Micropump GL Series Service Instructions User Manual
Page 6
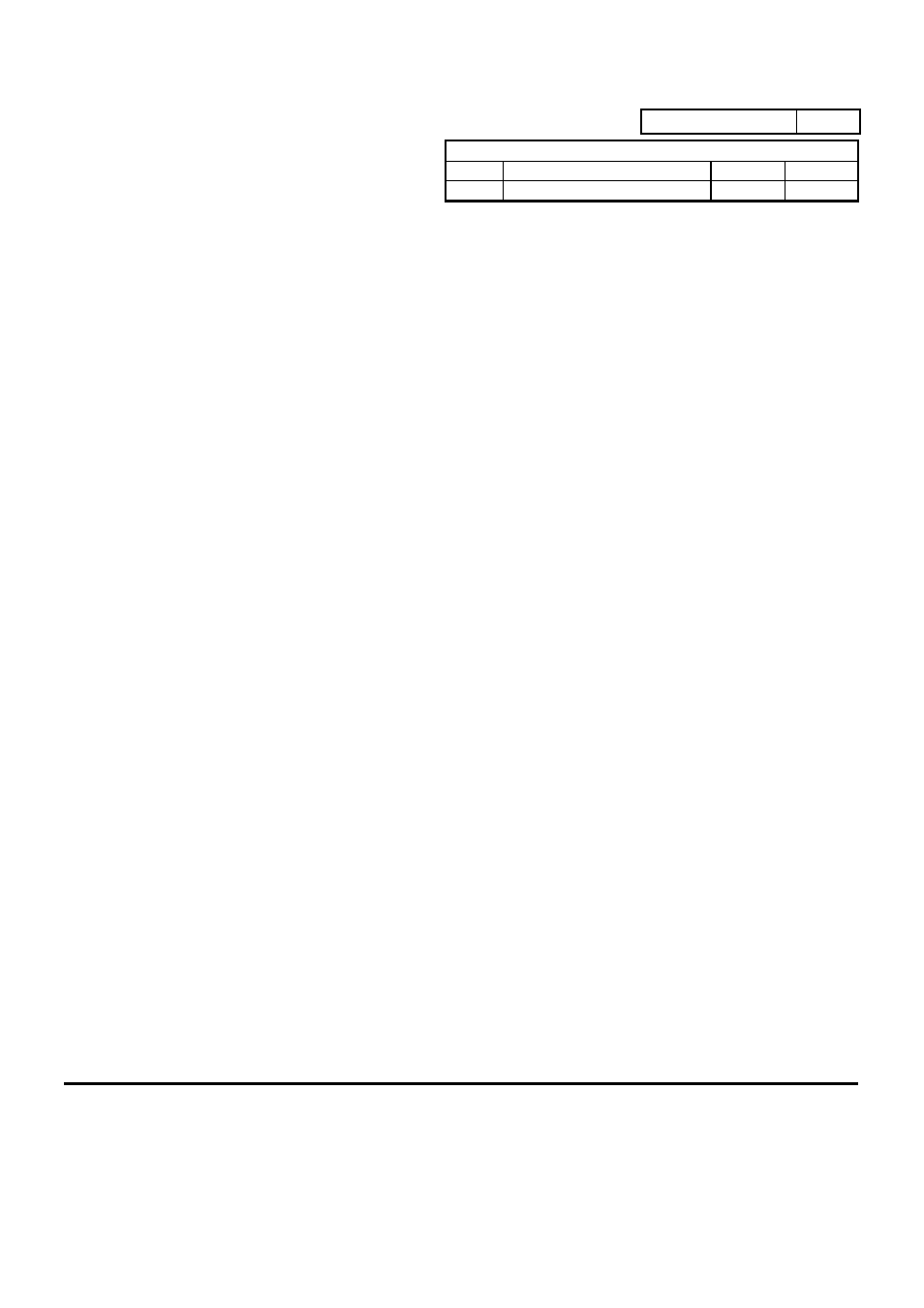
MICROPUMP, INC.
A Unit of IDEX Corporation
PO Box 8975, Vancouver, WA 98668-8975 • Phone: 360/253-2008 • Fax: 360/253-8294
MICROPUMP
LIMITED
A Subsidiary of Micropump, Inc.
Forge Close, Eaton Socon, St.
Neots, Cambridgeshire, PE 19 3TP England, • Phone: (44) (0) 1480-219844 • Fax: (44) (0) 1480-476959
REVISION
LTR.
DESCRIPTION
DATE
BY
C
REVISED PER ECN 4725
11-11-98
LFK
PART NUMBER:
6779
Page 6 of 7
and mesh without sticking. Replace gears if individually gears rotate easily but do not mesh together
without sticking.
7.3 Install 2 Dowel Pins (C) into Pump Body (F).
7.4 If elastomer O-Rings are used, apply a light even film of Dow Corning Vacuum Grease or equivalent.
Apply vacuum grease from capsule to thumb and index finger of one hand, and transfer a light, even
film of vacuum grease to O-Ring (E) by rubbing O-Ring between thumb and index finger. Check that
ENTIRE surface of O-Ring (E) is coated with vacuum grease.
7.5 Install 1 O-Ring (E) into O-ring groove on each side of cavity plate (M). Teflon O-rings may need to be
slightly stretched in order to fit into O-ring grooves.
7.6 Install Cavity Plate (M) over gears onto Dowel Pins (C). Locate Cavity Plate (M) flush onto Pump Body
(F) sealing surface.
7.7 Install Bearing Plate (B) onto gear shafts and dowel pins. Check that Bearing Plate (B) sealing surface
is flush against Cavity Plate (M) sealing surface.
7.8 Install 10 (3 for low pressure version) Screws (A) through Bearing Plate (B) into Pump Body (F) and
tighten to 28 to 30 in.-lbs. (3,2 to 3,4 N-m). It is advised to apply a light oil to screw threads and under
screw head before installation.
Note: Pump with Teflon O-rings may require screws (A) to be tightened 2 to 3 times, due to the
hardness of the Teflon O-rings.
7.9 Install Teflon O-ring (N) into Pump Body (F), o-ring will require a slight compression to fit into groove.
7.9.1 If elastomer O-ring is used, apply light even film of Dow Corning Vacuum Grease or equivalent.
Apply vacuum grease from capsule to thumb and index finger of one hand, and transfer a light,
even film of vacuum grease to O-Ring (N) by rubbing O-ring between thumb and index finger.
Check that entire surface of O-Ring (N) is coated with vacuum grease.
7.10 Driven Magnet (G) installation.
7.10.1 Position Driven Magnet (G) on Driving Gear (L) shaft locating set screw onto flat on Driving
Gear (L) shaft. Magnet Assembly should be located .150" (3.8mm) away from Pump Body (F).
(See Figure 2) Tighten set screw to 13 to 15 in.-lbs. (1,5 to 1,7 N-m) when properly adjusted.
7.11 Check that Driven Magnet (G) is free of metal particles; see Cleaning Instructions, section 5.2.2.
Check that Driving Gear (L) shaft rotates without sticking; see Repair Instructions, section 6.5.5.
7.12 Install Magnet Cup (O) over Driven Magnet (G), onto O-Ring (N) in Pump Body (F); place
Backing Ring (H)(low pressure versions only) over Magnet Cup (O) with the chamfer facing Pump
Body (F).