INFICON MPG40x ATM to Ultra-High Vacuum Gauge User Manual
Inverted magnetron pirani gauge, Safety, Technical data
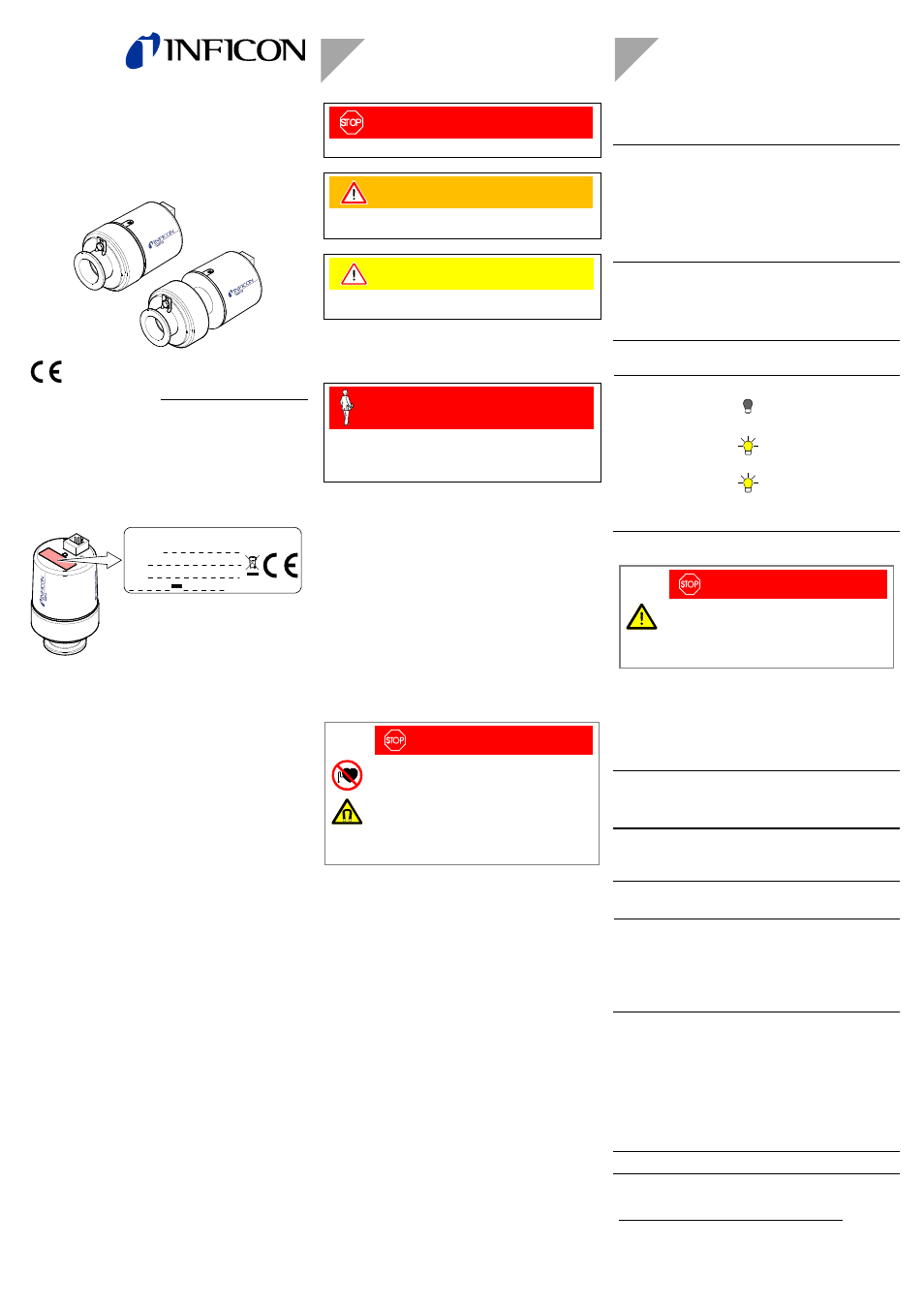
Inverted Magnetron Pirani
Gauge
MPG400
MPG401
Instruction Sheet
Incl. Declaration of Conformity
tima48e1-a (2008-10)
Product Identification
In all communications with INFICON, please specify the in-
formation on the product nameplate. For convenient refer-
ence copy that information into the space provided below.
Model:
PN:
SN:
W
INFICON AG, LI-9496 Balzers
Validity
This document applies to products with the following part
numbers:
MPG400
(FPM sealed)
MPG401
(
all-metal)
351-010
(DN 25 ISO-KF)
351-011
(DN 40 ISO-KF)
351-012
(DN 40 CF-F)
351-020
(DN 25 ISO-KF)
351-021 (
DN 40 ISO-KF)
351-022
(DN 40 CF-F)
The part number (PN) can be taken from the product name-
plate.
If not indicated otherwise in the legends, the illustrations in
this document correspond to the product with part number
351-010. They apply to the other products by analogy.
We reserve the right to make technical changes without prior
notice.
All dimensions in mm.
Intended Use
The Inverted Magnetron Pirani Gauges MPG400 and
MPG401 have been designed for vacuum measurement in
the pressure range of 5×10
-9
… 1000 mbar.
The Inverted Magnetron Pirani Gauges must not be used for
measuring flammable or combustible gases which react in
air.
The gauges can be operated in connection with an INFICON
Single-Channel Controller VGC401, Two-Channel Controller
VGC402 and Three-Channel Controller VGC403, or with
another controller.
Functional Principle
The gauges consist of two separate measurement systems
(Pirani and cold cathode system) the signals of which are
combined in such a way that one measurement signal is
output. The Pirani measurement circuit is always on.
Safety
Symbols Used
DANGER
Information on preventing any kind of physical injury.
WARNING
Information on preventing extensive equipment and envi-
ronmental damage.
Caution
Information on correct handling or use. Disregard can lead
to malfunctions or minor equipment damage.
Personnel Qualifications
Skilled personnel
All work described in this document may only be carried
out by persons who have suitable technical training and the
necessary experience or who have been instructed by the
end-user of the product.
General Safety Instructions
• Adhere to the applicable regulations and take the nec-
essary precautions for the process media used.
Consider possible reactions between the materials and
the process media.
Consider possible reactions (e.g. explosion) of the
process media due to the heat generated by the product.
• Adhere to the applicable regulations and take the neces-
sary precautions for all work you are going to do and con-
sider the safety instructions in this document.
• Before beginning to work, find out whether any vacuum
components are contaminated. Adhere to the relevant re-
gulations and take the necessary precautions when hand-
ling contaminated parts.
DANGER
DANGER: magnetic fields
Strong magnetic fields can disturb electronic
devices like heart pacemakers or impair their
function.
Maintain a safety distance of =10 cm between
the magnet and the heart pacemaker or prevent
the influence of strong magnetic fields by anti-
magnetic shielding.
Communicate the safety instructions to all other users.
Liability and Warranty
INFICON assumes no liability and the warranty becomes null
and void if the end-user or third parties
• disregard the information in this document
• use the product in a non-conforming manner
• make any kind of interventions (modifications, alterations
etc.) on the product
• use the product with accessories not listed in the product
documentation.
The end-user assumes the responsibility in conjunction with
the process media used.
Gauge failures due to contamination, as well as expendable
parts (filament), are not covered by the warranty.
Technical Data
Measurement range (air, N
2
) 5×10
-9
… 1000 mbar
Accuracy (N
2
)
≈
±30% (in the range
1×10
-8
… 100 mbar)
Repeatability
≈
±5% (in the range
1×10
-8
… 100 mbar)
Output signal (measuring
signal)
Voltage
range
Measurement range
0 … +10.5 V
1.82 … 8.6 V
Voltage vs. pressure
logarithmic , 0.6 V/decade
Error signal
<0.5 V no supply
>9.5 V Pirani sensor defec-
tive (filament rupture)
Output impedance
2×10
Ω
Minimum loaded impedance
10 k
Ω
, short-circuit proof
Response time
p > 10
-6
mbar
(pressure dependent)
<10 ms
p = 10
-8
mbar
≈
1000 ms
Identification gauge
85 k
Ω, referenced to supply
common
Status pin
6
p > 10
-2
mbar
Pirani-only mode
Low = 0 V
p < 10
-2
mbar
Cold cathode not
ignited
Pirani-only mode
Low = 0 V
p < 10
-2
mbar
Cold cathode ignited
Combined Pirani /
cold cathode mode
High = 15 … 30 VDC
LED
High voltage on (LED on)
Supply
DANGER
The gauge may only be connected to power
supplies, instruments or control devices that con-
form to the requirements of a grounded extra-
low voltage (SELV-E according to EN 61010).
The connection to the gauge has to be fused
1)
.
Voltage at the gauge
15 … 30 VDC
(ripple
≤
1 V
pp
)
Power consumption
≤
2 W
Fuse
1)
≤
1 AT
Voltage at the supply unit with
maximum cable length
16 … 30 VDC
(ripple
≤
1 V
pp
)
2)
Adjustment
Potentiometer
Potentiometer
adjustment under 10
-4
mbar
adjustment at atmospheric
pressure
Electrical connection
FCC68 socket, 8 poles
Sensor cable
8 poles, shielded
Line length
≤
50 m (8
×
0.14 mm²)
Operating voltage
≤
3.3 kV
Operating current
≤
500 µA
Grounding concept
→ "Electrical Connection"
Vacuum connection –
measuring common
connected via 10 k
Ω (max.
voltage differential with
respect to safety ±50 V
accuracy ±10 V)
Supply common – signal
common
conducted separately
Materials exposed to vacuum
Vacuum connection
Measurement chamber
Feedthrough isolation
Internal seal
MPG400
MPG401
Anode
Ignition aid
Pirani measurement tube
Pirani filament
stainless steel
stainless steel
ceramic
FPM 75
Ag, Cu, soft solder (Sn, Ag)
Mo
stainless steel
Ni, Au
W
Mounting orientation
any
1)
INFICON controllers fulfill these requirements.
2)
The minimum voltage of the power supply unit must be in-
creased proportionally to the length of the sensor cable.