C-4 finisher trowel — maintenance – Multiquip C42H User Manual
Page 28
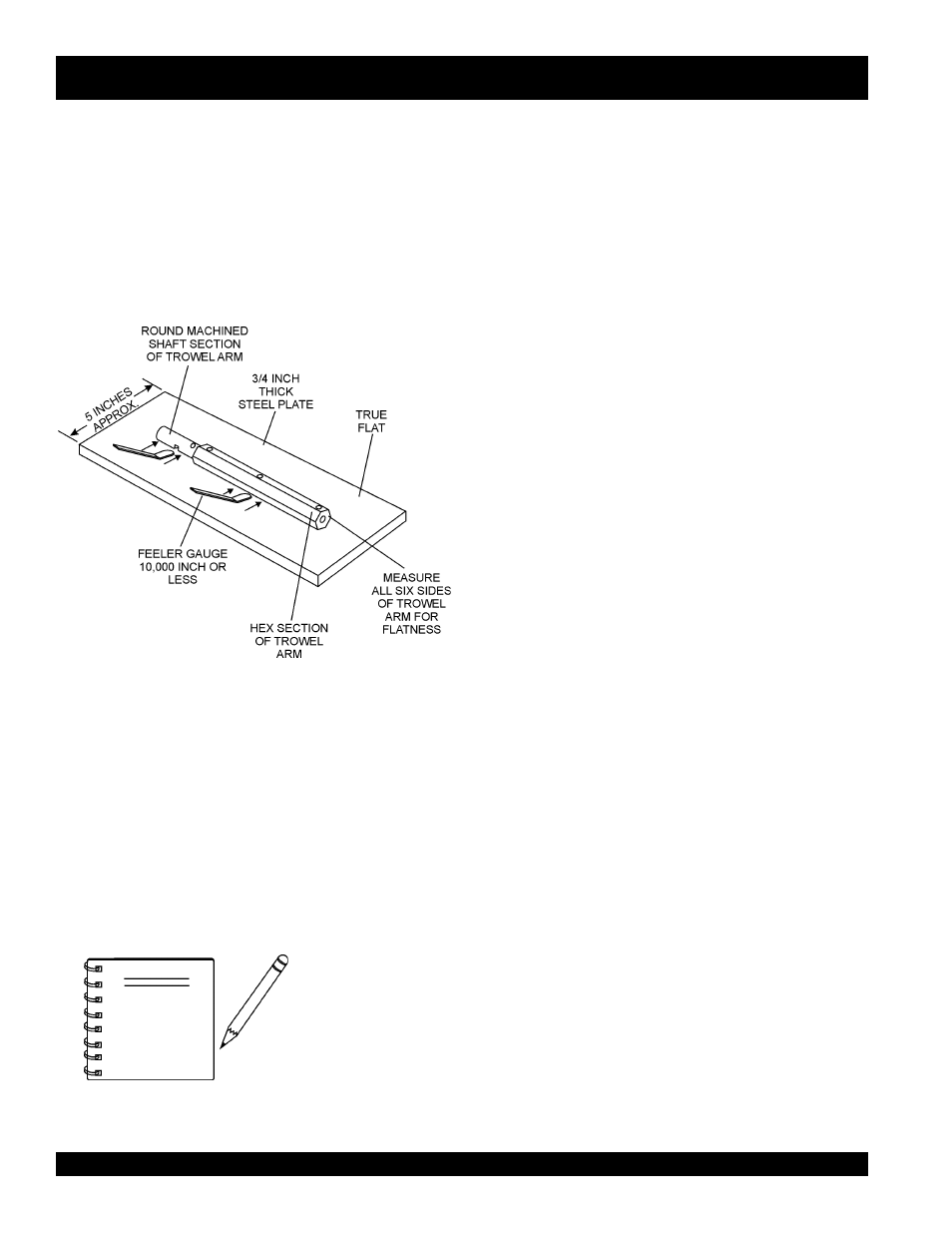
PAGE 28 — C-4 FINISHER WALK-BEHIND TROWEL— PARTS & OPERATION MANUAL — REV. #0 (07/24/02)
Trowel Arm Flatness Test
1. Using a piece of 3/4 inch thick steel plate or any surface which
is
true
and
flat
, check all
six sides
of each trowel arm for
flatness.
2. Check each of the six sides of the trowel arm (hex section
only) using a ten thousands of an inch (max.) feeler gauge
(Figure 28) between the flat of the trowel arm and an
ex
-
tremely flat
test surface.
3. If the trowel arm is found to be
uneven
or
bent
, replace the
trowel arm. A bent trowel will not allow the trowel to operate
in a smooth fluid rotation.
4. Next, check each of the six sides of the round machined shaft
section of the trowel arm. Each section should have the
same
clearance
between the round of the trowel arm shaft and the
test surface.
Figure 28. Trowel Arm Flatness Test
C-4 FINISHER TROWEL — MAINTENANCE
Trowel arms can be
damaged by rough
handling or by striking
exposed plumbing or
forms while in operation.
ALWAYS look-out for
objects which might
cause damage to the
trowel arms.
Re-Assembly
1. Clean and examine the
lower wear plate
,
thrust collar
and
thrust collar bushing
. Examine the entire spider assembly.
Wire brush any concrete or rust build-up. If any of the spider
components are found to be damaged or out of round,
replace them.
2. Insert all trowel arms (4) into spider plate.
3. Lock trowel arms in place by tightening the hex head zerk
grease fittings (4) and allen head screws (2).
4. Re-install the blades back onto the trowel arms.
5. Reinstall lower wear plate,
thrust collar
and
thrust collar
bearing
in the
reverse order
that they were dis-assembled
onto the spider shaft. Make sure that there is little or no lateral
movement between the thrust collar and the spider shaft.
6. Carefully lift
the upper trowel assembly
, line up the key-
way on gear box main shaft and insert into spider assembly.
7. Lubricate all grease points (zerk fittings) with premium
"
Lithum 12"
based grease, conforming to NLG1 Grade #2
consistency.
NOTE