Conditions, issues and ratings, High temperature installation, Membrane seam failure – Dow Protected Membrane Roof EN User Manual
Page 19: Plant growth on pmr assemblies, The issue, Discussion, Conclusion
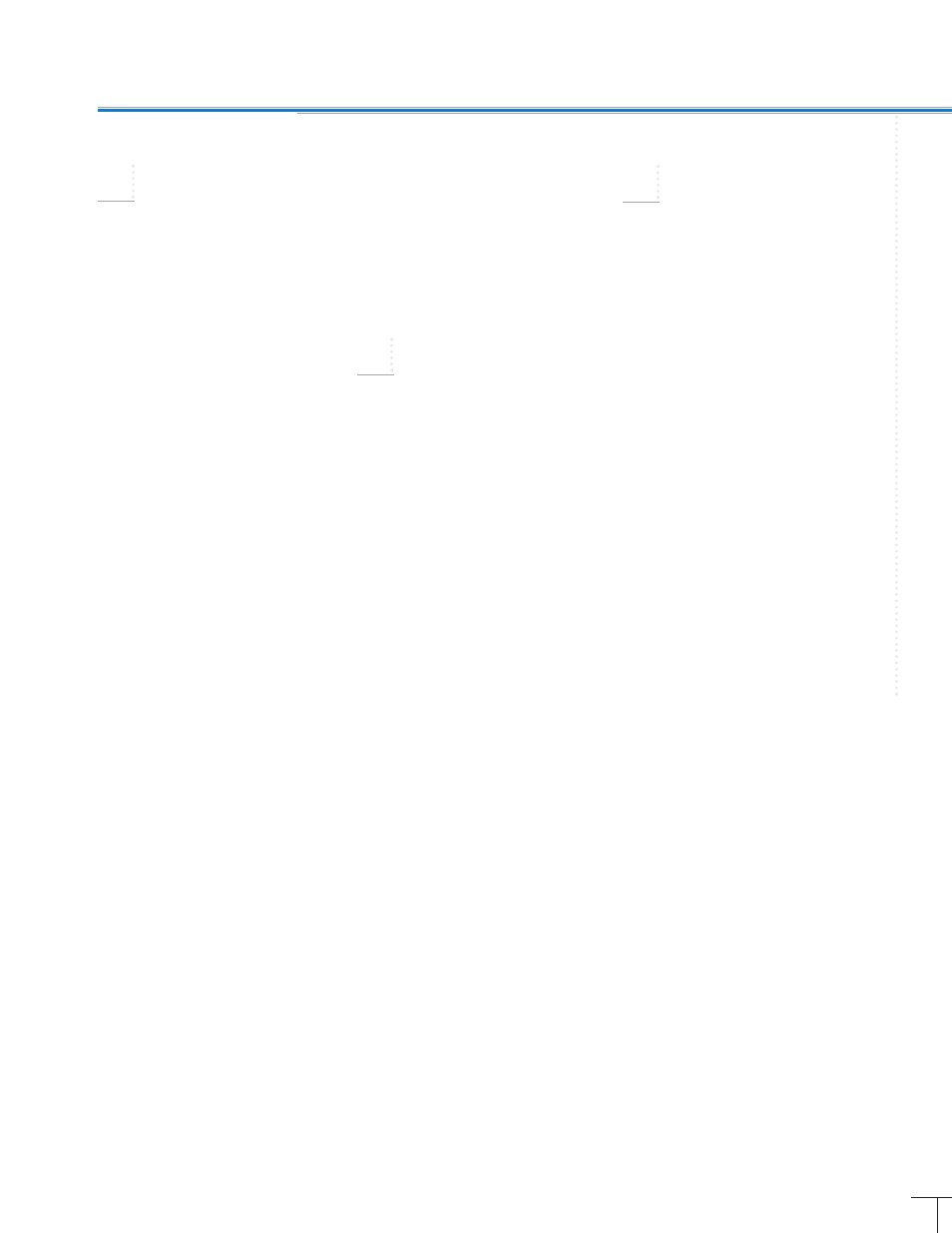
C
O
N
D
I
T
I
O
N
S
,
I
S
S
U
E
S
A
N
D
R
A
T
I
N
G
S
–
S
p
e
c
i
a
l
C
o
n
d
i
t
i
o
n
s
a
n
d
I
s
s
u
e
s
1 9
High Temperature
Installation
THE ISSUE
In high temperature locations,
PMR assemblies should not
be covered with a dark fabric
prior to laying the ballast
because of the potential adverse
effect on the STYROFOAM
™
Brand Extruded Polystyrene
Foam Insulation.
DISCUSSION
Like many insulations, higher
temperatures may cause permanent
distortion and/or long-term
creep. The maximum use
temperature for STYROFOAM
™
Brand Extruded Polystyrene
Foam Insulation is 165°F (74°C)
for continuous use, with short-
term exposure up to 190°F
(88°C).
Typically, this concern arises
in warmer locations (e.g., south-
ern U.S.) when STYROFOAM
™
Brand Insulation is placed under-
neath a dark fabric prior to lay-
ing the ballast. Given the right
conditions, the temperature on
the top of the insulation may
reach close to the upper limits
for polystyrene insulation and
cause some distortion. Experience
has shown that when STYROFOAM
™
Brand Insulation is exposed to
both direct sunlight and an out-
door air temperature over 90°F
(30°C), distortion can occur in
as little as 30 minutes when a
dark fabric is installed over the
insulation. To prevent this phe-
nomenon during hot weather,
temporarily place white opaque
polyethylene film on the insula-
tion until the ballast is laid (or
use a white filter fabric).
In addition, reflective surfaces
such as glass or metal wall panels
can substantially increase surface
temperatures. When combined
with a dark fabric, extremely
high surface temperatures can
occur, increasing the potential
for distortion of rigid foam
boards. Follow the same precau-
tion as mentioned above.
CONCLUSION
In high temperature locations,
the temporary use of white
opaque polyethylene film laid
on the insulation until the
ballast is laid will prevent any
distortion of the insulation (or
use a white filter fabric).
Membrane Seam
Failure
THE ISSUE
Failures at the seams in
thermoset membranes may
be worse with PMR because
the membrane stays damp.
DISCUSSION
Thermoset membranes (such
as EPDM and neoprene) were
historically seamed with a con-
tact adhesive. Seam failure due
to moisture intrusion or other
contaminant was a concern for
this type of membrane because
the membrane stays damp in a
PMR, potentially resulting in an
increase in seam failure. In fact,
Dow never received a complaint
about this perceived concern.
In today’s EPDM system, a
seam tape is used. This tape has
exhibited excellent performance
and this is no longer an issue.
CONCLUSION
There are no documented
cases of seam failure related to
the PMR application.
Plant Growth on
PMR Assemblies
THE ISSUE
Periodically, plant growth
will occur on PMR and other
low-sloped roofs. Can this be
avoided?
DISCUSSION
At times, grass, weeds or small
trees may grow on both PMR
and conventional roofs. Good
roofing practice should include
a maintenance program that
includes periodic inspection for
this type of growth. Any plant
growth should be pulled out
and, if required, the area treated
with a weed killer.
Roots from plant growth can
sometimes damage the mem-
brane if left unchecked. With a
PMR system, there is less chance
of this happening since the
membrane is protected by the
insulation, fabric and ballast.
CONCLUSION
A preventive maintenance and
inspection program should
include inspection and removal
of any plant growth.
Conditions, Issues and Ratings
S P E C I A L
C O N D I T I O N S
A N D
I S S U E S
®™Trademark of The Dow Chemical Company (“Dow”) or an affiliated company of Dow