Midco G69B User Manual
Page 3
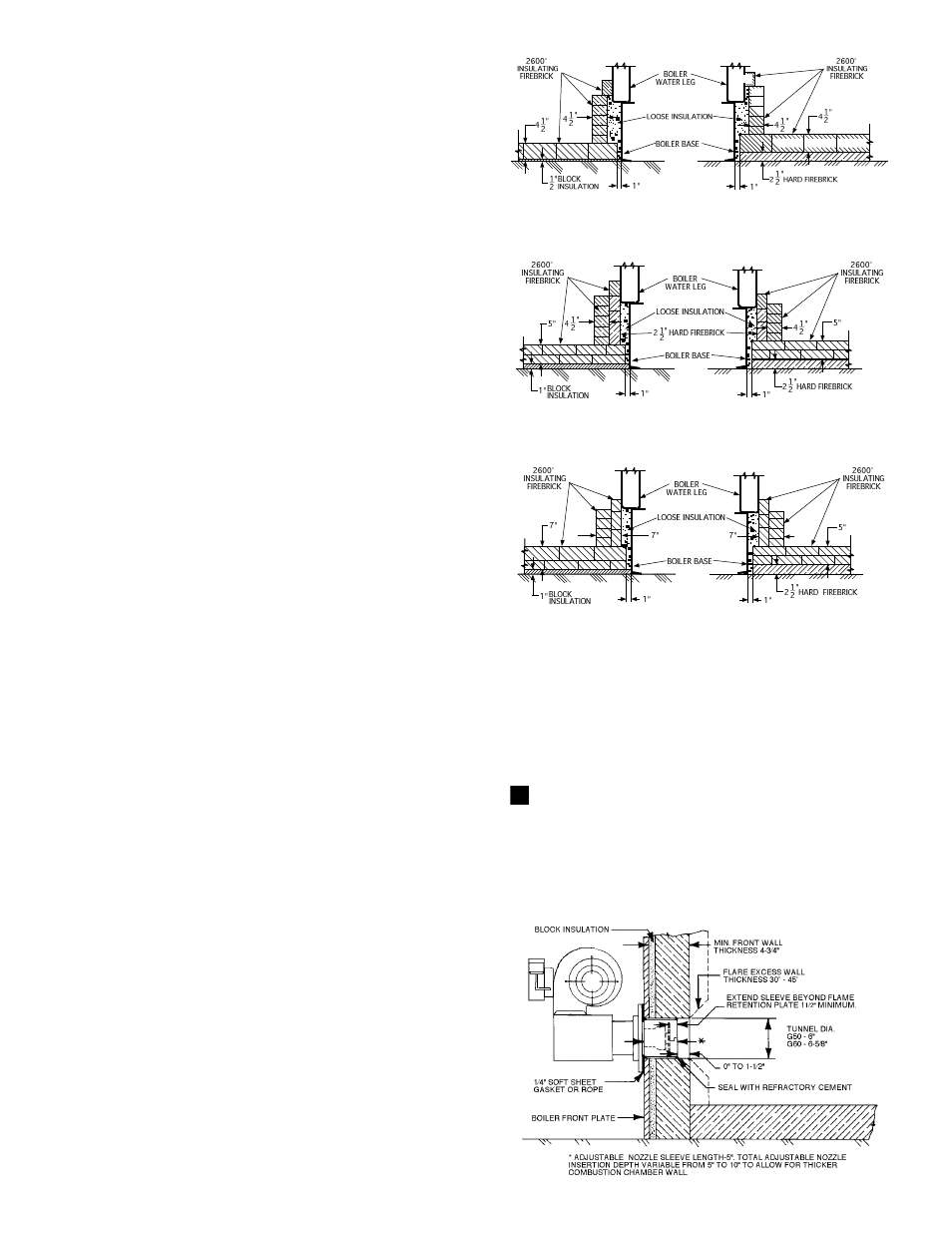
FIGURE 1
Typical Floor And Wall Construction For
225,000 BTU Per Square Foot. (Standard)
FIGURE 2
Typical Floor And Wall Construction For
275,000 BTU Per Square Foot.
FIGURE 3
Typical Floor And Wall Construction For
350,000 BTU Per Square Foot. (Maximum)
The burner is equipped with a mounting flange for direct
attachment to the boiler front, and mounting brackets for
legs. Use both if necessary for rigid installation. The
burner nozzle must not extend into the combustion
chamber. It should be sealed into the opening as shown
in Figure 4.
WARNING:
BURNER CABINET MUST BE
MOUNTED IN ORIENTATION IN FIGURES 4 AND 7.
ANY OTHER MOUNTINGS MAY CAUSE A
DANGEROUS CONDITION, AND WILL VOID BURNER
WARRANTY AND AGENCY APPROVALS.
NON-STANDARD ARRANGEMENTS MAY BE
AVAILABLE FOR SOME MODELS-CONSULT
FACTORY FOR DETAILS IF REQUIRED.
FIGURE 4
Construction at Burner Entrance
II
GAS UTILIZATION EQUIPMENT
The heating system, both the gas utilization equipment
and the distribution system, should be in good repair and
sufficient to properly heat the building. It should be
determined if any serious faults are present that would
cause excessive fuel consumption, unsafe operation or
improper heating, and measures taken to correct them.
After the grates and grate operating parts have been
removed from the firebox, the boiler interior should be
thoroughly cleaned, removing all adhering dirt, tars,
scale and soot. All joints should be cemented to prevent
excess air infiltration into the boiler. Clean out doors
should be checked for close fit, and sealed with furnace
cement if they fit poorly.
Firing door catches should be filed off or otherwise
arranged so that the door will open easily to relieve
pressure. No positive catches should be used. The use
of a spring type door holder is recommended.
III
COMBUSTION CHAMBER
The UNIPOWER gas burner is designed for "in-shot"
firing. It can be fired into the ashpit of a boiler designed
for solid fuels, or it can be fired into the primary heat
exchanger of a boiler designed for liquid or gaseous
fuels. The ashpit installation requires a refractory lining.
The combustion chamber serves to contain and promote
combustion and to protect non-heat exchange surfaces
from direct flame contact. Built-up combustion chambers
should be made of 2600
o
insulting firebrick. As an
alternative, a monolithic floor can be cast in place, using
a high temperature (2400
o
), light weight insulating
refractory. Check with your supplier to determine the
thickness which will yield equivalent insulating qualities.
The top of the combustion chamber should be positioned
2 to 6" above the base of the heat exchanger. If the
combustion chamber is to be set directly on the floor,
provide a minimum of 1/2" insulating millboard or
magnesia block underlay for floor protection. Use high
temperature fill such as vermiculite in voids around the
combustion chamber. Any portion of the heat exchanger
not exposed to circulating air or water should be covered
with insulating firebrick.
The combustion chamber sizes given in Table 1 are
based on the maximum rated burner capacity. If the
input is to be permanently set at a reduced rate the
combustion chamber floor area can be reduced
proportionately to the proposed input, with the length as
closely proportioned to twice the width as possible.
Where recommended size combustion chambers
(225,000 BTU/sq. ft.) can be accommodated, the type of
construction shown in Figure 1 should be used. If lack of
space prohibits use of this construction, higher BTU
values per square foot can be allowed for by using the
constructions shown in Figure 2 and 3.
The back wall of the combustion chamber should be
carried 2 or 3 courses higher and overhung to deflect the
flames from direct impingement on the rear heat
exchanger surface. Hard firebrick should be used to
prevent erosion of the brick by high velocity gases.
-3-