3 discharge conditions and reaction forces, 3 valve connecting dimensions, 4 flange caps and gaskets – Richter KSE-C/F Series Safety Valves User Manual
Page 10: 5 direction of flow and installation, 6 grounding, 7 installation, Discharge conditions and reaction forces, Valve connecting dimensions, Flange caps and gaskets, Direction of flow and installation
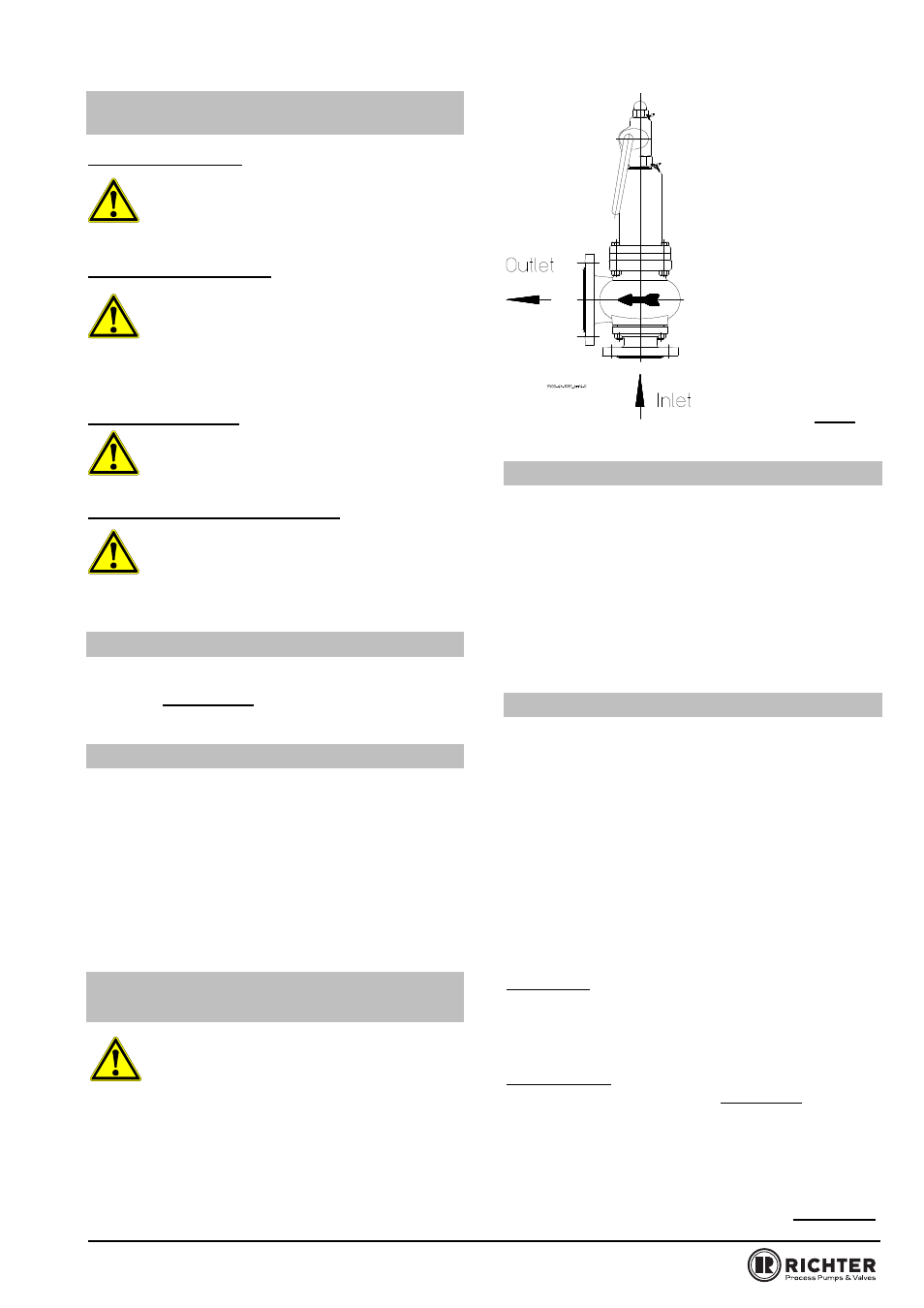
Series KSE/F, KSE-C/F
Page 10
9530-050-en
Revision 04
TM 7489
Edition 03/2009
6.2.3 Discharge conditions and reaction
forces
At low temperatures:
Outlet lines must be protected against
freezing. This applies in particular if gas
cooling as a result of expansion is to be
expected or lines are laid outdoors.
With crystallising media:
In the case of media which tend to
crystallise, solidify or stick, appropriate
action must be taken to ensure that the
solidification process cannot take place in
the inlet or outlet lines or in the body (e.g. installed
rupture disc, insulation, heating).
With gassing media:
In the case of gassing or vaporising liquids,
adequately dimensioned flashtraps must be
located in the direct vicinity of the valve.
Reaction forces during discharge:
The pipes and their holders are to be
dimensioned so that their weight forces and
the reaction forces and thermal loads
produced during discharge can be safely absorbed.
6.3 Valve connecting dimensions
The main dimensions are contained in the sectional
drawing in Section 10.5.
6.4 Flange caps and gaskets
Contamination of or damage to the sealing
surfaces is best avoided if the protective caps
remain on the flanges until just before installation.
If plastic sealing surfaces can be damaged, e.g. with
mating flanges made of metal or enamel, use PTFE-
lined seals with a metal inlay.
These are available as special accessories from the
Richter product range.
6.5 Direction of flow and
installation
When the valve is being installed, the
direction of flow must be observed; it is
indicated by an arrow on the valve body.
A mix-up of the inlet and outlet will result in the
valve becoming ineffective and the bellows may be
destroyed.
Always install the safety valve with the stem in a
vertical position.
Fig. 5
6.6 Grounding
The valve must be grounded. The simplest solution is
to use tooth lock washers which are placed under one
pipe bolt of each flange.
At the customer's request a setscrew M6 with a hex.
nut and washer will be provided at each flange as an
additional grounding connection.
Otherwise grounding must be ensured by different
measures e.g. a cable link.
6.7 Installation
The plant components to be protected are to be
cleaned thoroughly prior to installation of the valve.
Solids jeopardise the soft-sealing, high-precision
surfaces of the seat and plug and permanent leaks
could arise.
The safety valve must be installed so that no
inadmissible mechanical or thermal stresses are
transmitted from the attached pipes to the body.
Changes in length of the pipes due to temperature
are to be allowed for, e.g. through the installation
of expansion joints.
Remove the flange covers.
For KSE/F: Before installation (vales with set
pressures
0.5 bar), remove metallic transport
securing strip and cap nut for securing the valve
during transport. Screw on attached lead-sealed cap
nut 927/1. See Section 5.1.
For KSE-C/F:
Before commissioning, remove
transport securing device. See Section 5.2.
Remove the securing wire between the bonnet 513
and the lifting lever 238.
Position and align the safety valve and any
additional gaskets. Then tighten the pipe screws
with a torque wrench in diametrically opposite
sequence. For tightening torques, see Section 1.3.