the bonnet with
internals completely off.
Grip the bellows 206 in the reinforced section just
above the lifting aid 237. Unscrew the lifting aid off
the bellows and remove the plug 204.