Installation, Instructions, Caution – Autoquip FREIGHTLIFT FLT User Manual
Page 35
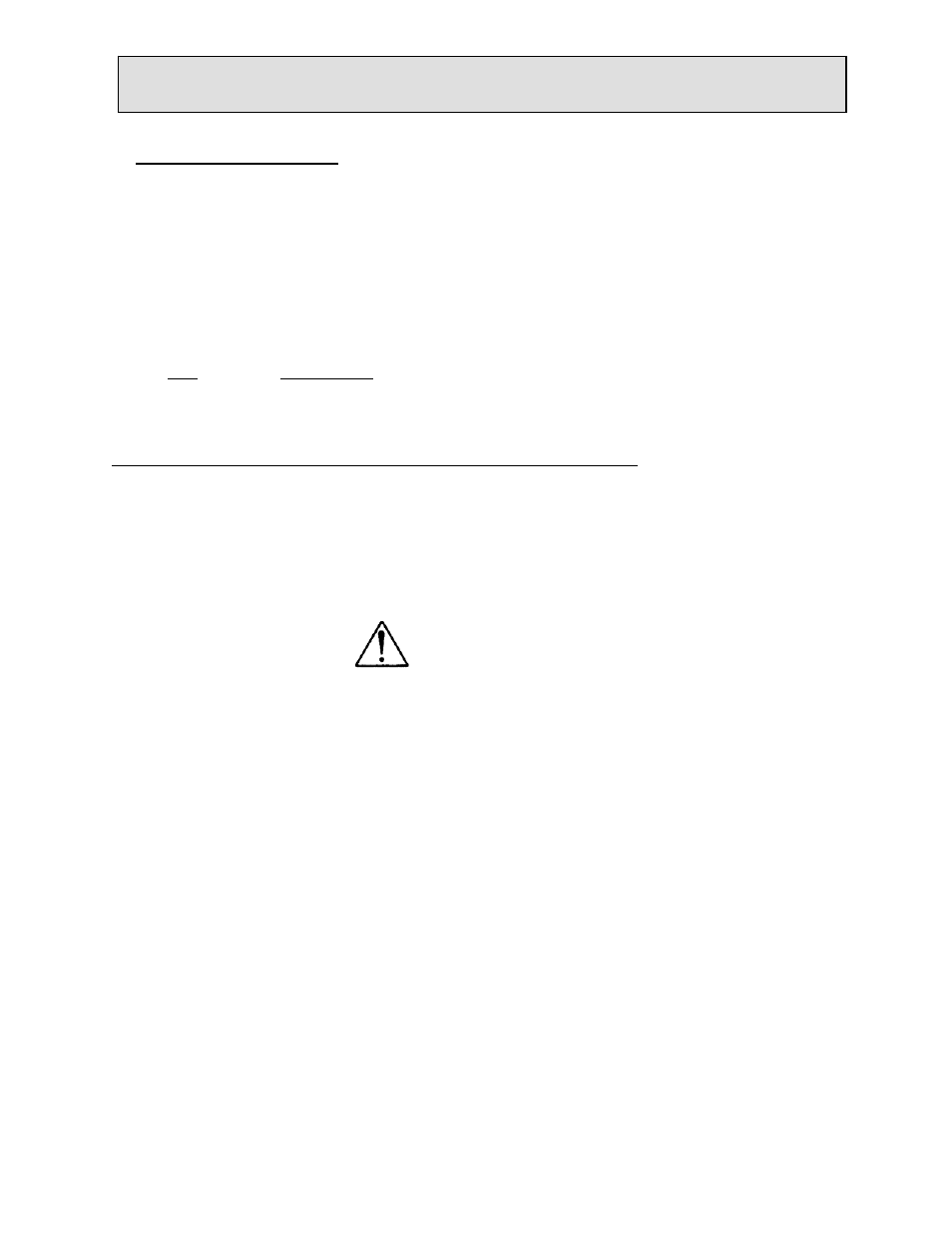
35
INSTALLATION
INSTRUCTIONS
C. BRACING THE BEAMS
All illustrations on the GA drawing for bracing preferences are for reference only. Site
conditions may require different anchoring and bracing. The installers are ultimately
responsible for the proper and safe anchoring and bracing of the equipment. Autoquip
Corporation supplies material for bracing on standard applications, but special bracing
may be required by the installer on non-standard models. The special materials for
anchoring and bracing of the lift and gates are not the responsibility of Autoquip.
NOTE: For all field welding of braces, use 1/4" fillet – all around.
Items needed:
Qty
Description
Varies
Horizontal Channel Braces
varies
Brace Plates – with (4) 9/16” dia. holes each
HORIZONTAL / UPPER LEVEL BRACING (Refer to Figure 17)
1. Attach the horizontal channel brace to the upper floor landings with either lags or by
welding (it has been assumed that you will have a solid floor face to attach to for
your installation). When attaching the floor to beam brace, use bolts which have
been properly sized to withstand the horizontal pull-out force shown on the GA
drawing.
CAUTION!
Never use concrete anchor bolts on a cinderblock or brick wall! The wall will
not withstand the pull force developed by the lift. Use only recommended
anchoring and bracing methods illustrated in this manual. Equipment
damage or personal injury could result.
2. Add side bracing as necessary for your particular installation in order to prevent the
beams from flexing or swaying sideways during operation.
3. Take necessary precautions to minimize beam movement resulting from the
heating & cooling of welds. Re-check and confirm guide angle dimension.