FMI Q431 "Q User Manual
Q” pump instructions cerampump, Safety instructions
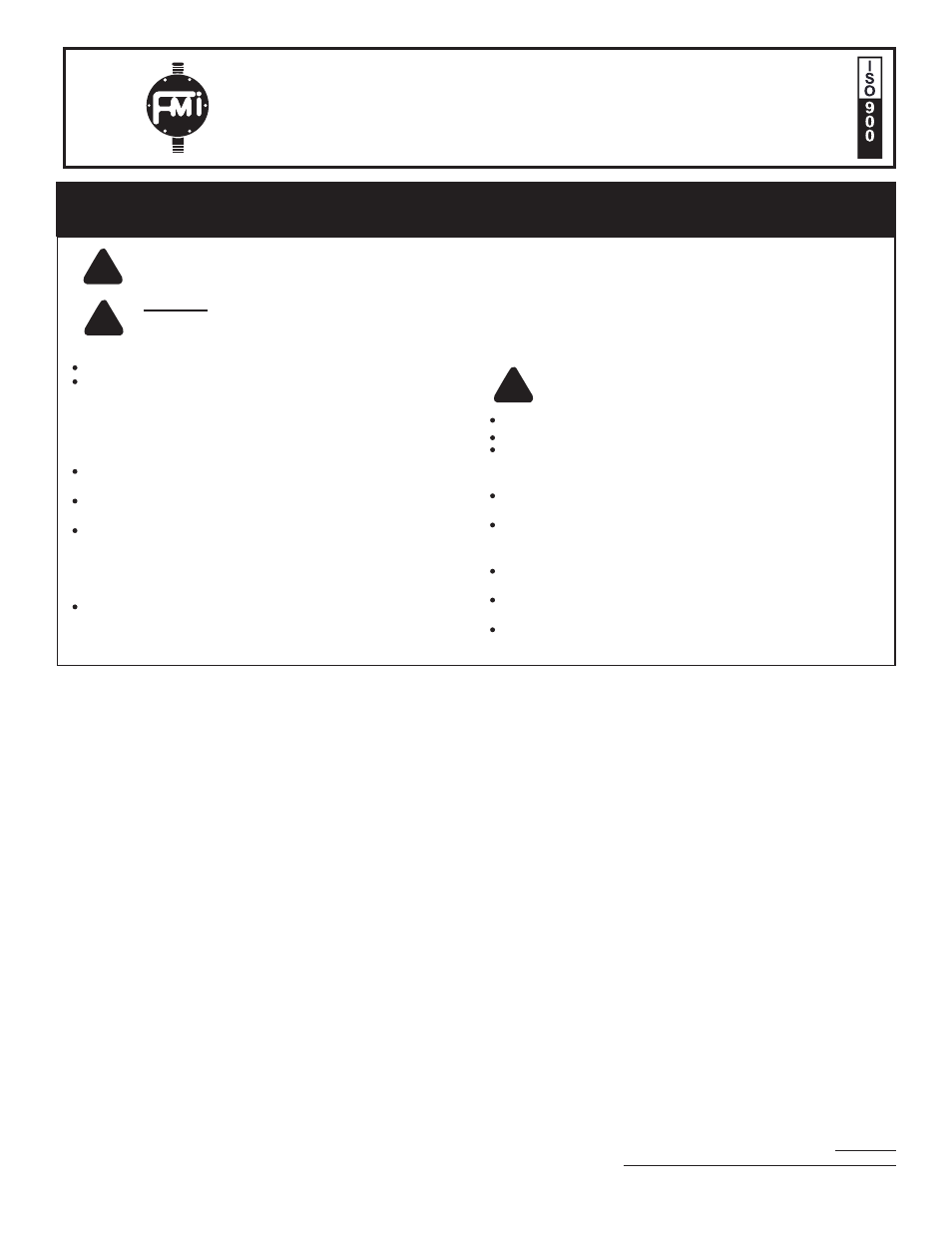
INSTALLATION & OPERATING TIPS
1. CLEAN FLUIDS. Abrasives in the pumped fluid
may damage cylinder and piston surfaces and
should, therefore, be avoided. Carbon cylinder lin-
ers and stainless steel pistons are particularly sus-
ceptible to abrasion by particulate matter in the
pumped stream. Ceramic piston/cylinder compo-
nents are more tolerant of suspended solids, ex-
cept solids that tend to flock and impede the
movement of the piston in the cylinder.
2. COMPATIBLE FLUIDS. Pump only fluids com-
patible with materials of construction of the pump
head you have selected.
3. WET OPERATION. The pumped fluid provides
surface cooling and lubrication to the piston and
cylinder of your FMI PUMP. Therefore, avoid dry
operation (except pumps specifically designated
“gas pump”).
4. FLOW VOLUME AND DIRECTION. Angular de-
flection of the cylinder with respect to the zero
point on the calibration scale of your FMI “Q”
PUMP controls flow magnitude and direction e.g.,
with the cylinder pointer at 10 on the left scale, fluid
will be passed from the right port to the left port at
100% of the maximum rated volume; with the
pointer at 10 on the right scale, fluid will pass from
the left port to the right port at maximum rate. Set
at 5 on the scale, flow rate will be 50% of maxi-
mum; at 4, it will be 40%; at 3, 30%, etc., etc. The
flow control setting may be changed (including flow
reversal) at any time while the pump is operating or
idle. Slightly loosen the two thumb screws and turn
the STROKE LENGTH ADJUSTMENT KNOB.
Retighten thumb screws once the desired setting
is reached.
5. PISTON SEALS. The R408 seals that keep your
PUMP piston dry are not “just ordinary plastic
discs.” They are precisely cut and hot formed from
sheets of a chemically inert fluorocarbon, specifi-
cally formulated for resistance to wear, abrasion,
heat and chemical attack.
Each R408 seal possesses an exceptional me-
chanical memory which allows it to maintain a rel-
atively constant wiping pressure on the piston,
compensating for seal wear as it occurs. Properly
maintained in clean condition, the original seals on
a FMI PUMP may be expected to last the life of
the pump. If they are removed for any reason,
they should be carefully cleansed of all foreign par-
ticles prior to re-assembly. Seal seats must also be
free of particles. (please see para 18)
6. DIAL INDICATOR. (optional) The Dial Indicator
Kit is for fine adjustment and continuous monitor-
ing of your “Q” pump flow rate settings.
To adjust Dial Indicator equipped pumps:
1.Loosen thumb screws, turn STROKE LENGTH
ADJUSTMENT KNOB, moving cylinder assembly
to neutral (zero-flow position).
2. Adjust indicator pointers until they read zero on
both dials.
3.You are now ready for fine setting by turning
STROKE LENGTH ADJUSTMENT KNOB until
you achieve desired flow rate on dial. To prevent
system backlash always turn STROKE LENGTH
ADJUSTMENT KNOB two turns or one full revolu-
tion of large dial beyond desired setting, then ad-
just back.
7. 4-20 mA CONTROL for automatic response to
remotely generated 4-20 milliamp signals is stan-
dard on V300 controllers. The input can be either
grounded or ungrounded. The current source con-
nects to terminal posts mounted on front cover as-
sembly of the STROKE RATE CONTROLLER. Be
sure to observe correct polarity. For complete
hook-up and operating information see page 10.
8. PRESSURE. Do not operate pump against
head pressures in excess of design specification.
Drive arm on piston may bend or break under
overload and other irreparable damage may be
suffered. Check your fluid circuit before apply-
ing power to the pump!
9. ELECTRICAL PROTECTION. All FMI PUMPS
are positive displacement in struments and should
be protected by lowest possible “slo blow” fuse or
circuit breaker electrical arrangements. “QV” units
come equipped with .75 amp fuses.
10. NOISE AT HIGH PUMP RATES. A metallic
hammering noise during operation of your pump
1
IN-Q431-09A
Before using any Fluid Metering, Inc. product read the following safety instructions as well as specific product
specifications and operating instructions.
Warning! Fire, electrical shock or explosion may occur if used near combustibles, explosive atmosphere, corrosive air,
wet environment or submerged in fluid.
!
Caution! Fire, electrical shock, injury and damage may
occur if not used in accordance with Fluid Metering, Inc.
specifications and operation instructions.
Do not put wet fingers into power outlet of unit.
Do not operate with wet hands.
Do not operate drive assemblies that require a hard mount
(to be bolted down) unless they are mounted per Fluid Metering, Inc.
specifications. If not, injury may occur and/or damage to unit.
Do not touch any rotating pump or motor components: injury may
occur.
Do not run pump dry, unless designed for that service.
Running dry is harmful to the pump, and will cause excessive heating
due to internal friction.
Check pump rotation and inlet/outlet pump port orientation before
connecting power to pump. If not, injury may occur.
When pulling out cords from outlets do not pull cord, grasp plug to
prevent plug damage or electrical shock.
Fluid Metering, Inc. Drive Motors become HOT and can cause
a burn
. DO NOT TOUCH!
Turn off the electrical power before checking pump for any problems.
Connect motor, speed controllers, or any other electrical devices
based on Fluid Metering Inc. specifications. Any unauthorized work
performed on the product by the purchaser or by third parties can im-
pair product functionality and thereby relieves Fluid Metering, Inc.
of all warranty claims or liability for any misuse that will cause
damage to product and/or injury to the individual.
Power cables and leads should not be bent, pulled or inserted by ex-
cessive force. Otherwise there is a threat of electrical shock or fire.
Replace any inline fuses only with fuse rating as specified by Fluid
Metering, Inc.
When pump/drive is under operation, never point discharge tubing
into face or touch any rotating components of pump.
In a power down thermal overload cut-in condition, unplug or turn off
power to pump. Always allow a cool down period before restarting:
otherwise, injury or damage may occur.
For 30 seconds after power is removed from pump/drive: do not
touch any output terminals. Electrical shock may occur because of
residual voltage.
!
SAFETY INSTRUCTIONS
!
1
“Q” PUMP INSTRUCTIONS
CeramPump
®