Construction details – Goulds Pumps 3500XD - IOM User Manual
Page 15
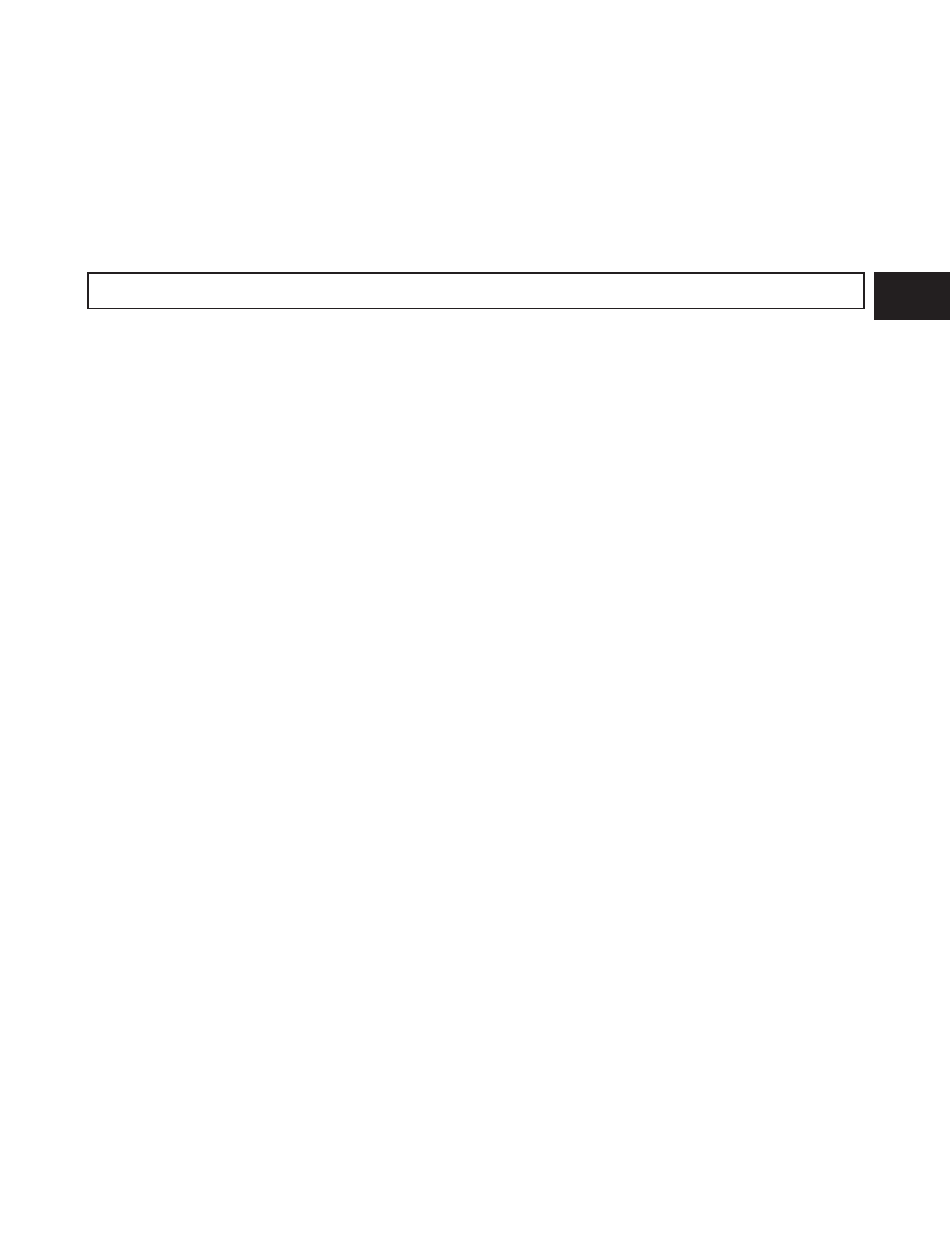
Air separation occurs due to the action of X-Ducer in Zone
1. The air collects at the center of the X-Ducer and is
pumped through balance holes in the impeller shroud. Any
remaining paper stock is separated from the air behind the
impeller via a patented secondary separation device (U.S.
Patent #5,087,171) in Zone 2. The paper
stock is pumped to the casing volute via large back
pump-out vanes (Zone 4), and the air flows to atmosphere
or to a vacuum source depending on operating conditions
(Zone 3).
Pressure generation takes place in the impeller and casing
volute in the normal manner once the air has been removed
(Zone 4).
CONSTRUCTION DETAILS
Casing - The casing is vertically split, top centerline
discharge, providing a back pullout design for ease of
maintenance. A renewable sideplate is incorporated into
the design to reduce maintenance costs. The sideplate is
sealed with an O-ring and gasket.
Impeller - The impeller is an open design with a full back
shroud. It is designed for a matched close clearance with
the suction sideplate to provide optimum efficiency. The
impeller has balance holes to allow air to pass through the
back shroud. Remaining paper stock is returned to the
casing volute via large pump-out vanes.
The impeller is keyed to the shaft and sealed with Teflon
®
O-rings.
X-Ducer - The X-Ducer creates turbulence in the standpipe
and feeds the pulp into the pump suction. The design
concentrates the air present in the pulp suspension where it
is expelled from the degas holes in the impeller into the
degas system. The X-Ducer is key driven and secured to
the shaft with a rotor nut. Teflon
®
o-rings protect the shaft.
Repeller - A patented (U.S. Patent # 5,087,171) repeller
behind the impeller provides superior secondary air
separation. The repeller is keyed to the shaft and sealed
with Teflon® O-rings.
Stuffing Box Cover - The stuffing box cover contains a
degasification nozzle through which excess air is removed.
Shaft sealing is accomplished with a mechanical seal as
standard.
Shaft/Shaft Sleeve - The shaft is designed to minimize
deflection in the seal area and at the impeller. It is
protected from the pumpage by a replaceable sleeve sealed
with a Teflon® O-ring.
Power End - A heavy duty power end is provided for
maximum reliability. It includes a duplex angular contact
thrust bearing and a cylindrical roller radial bearing for
maximum load carrying ability. The bearings are sized for
a two year minimum L'
10
(14 year average) life under the
worst operating conditions. Oil lubrication is standard and
the frame is sealed at both ends with labyrinth oil seals.
External axial adjustment is provided to maintain the
proper impeller clearance for optimum efficiency.
3500XD IOM 8/07
11
2