Determine the gripping pressure, Determine the gripping pressure 52, Force versus temperature – MTS Series 646 Hydraulic Collet Grips User Manual
Page 52: Force versus hydraulic pressure
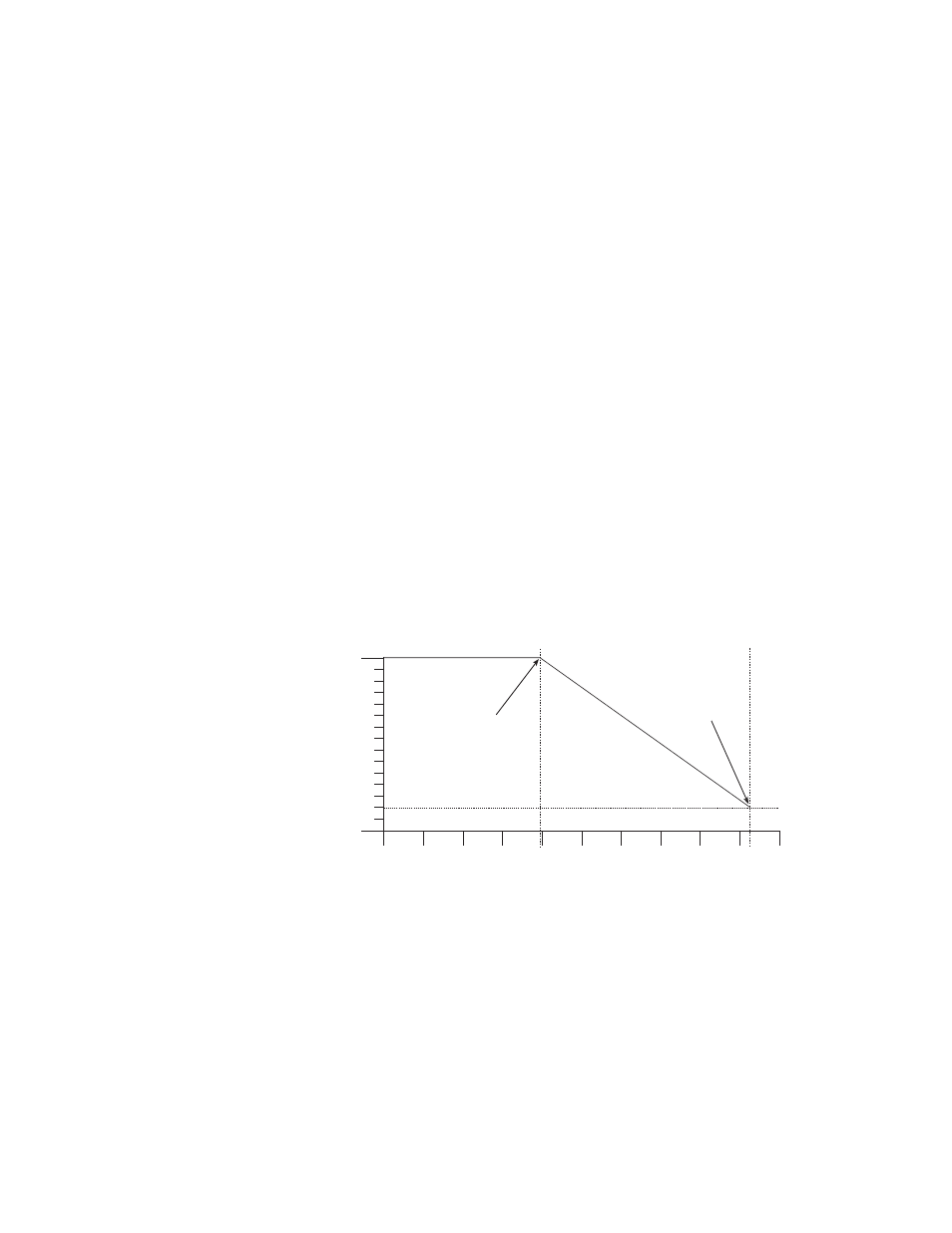
Series 646 Hydraulic Collet Grips
52
Operation
Determine the Gripping Pressure
The amount of hydraulic pressure to be applied to the grips must be sufficient to
prevent backlash between the specimen ends and the specimen adapters, and also
between the mating threads of the specimen adapters and the grip extensions,
during all parts of the loading cycle.
To also ensure that the grips will not be loaded beyond their force rating,
however, determining hydraulic pressure must start with temperature
considerations, rather than the forces to be applied to the specimen.
Note
If the gripped ends of the specimen become deformed, reduce the
hydraulic gripping pressure. Re-compute the amount of pressure
required to grip the specimen.
Determining the required hydraulic pressure is a two step process:
1. Determine that the maximum force (whether tensile or compressive) to be
applied to the specimen is within the grip rating, considering the
temperatures that the specimen will experience.
2. If anticipated forces are appropriate, use the “Required Pressure for the
Applied Force” graph to find the required gripping pressure.
Force versus
temperature
The following figure shows that the grip force rating for specimen temperatures
up to 700°C is 67 kN (1292°F at 15,000 lb) is stable. The figure also shows that
the force rating is reduced proportionately for specimen temperatures between
700°C and 1000°C (1292°F and 1832°F), with a maximum force rating of 8.9 kN
at 1000°C (2000 lb at 1832°F).
Grip Force Rating versus Specimen Temperature
Force versus hydraulic
pressure
The horizontal scale at the bottom of the graph shows required gripping pressure
versus maximum force to be applied, which is shown on the left hand vertical
scale.
The right hand vertical scale is provided as a convenience. Assuming that the
gage portion of the specimen has a diameter of 0.25 inches, the right hand scale
shows maximum engineering stress (for a 0.25 inch diameter specimen), versus
required gripping pressure on the bottom horizontal scale and also the equivalent
force on the left hand vertical scale.
Specimen Temperature
66.7 kN up to 700º C
(15 kip up to 1292º F)
8.9 kN at 1000º C
(2 kip at 1832º F)
1038º C
(1900º F)
482º C
(900º F)
0 kN
(0 kip)
66.7 kN
(15 kip)
Load