Permitted indicator values for alignment checks, Align the coupling, Float control installation – Goulds Pumps API 3171 - IOM User Manual
Page 25
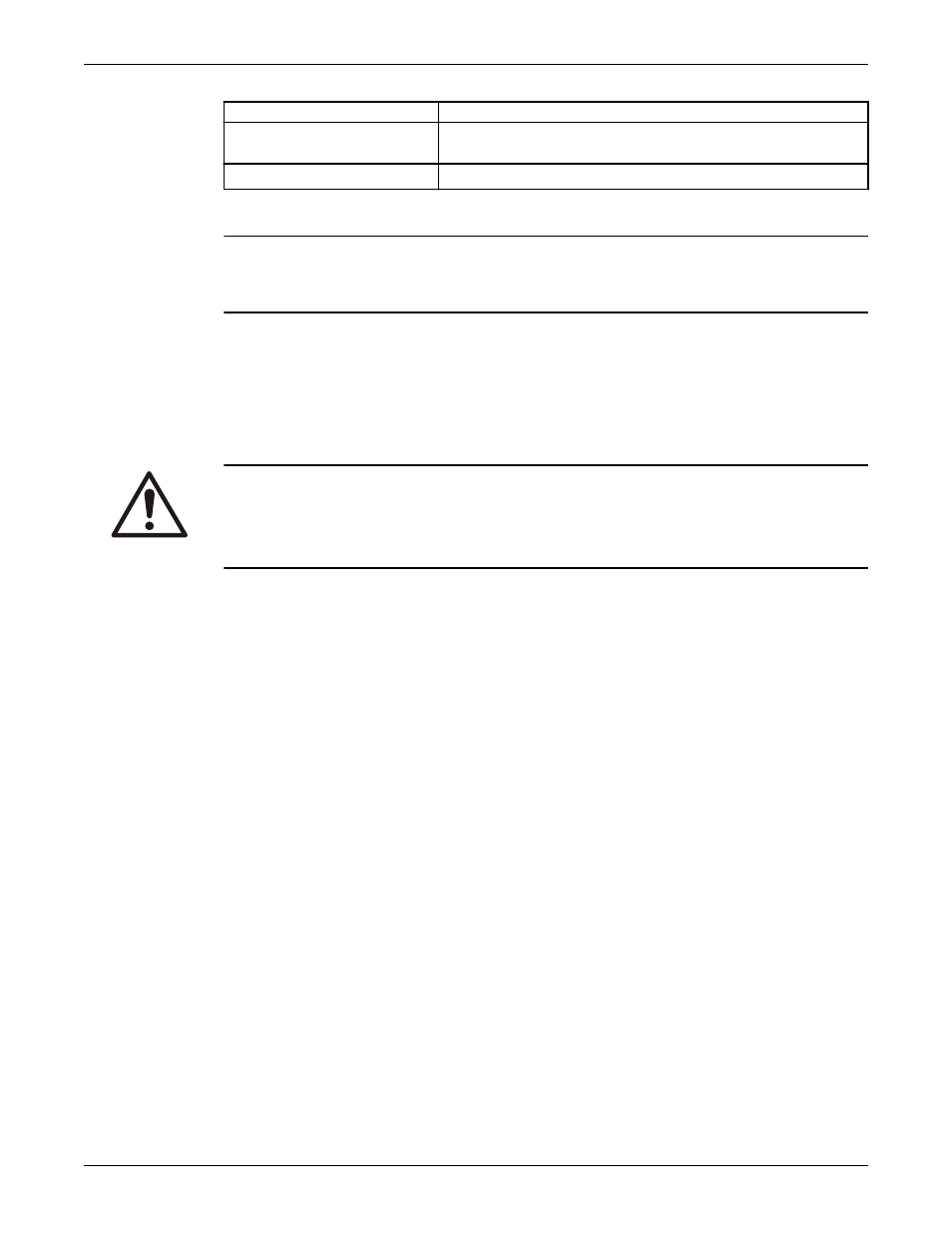
Final alignment (hot alignment) checks
When
Why
After the first run
This ensures correct alignment when both the pump and the driver
are at operating temperature.
Periodically
This follows the plant operating procedures.
Permitted indicator values for alignment checks
NOTICE: The specified permitted reading values are valid only at operating temperature. For cold
settings, other values are permitted. You must use the correct tolerances. Failure to do so can result in
misalignment and reduced pump reliability.
When dial indicators are used to check the final alignment, the pump and drive unit are correctly aligned
when these conditions are true:
• The total indicator runout is a maximum of 0.002 in. (0.05 mm) at operating temperature.
• The tolerance of the indicator is 0.0005 in./in. (0.0127 mm/mm) of indicator separation at operating
temperature.
Align the coupling
WARNING:
• Disconnect and lock out electrical power before installing or servicing the pump.
• When installing in a potentially explosive environment, make sure that the motor is properly certified.
• The coupling used in an ATEX classified environment must be properly certified.
Alignment of the pump and motor is of extreme importance for trouble-free mechanical operation.
Straight-edge alignment by an experienced installer is adequate for most installations. Use dial indicators
for disc couplings and applications where alignment to tighter tolerances is desirable. In these cases, use
standard dial indicator procedures.
1. Check for coupling alignment by using either the reverse dial indicator method or laser alignment
tools.
2. Move the motor until you achieve the correct alignment.
Refer to the coupling manufacturer literature for proper alignment criteria.
3. Install discs between the hubs per the manufacturer's directions included with the pump data package.
4. Tighten all motor bolts.
Float control installation
ITT supplies several different float controls. Refer to the float control installation instructions provided
with the controls for the proper installation procedure. This topic describes the Square D 9036 Simplex
and Square D 9038 Duplex float controls.
How float controls work
The on and off levels of the Square D 9036 simplex and the Square D 9038 duplex are controlled by
adjusting the collars (335). As the liquid level rises, the float rises to contact the upper collar and the
upward movement of the float rod causes the mechanical switch inside the control to close. This
completes the circuit to the starter. Operation continues until the liquid level drops low enough for the
float to contact the lower collar. This pulls the rod down, opening the switch and turning off the pump.
The only difference between the Square D 9036 simplex and the Square D 9038 duplex is in the operating
sequence. For the Square D 9038 duplex, the first pump starts as the water level rises. This allows the float
to contact the upper collar. When the water level drops down and shuts off the first pump, a lever arm
inside the control mechanically switches to the second pump and it comes on for the next cycle.
Installation
Model API 3171 Installation, Operation, and Maintenance Manual
23