Marshalltown FCS86 SURFACE SHARK Floor Stripper User Manual
Page 29
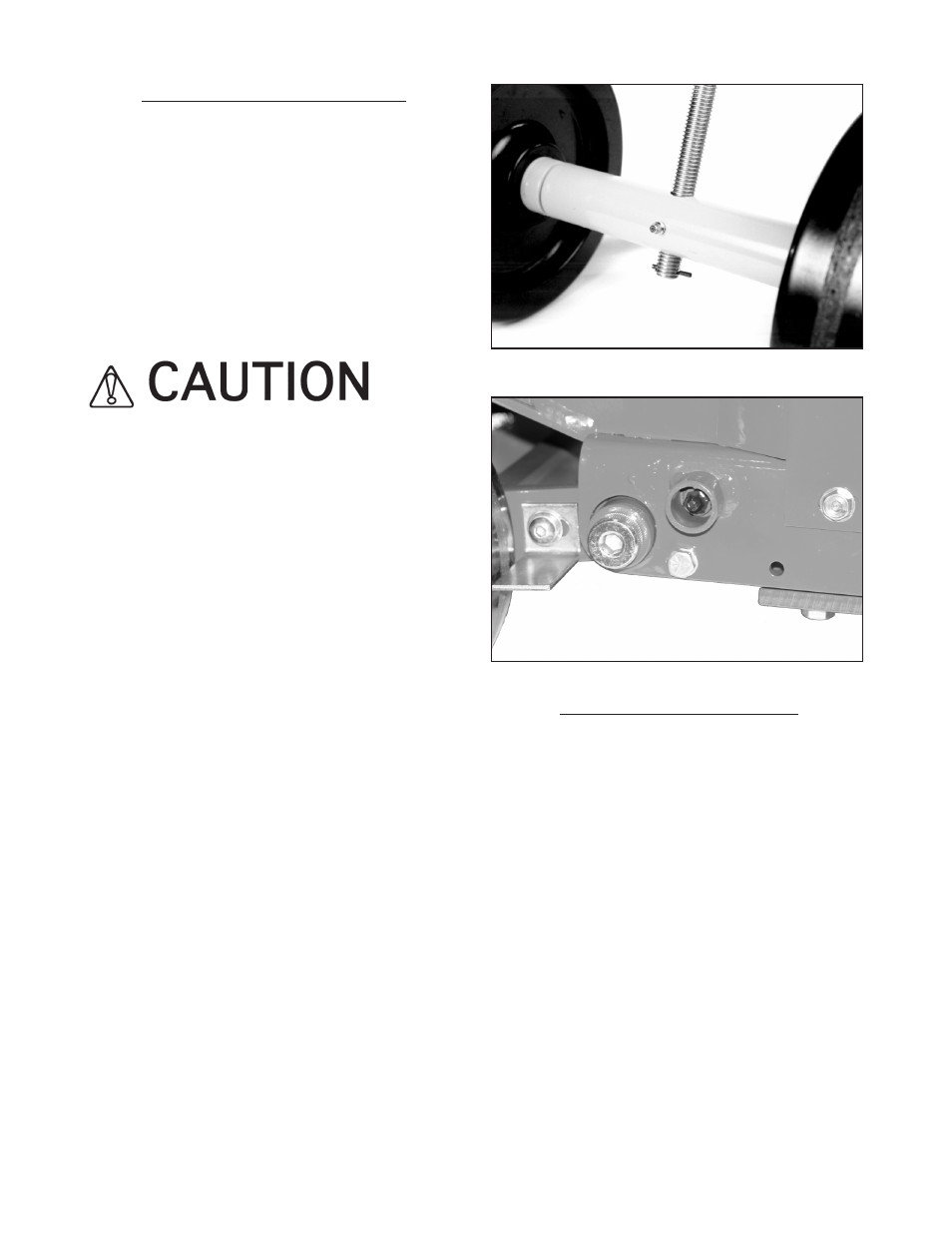
FCS86 SuRFACE ShARK™ FLooR STRIPPER
PAgE 29
LUBRICATION REQUIREMENTS
Parts Required:
1 each, standard grease gun filled with one of the
following: ESSo beacon 325, Shell Alvania
#2, Chevron SRI, or equivalent.
1 each, container of dry film lubricant.
1) Lubricate the caster wheel bearings with a dry film
lubricant only. Dry film lubricants dry immediately upon
contact. use sparingly. Excess lubricant will attract
the fine grained, powdered materials described and
directly affect bearing service life.
Do not lubricate the caster wheels with any
lubricant other than a dry film type. Grease
and many other liquid type lubricants will
attract foreign material accumulations that
can reduce bearing service life.
2) Zerk® type grease fittings are provided at two
locations:
a) To lubricate the back Saver™ blade Control System
jackscrew. Keep the jackscrew properly lubricated with
grease to minimize friction when operating the blade
control lever. Excessive lubrication will attract foreign
material accumulations that can reduce jackscrew
service life. FIguRE 29.
b) To lubricate the exciter bearing and bearing housing
casting. The exciter utilizes a shielded type ball bearing.
The Zerk® fitting provides lubrication for both the balls
and self-aligning feature of the bearing unit. FIguRE
30. grease interval will vary depending upon machine
utilization rates and operating environment factors.
grease accumulation on the bearing and housing
would indicate excessive lubrication.
Sleeve type bearings utilized for the operator handle
are self-lubricating and will not normally require
additional lubrication during their normal service life.
ball type bearings are shielded or sealed and will
not normally require additional lubrication during their
normal service life.
FIguRE 29
FIguRE 30
ELECTRIC MOTOR SERVICE
The electric motor is capable of operating for many
years with a reasonably small amount of maintenance.
before attempting to service the motor, disconnect
the Floor Stripper from the power supply. Clean the
motor surfaces periodically, preferably with a vacuum
cleaner. heavy accumulations of dirt and lint will result
in overheating and premature failure of the motor.
The electric motor is equipped with higher capacity
ball bearings and under normal service and ambient
temperatures, should not require relubrication for
many years. If you feel that the motor requires
relubrication, contact the local representative of the
motor manufacturer for specific information.
The seals utilized with the motor are intended to
deliver a longer service life in a dust filled atmosphere.
When replacing the seals, utilize only components
meeting the original factory specifications.