Flint & Walling Constant Pressure Pumping Stations - Add-On Kit User Manual
Page 4
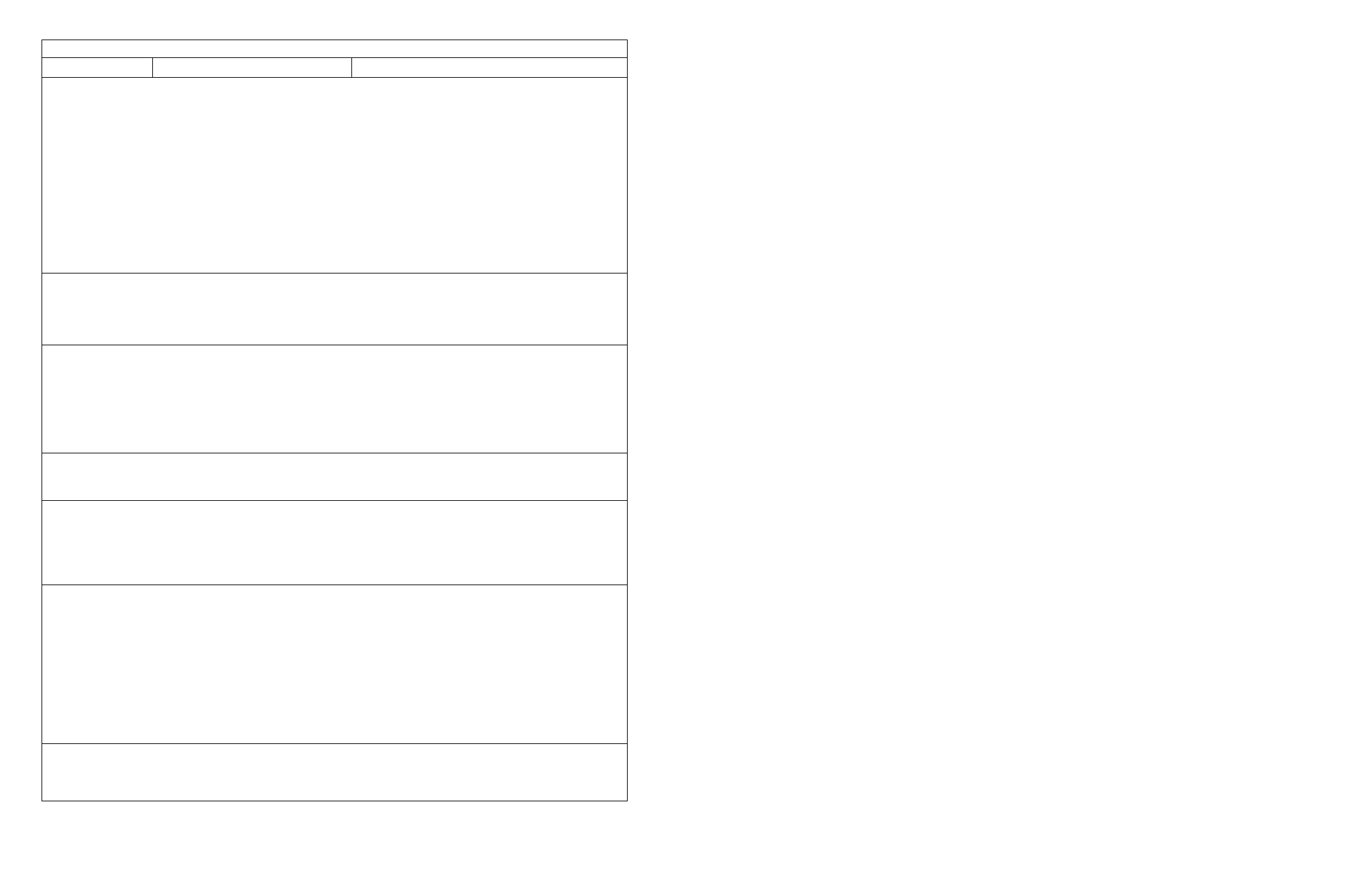
6
(FW1442)
95 North Oak St. • Kendallville, IN 46755 • 1-800-742-5044
7
(FW1442)
95 North Oak St. • Kendallville, IN 46755 • 1-800-742-5044
COntInGenCy OPtIOnS
For some applications, a contingency plan is needed
if the system is unable to deliver the required water
in the event of a component failure which causes one
pump to fail. The contingency plans below will allow
the working pump to deliver water until the failed
component is repaired/replaced, even if the single
pump cannot meet the pressure demands required by
the application.
1. Problem: Single phase pump or starter failure.
Effect: Single phase pump does not run when
demand is reached. Drive continues to run 3-phase
pump, but system drops below set pressure when
demand is high. User Contingency action: None.
Long term user action: Repair/replace failed single
phase component.
2. Problem: Three Phase pump failure (drive not
tripped on fault). Effect: Three phase pump does
not run. Single phase motor is controlled by the
drive and runs 1 minute on, 1 minute off on low
water demand or continuously with higher demand.
User Contingency action: None. Long term user
action: Repair/replace failed 3-phase pump.
3. Problem: Drive fails. Effect: Neither pump runs.
User Contingency action: With power turned off to
both drive and single phase motor, remove control
wires from drive terminals T5 & T6 and wire nut
together. Hook up a hose to hose bib and route
back to supply tank or drain and open hose bib
valve. (This is done to guarantee a minimum flow of
water thought the pump when there is no demand
for water and prevent damage to the pump that
can occur when the pump is run deadhead.) Turn
power on to single phase pump – Note: Pump will
run continuously. Long term user action: Replace
drive.
4. Problem: Transducer Fails (Drive Trips tr cL1). Effect:
Neither pump runs. User Contingency action: With
power turned off to both drive and single phase
motor, remove control wires from drive terminals T5
& T6 and wire nut together. Hook up a hose to hose
bib and rout back to supply tank or drain and open
hose bib valve. (This is done to guarantee a mini-
mum flow of water thought the pump when there
is no demand for water and prevent damage to the
pump that can occur when the pump is run dead-
head.) Turn power on to single phase pump – Note:
Pump will run continuously. Long term user action:
Replace transducer.
Troubleshooting Chart
Symptom
Possible Cause(s)
Corrective Action
Low or no discharge
1. Incorrect rotation
1. Refer to wiring diagram
2. Insufficient inlet pressure or
suction head (NPSH Required)
2. Increase inlet pressure by adding more fluid to
fluid source. (See Spec’s for minimum NPSH
Required)
3. Total head too high
3. Lower discharge head
4. Leak in suction line
4. Repair or replace
5. Impeller clogged or damaged
5. Clean or replace
6. Wrong size piping
6. Make needed adjustments
7. Casing gasket leaking
7. Replace gasket
8. Suction or discharge line valves
closed
8. Open
9. Mechanical seal leaking
9. Replace
Loss of suction
1. Insufficient inlet ressure or suction
head (NPSH Required)
1. Increase inlet pressure by adding more fluid to
fluid source. (See Spec’s for minimum NPSH
Required)
2. Clogged strainer
2. Clean or replace
Pump vibrates and/
or makes excessive
noise
1. Mounting plate or foundation not
rigid enough
1. Reinforce
2. Foreign material in pump
2. Clean
3. Damaged impeller
3. Replace
4. Cavitation present
4. Check suction line for proper size and be sure
valve is open. Remove excessive loops in suction
line. (See Spec’s for minimum NPSH Required)
Pump leaks at shaft
1. Damaged or worn mechanical seal
1. Replace
2. Corrosion due to character of
liquid pumped
2. Discontinue pumping liquid and consult factory
Pump will not start
or run
1. Improperly wired
1. Refer to wiring diagram
2. Blown fuse or open circuit breaker
2. Replace fuse or close circuit breaker
3. Loose or broken wiring
3. Tighten connections and replace broken wiring
4. Impeller clogged
4. Clean
5. Motor shorted out
5. Replace
Motor problems
1. Various
1. Consult qualified electrician
2. Overloading motor. Too much
water delivery
2. Restrict outlet by closing down valve in discharge
line
3. Liquid heavier and more viscous
than water
3. Consult factory
4. Seal binding
4. Replace
5. Rotor binding
5. Repair or replace
6. Voltage and frequency lower than
rating
6. Reconnect to rated voltage and frequency
7. Defects in motor
7. Repair or replace
Pinholes in the
casting. Liquid
dripsp around seal
area but is not seal
1. Cavitation caused by insufficient
inlet pressure or suction head
(NPSH Required)
1. Increase inlet pressure by adding a higher level of
fluid to source or increasing inlet pressure. (See
Spec’s for minimum NPSH Required)