Validation testing, Hepa filter burn-off process not necessary, Hepa filter unit replacement – Despatch Stackable LCC/LCD-4 User Manual
Page 19: Hepa filter: magnehelic pressure gauge
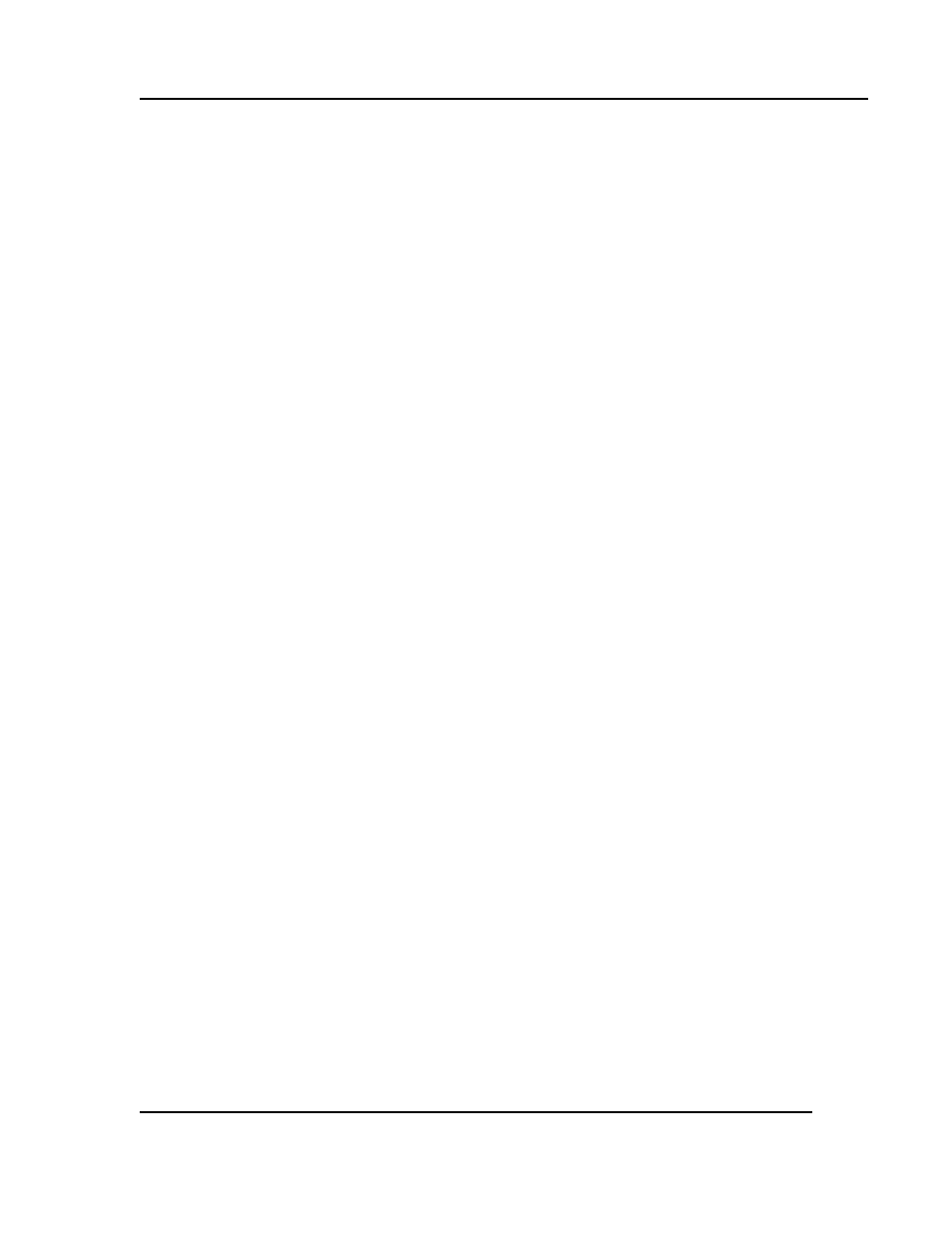
Stackable LCC/LCD Oven
Owner’s Manual
T
HEORY OF
O
PERATION
Version 1.1
19
Copyright © 2012 by Despatch Industries.
All rights reserved. No part of the contents of this manual may be reproduced, copied or transmitted in any form or by any
means including graphic, electronic, or mechanical methods or photocopying, recording, or information storage and
retrieval systems without the written permission of Despatch Industries, unless for purchaser's personal use.
Class 100 testing may be performed before or after a proper filter burn-in procedure has been
performed. Despatch guarantees Class 100 condition measurements based on two methods of test.
The direct method employs an extraction-type particulate analyzer. The indirect method involves
particle settling over a specified period of time onto a clean disk.
3.3.2.3. Validation Testing
Despatch recommends the following test sequence for pharmaceutical Class 100 ovens.
1.
Proper installation of the HEPA filters (Section 0).
2.
Ambient air challenge to determine integrity of oven chamber and filter gaskets.
3.
Proper filter burn-off procedure.
4.
Class 100 testing inside the work chamber.
3.3.2.4. HEPA Filter Burn-off Process Not Necessary
HEPA filters contain a binder material which protects the filter media during production and
shipping. Smoke produced from burning this binder at elevated temperatures is undesirable
during normal oven operation. Burning off the binder will ensure a clean process at elevated
temperatures.
However, when the binder is burned out of the filter media, the filter becomes very
fragile: too fragile to withstand normal shipping and handling. For this reason, Despatch does not
perform the burn-off procedure. The burn-off process is not necessary at temperatures under
200°C.
3.3.3. HEPA Filter Unit Replacement
Periodic replacement the HEPA filter unit due to:
Resistance, or pressure drop, across the filter unit. Maximum level of resistance in inches
(water gauge) will vary depending upon the operation of the filter and the available fan
capacity. Adequate fan capacity must be available.
Loss of efficiency (leakage), determined from air-sampling measurements made downstream
of the filter unit.
Visible damage or rupture of the filter media in a unit.
Change in process application.
Excessive build-up of lint or combustible particulate matter on the filter unit.
Water droplets in airstream through filter, free water (RH = 100%), will saturate filter very
quickly and may cause burnout or holes in burned off filter media.
High level of radiation in the vicinity of the filter unit.
3.3.4. HEPA Filter: Magnehelic Pressure Gauge
The LCC Series oven is equipped with a Magnehelic pressure gauge which measures the pressure
in front of the HEPA filter (Figure 4). As the filter becomes dirty, pressure increases. Despatch