Equipment inspection – Pulsafeeder Pulsa Series Pulsamatic Controls User Manual
Page 8
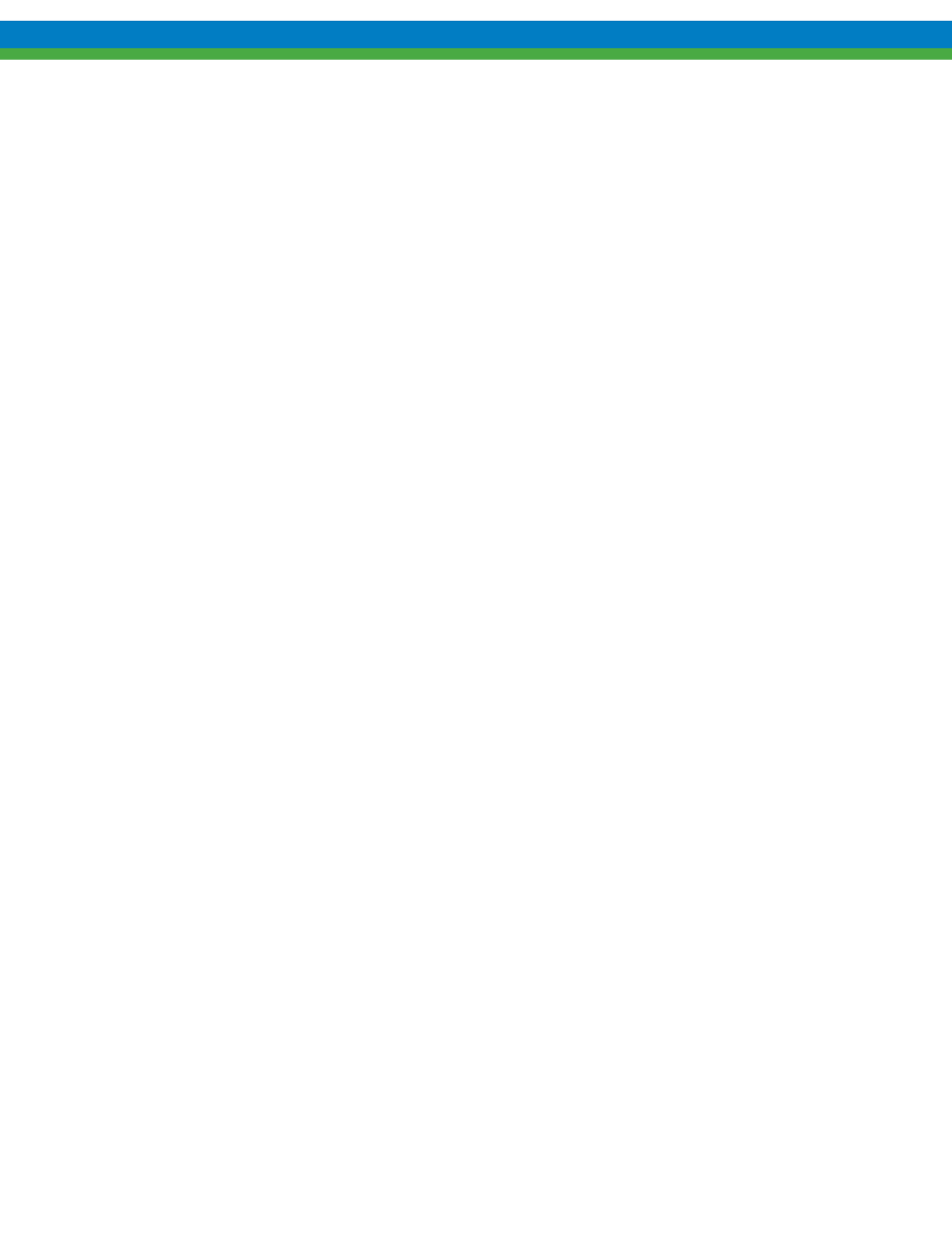
5
2. Equipment Inspection
1. Check all equipment for completeness against the order and for shipping damage. Shortages or
damage should be reported immediately to your PULSA Series representative.
2. Check pump and PULSAmatic stroke control identification tags for serial and model numbers.
There are two tags: one on the pump gearbox which includes the pump model number and
another on the PULSAmatic enclosure. The pump gearbox serial number identifies the
PULSAmatic actuator as well as any separately mounted control stations. Each should
correspond to the information on the parts lists. Use these reference numbers whenever
corresponding with the factory.
3. Check the envelope containing this bulletin for service parts list and special drawings and
wiring diagrams for specified control options.
3. Procedural Notes
Electrical repairs and calibrations should be undertaken only by an electronic technician q2ualified
in the maintenance and repair of linear (analog) industrial process control equipment.
A digital voltmeter and a process control signal generator are required for electronic calibrations.
Troubleshooting and repair may require access to the mechanism linking the actuator control to the
oscillating housing inside the pump gearbox. This requires removal and replacement of the rear
gearbox cover assembly. Refer to the pump operations manual for the description of these
operations.
Detailed circuit board schematics, containing component identifications, are available from the
factory to facilitate electronic circuit troubleshooting and repair at the board level.
The following conventions and procedures apply throughout this bulletin.
1. “Zero Stroke” refers to a zero, or (000) setting on the mechanical stroke counter.
“Full Stroke” refers to a full or (100) setting on the mechanical stroke counter.
2. A “low end” input control signal is one that commands the pump to zero stroke
A “high end” input control signal is one that commands the pump to full stroke.
Note that the signal values are inverted in the reverse acting option so that, for example, a 4-20
mA signal commands full to zero stroke. In this case, 4 mA is the high end signal. See
“Options” under “principals of Operation” above for signal definitions.
3. Pump stroke can be manually or automatically set as required for calibrations and adjustments.
References to the disable switch (“out” for manual, “in” for automatic) may be omitted.
Manual, or hand wheel adjustments made while the pump is not operating, require that
pressures be relieved from both the suction and discharge lines.
4. Wiring terminals are indentified on the circuit board and referred to directly. For example
TB2-3 refers to terminal No. 3 on Terminal Board No. 2, (reference Figure 4).
CAUTION: When troubleshooting, always remove signal potential prior to
disconnecting AC power. This will help protect integrated circuits on the circuit
board.