S&S Cycle Standard & Easy Start Gear Drive Camshafts for 2007–up Harley-Davidson Big Twin and 2006 Dyna Models User Manual
Page 2
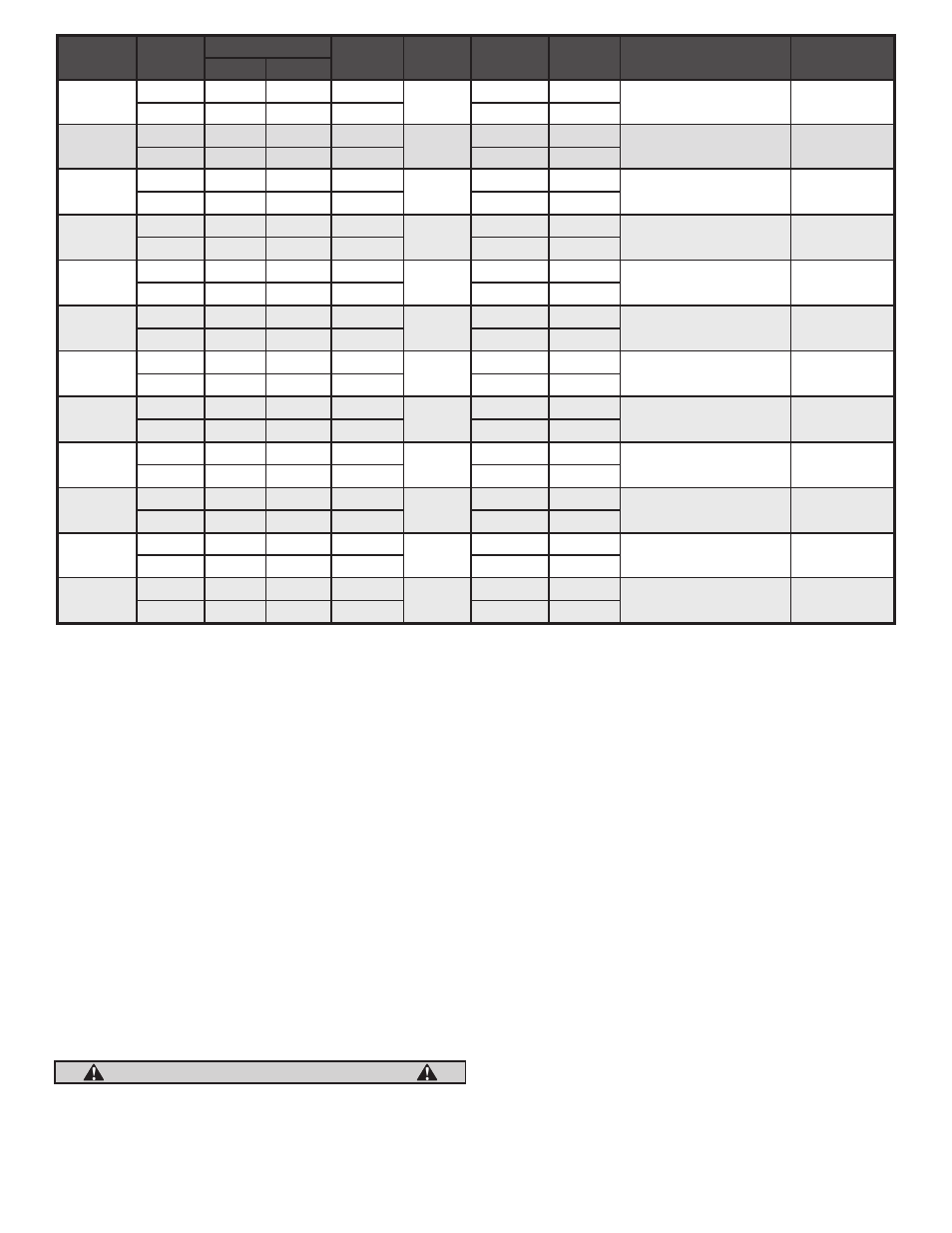
Piston to valve clearance will need to be confirmed when using a cam
with over 0.585" of lift. Clearance should be at least 0.060" intake and
.080" exhaust.
Valve to valve clearance will need to be confirmed when using a cam over
0.585" lift. Clearance should be a minimum of 0.060".
COMPATIBILITY NOTES:
S&S Cam Gear Drive is not compatible with camshafts designed for the
stock style chain cam drive. S&S Cam Gear Drive must be used with S&S
gear drive style camshafts.
2006-Up gear driven camshafts kits 510G, 551G, 570G, 583G and 585G
are compatible with stock 2006-Up valve springs. Due to the change
in lift from the cams, 570G and 585G require adjustable pushrods. S&S
adjustable pushrod kit 93-5095 is recommended for engines with stock
length cylinders. Longer pushrods are available for engines with longer
than stock cylinders. See the S&S Catalog for pushrods.
S&S camshaft installation Kit 106-6068 is strongly recommended when
installing S&S cam gear drive. This kit includes hardware, gaskets and
bearings required for cam installation, this kit includes oil pump o-rings.
OVERVIEW OF EASY START CAMSHAFTS (IF EQUIPPED):
S&S® has developed Easy Start cams to assist starting with a
compression release cam. The operation is simple: at cranking speeds
a spring loaded decompression lever holds the exhaust valve open
slightly. Once the engine fires and exceeds 750 RPM, centrifugal force
sends the lever to a retracted position, allowing the engine to run
normally.
INTRODUCTION
The S&S® cam gear drive offers many advantages over the original cam
drive system:
• Reduced maintenance. There are no chain guides or shoes to wear or
replace and no debris from wearing guides or shoe in you engine.
• Consistent cam timing. Cam gears are keyed with a light press fit.
• Eliminating the chains and tensioners eliminates excessive side
loading of the cam support plate bearing surface.
• Critical sprocket alignment is unnecessary.
• Maintained accurate valve timing when using high performance
valve springs with higher spring forces.
• Higher cam lifts can be used without decreasing cam base circle. Gear
driven cams rotate in opposite direction from the chain driven cams.
Lobes on the front and rear cams never point towards each other,
allowing increased lobe height.
NOTES:
2004-up stock valve springs will handle camshafts with lift up to 0.585".
If a camshaft with higher lift is installed, high performance valve springs
capable of handling a greater lift must be used.
A cam with over 0.585" of lift will cause interference between the valve
spring top collar and the valve seal with stock cylinder heads.
Cams with more than .585" lift require that the stock valve
springs be replaced with high lift spring kits. Some high lift
spring kits require clearance checks and many require cylinder
head modifications to prevent contact between top color and
valve seal, and to achieve correct installed height. See the
instructions with your spring kit for exact specifications.
2
Chart 1
Cam Name
Lobe
Timing
Duration
Lift
Centerline
TDC Valve
Lift
05-UP Models works with
stock valve springs
works with
stock pushrods
Open
Close
510G
Int
20°
38°
238°
0.510"
99°
0.187"
X
X
Exh
52°
20°
252°
106°
0.179"
551 (E)
Int
17°
19°
216°
0.550"
91°
0.178"
X
X
Exh
41°
17°
238°
102°
0.170"
557
Int
6°
27°
212°
0.557"
100°
0.113"
X
X
Exh
39°
12°
231°
103°
0.146"
570 (E)
Int
20°
40°
240°
0.570"
100°
0.187"
X
X
Exh
55°
20°
255°
107.5°
0.179"
583 (E)
Int
5°
18°
203°
0.583"
96.5°
0.113"
X
X
Exh
58°
24°
262°
107°
0.206"
585 (E)
Int
20°
45°
245°
0.585"
102.5°
0.186"
X
X
Exh
60°
20°
260°
110°
0.179"
625 (E)
Int
20°
55°
255°
0.625"
107.5°
0.189"
Exh
60°
20°
260°
110°
0.184"
635
Int
19.5°
43.5°
243°
0.635"
102°
0.186"
Exh
58.5°
37.5°
276°
100.5°
0.284"
640 (E)
Int
25°
60°
265°
0.640"
107.5°
0.228"
Exh
65°
25°
270°
110°
0.214"
675 (E)
Int
25°
60°
269°
0.675"
109.5°
0.235''
Exh
74°
25°
275°
112.5°
0.205"
HP103
Int
20°
49°
249°
0.575"
102.7°
0.199"
X
X
Exh
45°
26°
251°
101.5°
0.206"
MR103
Int
13°
33°
226°
0.585"
100°
0.097"
X
X
Exh
50°
22°
252°
104°
0.191"
CAUTION