Replacement guidelines, Shaft and sleeve inspection, Bearing frame inspection – Bell & Gossett P2001406C Series e-1510 Centrifugal Pumps User Manual
Page 30: Impeller trimming guidelines
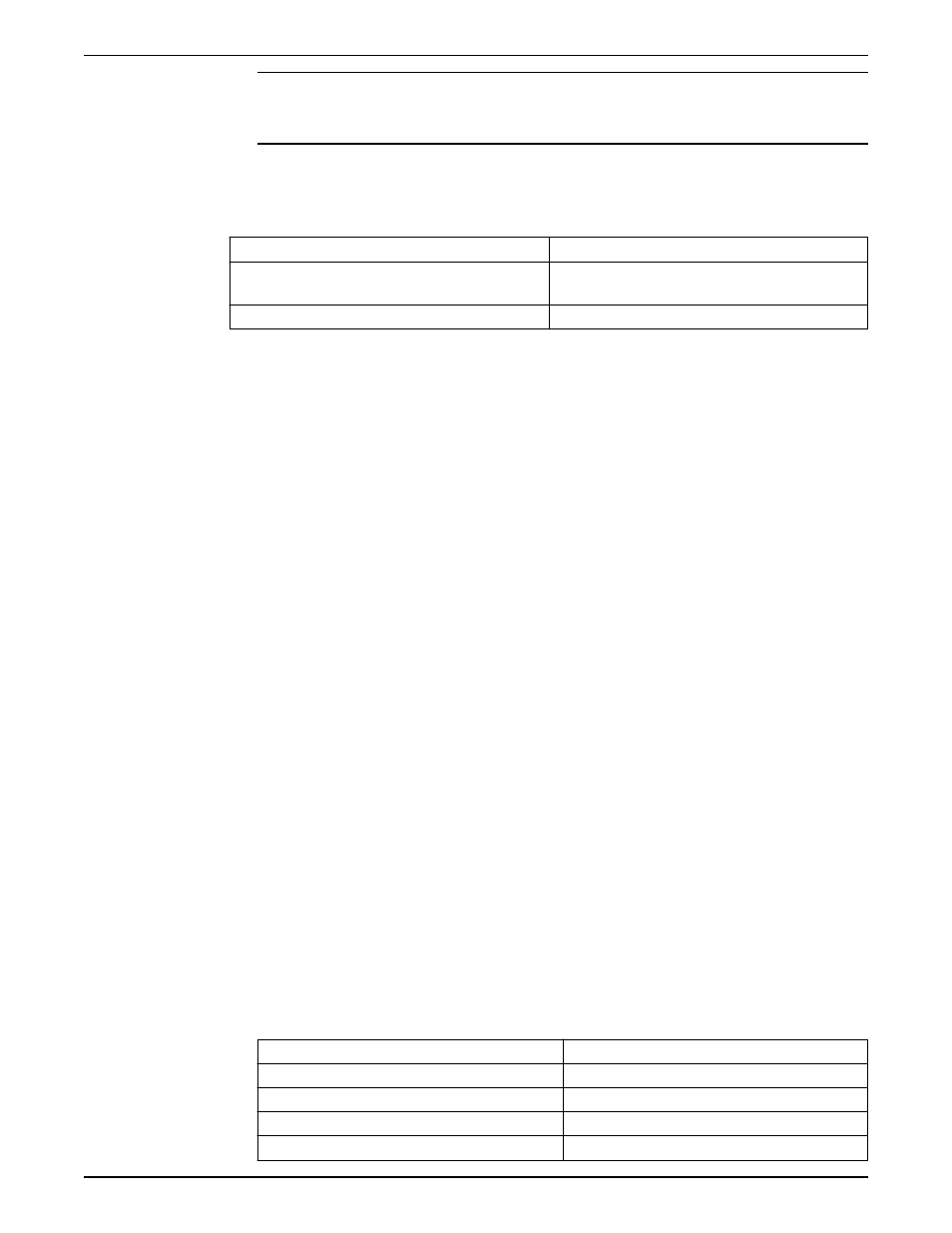
NOTICE:
Protect machined surfaces while you clean the parts. Failure to do so may result in
equipment damage.
Replacement guidelines
Impeller replacement
This table shows the criteria for replacing the impeller:
Impeller parts
When to replace
Impeller vanes
• When grooved deeper than 1/16 in. (1.6 mm), or
• When worn evenly more than 1/32 in. (0.8 mm)
Vane edges
When you see cracks, pitting, or corrosion damage
Gaskets, O-rings, and seat replacement
• Replace all gaskets and O-rings at each overhaul and disassembly.
• Inspect the seats. They must be smooth and free of physical defects.
• Replace parts if the seats are defective.
Shaft and sleeve inspection
Inspection criteria
Inspect the shaft and sleeve according to this criteria:
• Thoroughly clean the shaft and sleeve.
• Thoroughly clean the coverplate seal cavity.
• Inspect the surface for damage such as pitting, corrosion, nicks, and scratches.
Replace these parts if they are damaged.
Bearing frame inspection
Check the bearing frame for these conditions:
• Visually inspect the bearing frame and support foot for cracks.
• Inspect the bearing frame for smooth and free operation.
• Inspect the bearing frame for contamination by pumped fluids.
Repair or replace the bearing frame as necessary.
Impeller trimming guidelines
Machining
When it is necessary to reduce the pump flow rate and generated head by trimming the
impeller diameter, the following guidelines apply for stainless steel impellers:
• Review the pump hydraulic selection data and consult your local Xylem representative
to select the proper reduced diameter.
• For the e-1510-4AD model, before trimming the impeller refer to the e-1510-4AD
angle cut guidelines.
• The recommended machining insert is Sandvick CNMG 432-1125 or equal without
coolant at 250 surface feet per minute (SFM) (76.2 surface meter per minute (SMM)).
• To calculate the spindle speed (RPM), use the formula RPM=(SFM*12)/(3.1416*
diameter of cut, in.) (RPM=(SMM*39.37)/(3.1416* diameter of cut, mm/25.4)). This
results in the following:
Impeller Maximum Diameter
Recommended Maximum Spindle Speed (RPM)
7 in. (177.8 mm)
136
9.5 in. (241.3 mm)
100
11 in. (279.4 mm)
87
13.5 in. (342.9 mm)
71
Maintenance
28
Series e-1510 Installation, Operation, and Maintenance Manual