S&S Cycle Super Stock and Special Application Crankcases for 1936-99 Big Twin Engines User Manual
Page 14
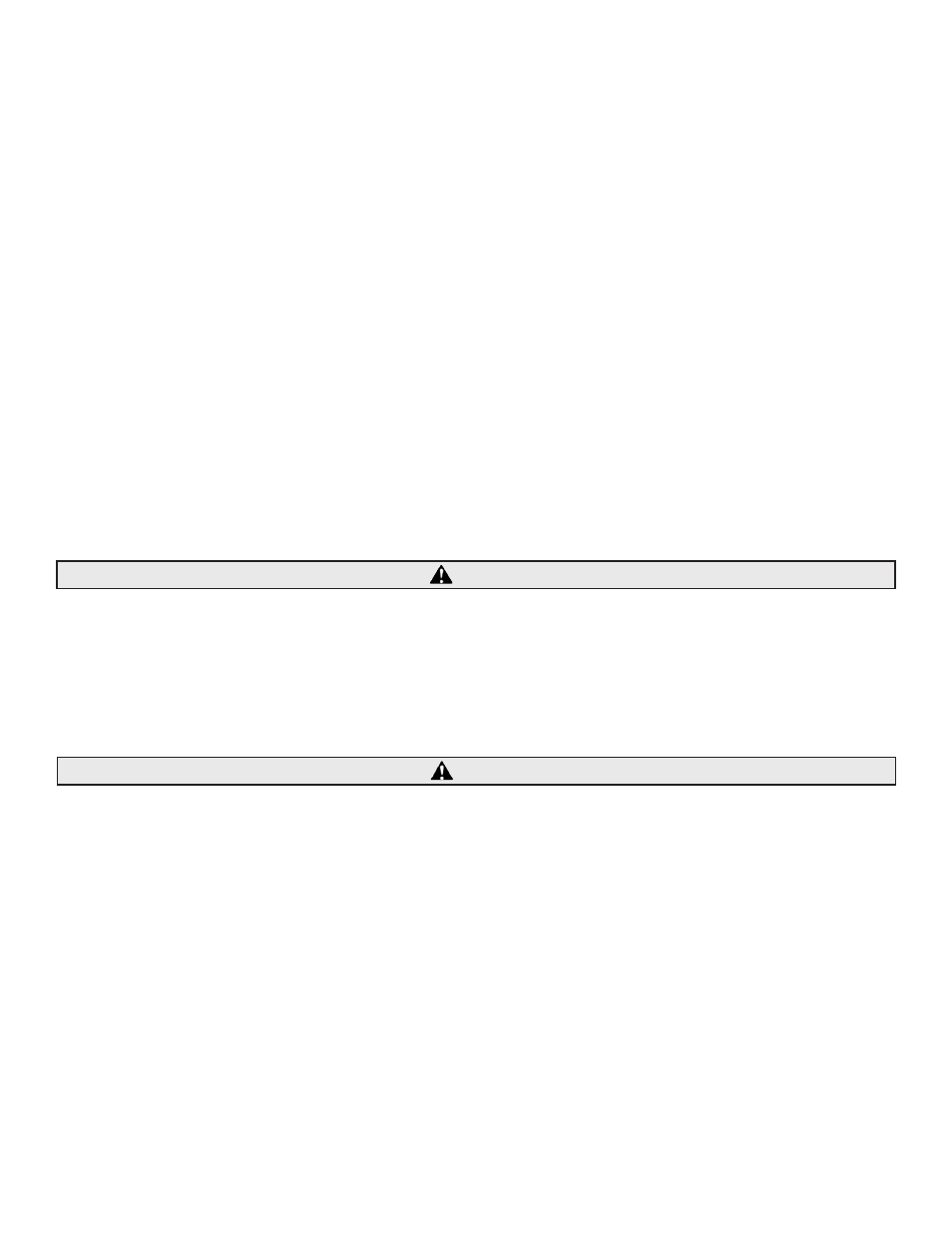
14
F- Breather gear timing - Breather gear window in crankcase is machined to maximum specifications and should require no further machining.
In addition, breather passage between flywheel cavity and breather gear bore is cast in a special “ported” shape designed to optimize flow
of crankcase vapors and oil mist.
G- Oil pump
1- Oil pump compatibility
a- 1936 to 1947 (knucklehead) engines - Original stock cast iron, early stock alloy 1968 to 1969, or S&S 31-6250 oil pump may be used.
Passages in crankcase are machined to provide stock-like oil circulation.
b- 1948 to 1969 (panhead and shovelhead) engines - Original stock cast iron, early stock alloy 1968 to 1969, or S&S 31-6250 oil pump
may be used. Passages in crankcase are machined to provide stock-like oil circulation. However, if S&S 31-6250 pump is used, builder
has option to separate oil supply as in 1973 and later style oiling system. This permits tappets and heads to receive unrestricted oil
supply first Lower end main and connecting rod bearings get secondary oil at lower pressure after top end is supplied.
c- 1970 to present (alternator style) engines - Top end and lower end oil supply passages are separated and pressure relief passage
is drilled as in stock late 1981 and later engines. S&S 31-6260 oil pump kit may be used in this application as may SOME stock alloy
Harley-Davidson® shovelhead pump. Most 1973-1980 stock pumps leave pressure relief passage in crankcase uncovered, resulting
in large oil leak (See Picture 12 on page 6). S&S recommends S&S oil pump for these applications, although stock 1973 - 1980 pump
can be used if exposed passage is plugged according to procedure in Section 2-A.
NOTES
Oiling systems in stock 1973 and later engines have two distinct differences from earlier engines. Oil supplies to top end and bottom end are separated,
•
and connecting rod bearings receive constant oil supply through pinion shaft rather than intermittent supply as in earlier engines. Oil supply is separated
so tappets/heads get oil first at highest possible pressure. In applications where hydraulic tappets are used, this system maintains high oil pressure to
tappets assuring proper operation. After top end components are satisfied, pressure relief valve opens allowing oil to flow to bottom end bearings and
other components. After bottom end is satisfied, relief valve opens further allowing excess oil to flow to incoming oil supply passage side of pump.
Separate oil supply delivered to bottom end allows change in delivery at pinion shaft from intermittent to constant feed system, hence, end oiling style
pinion shaft. S&S® recommends separating oil supply in generator style cases when hydraulic tappets are used. This is possible only if S&S 31-6250 style
replacement oil pump is used. If stock, cast iron or early alloy pump is used, oil supply cannot be separated and pinion shaft must not be converted to
constant oil feed.
Using stock cast iron oil pump or 1968-1969 alloy pump with constant feed pinion shaft oiling system can result in abnormally low oil
pressure with possible engine damage as a result.
If stock alloy pump is used, proper identification to confirm it is correct type is imperative. Different year alloy pumps have design changes that could
•
interfere with oil circulation if used with wrong style crankcases. Some early stock alloy pumps will also cause pressure relief passage in S&S crankcase
to be uncovered, resulting in large oil leak.
Pump and other parts such as pinion shaft and pinion shaft bushings, rocker shafts and rocker shaft bushings, lifters and lifter guides must be serviceable
•
and in good condition to insure proper oil pressure and circulation.
Insufficient oil supply may result in premature wear or damage to critical engine components.
2- Crankcase oil supply passages - 1948 to 1969 (generator style) crankcase only. See Pictures 4 & 5.
a- Engines using stock cast iron or early stock alloy oil pump assembly or S&S 31-6250 pump and solid tappets.
1- Thread 50-0024 socket head set screw (See Line Drawing, item 47) into hole F until it bottoms out.
2- Top of screw should be flush with or slightly below gasket surface, but screw should not extend deep enough to block oil
passage G.
b. Engines using hydraulic tappets and S&S oil pump 31-6250
1- Thread 50-0024 socket head set screw (See Line Drawing, item 47) into hole G until it bottoms out.
2- Depth should be between .540” and .600” from gear cover gasket surface. Location of screw should be between holes F and H.
3- Oil pump mounting hardware - Mounting holes are 1⁄4-20 thread. Tighten to 8-10 ft. lbs. Installation hardware is not furnished
due wide variety of possible applications. S&S oil pump kits include mounting screws. Screws are also available separately.
a- Cast iron pump - Use two 1⁄4-20 x 11⁄2” (S&S 50-0080) and four 1⁄4-20 x 21⁄4“ (S&S 50-0019) hex head cap screws and one 1⁄4”
lock washer (S&S 50-7019) for each screw.
b- Alloy pump - Use two 1⁄4-20 x 11⁄2” (S&S 50-0080) and four 1⁄4-20 x 23⁄4” (S&S 50-0081) hex head cap screws and one 1⁄4” lock
washer (S&S 50-7019) for each screw.
H- Tappet guides - Mounting holes in S&S crankcase are 1⁄4-20 thread. Tighten to 8-10 ft. lbs. Mounting screws are not furnished, but are
available separately.
1- 1936 to 1978 - S&S cases accept most stock tappet guides. Due to casting variations, however, some early cast iron guides may require
minor grinding at corners adjacent to cylinder spigot bore decks. Use four 1⁄4-20 x 7⁄8” (S&S 50-0068) 12 pt. cap screws and four 1⁄4“ (S&S
33-5308) screw adapter washers for each guide. See Line Drawing, item 13.
2- 1979 to present - Use four 1⁄4 -20 x 7⁄8” (S&S 50-0068) 12 pt. cap screws for each guide. See Line Drawing Item 13.
CAUTION
CAUTION