Description, Split-shaft pto gearbox – Hale RGA User Manual
Page 4
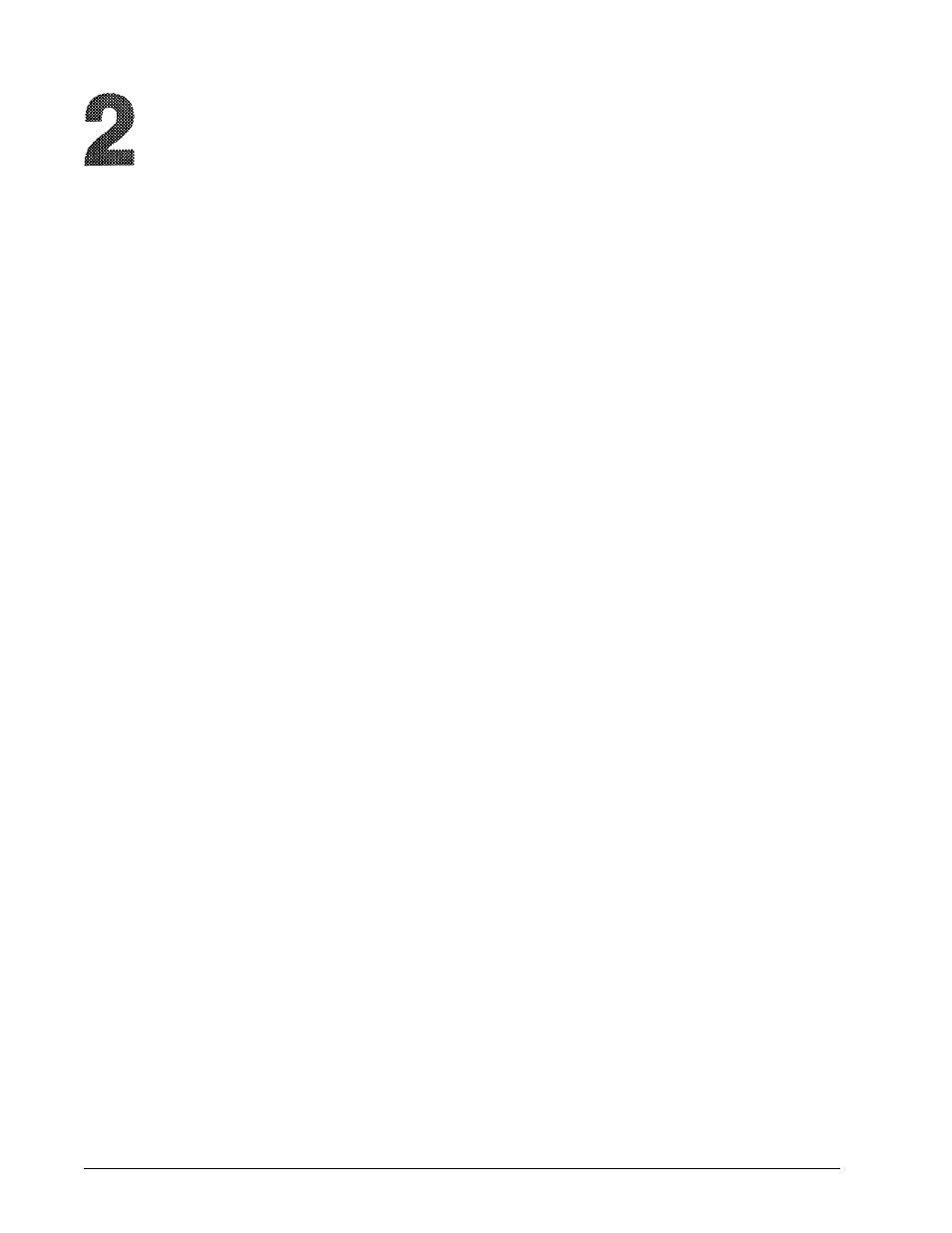
SPLIT-SHAFT PTO GEARBOX
INSTALLATION MANUAL
2
DESCRIPTION
Hale MGA and RGA Series Split-Shaft PTO
gearboxes provide a cost effective means
for driving a pump, generator, air
compressor, winch or other auxiliary
equipment from the truck engine without
resorting to high cost, heavy, dedicated
engines.
The gearboxes are heavy duty drive units
capable of withstanding drive line input
torque during road use of up to 16,000 lb-ft
(21,693 N-m).
The gearboxes are installed in a midship
position on the truck between two sections
of a split drive shaft. (See figure 1)
Mounting holes on the gearboxes permit
attaching the gearbox directly to the truck
frame or through the use of brackets
manufactured by the gearbox installer. The
main drive shaft sections connect to the
gearboxes by drive flanges piloted and
predrilled for compatibility with 1600, 1700
and 1800 series Spicer drive flanges.
Each gearbox model (the MGA and RGA)
can be ordered with the rear drive flange
blanked off for operation with a transmission
mounted PTO. When the PTO drive option is
used the gearbox is not mounted in the
apparatus drive line. (Refer to figure 1)
When shifted from road to auxiliary output
operation the RGA gearbox transmits up to
2300 lb-ft (3188 N-m) torque from the
apparatus drive shaft to the 2 inch by 10
spline rear facing auxiliary drive shaft to
drive the auxiliary equipment.
The MGA gearbox transmits up to 1200 lb-ft
(1627 N-m) torque from the apparatus drive
shaft to the auxiliary drive shaft. The
auxiliary drive shaft on the MGA gearbox
has a 1-½ inch by 10 spline on one end and
a 1-
3
/
8
inch by 10 spline on the other and
can drive two pieces of auxiliary equipment
simultaneously. The MGA gearbox can be
configured with the auxiliary drive shaft
positioned with either spline facing in either
the front or rear position. Additionally the
MGA gearbox can be mounted in either a
vertical or horizontal position.
Chrome nickel steel spur gears provide the
necessary rotational energy transmission.
The auxiliary drive shaft of each gearbox is
rigidly supported by two ball bearings with
double lip oil seals to prevent gearbox
contamination.
CAUTION: The gearbox IS NOT a “hot
shift” device. Before shifting from ROAD
to PUMP or back make sure the
apparatus drive shaft has stopped
turning. Attempting to shift with the
drive shaft turning will result in damage
to the gears.
The standard gearboxes are shifted from
road to auxiliary output operation with a
manual shift lever. Other shift options
available are vacuum power and air power
shift mechanisms. Movement of the shift
controls while the apparatus transmission is
in neutral will engage the drive shaft to
drive the auxiliary equipment. After shifting
the gearbox from road to auxiliary output
mode, placing the transmission back into
drive gear provides power to the gearbox.
Indicator lights mounted in the driver’s
compartment and at the pump operator’s
panel provide visual indication as to when
the gearbox has been shifted from road to
auxiliary output mode and when all
interlock conditions have been met for safe
operation. Electrical signals for these lights
are provided by switches that are actuated
by the gearshift shaft.