Sar 331 sa gds – Dake Model SAR 331 User Manual
Page 27
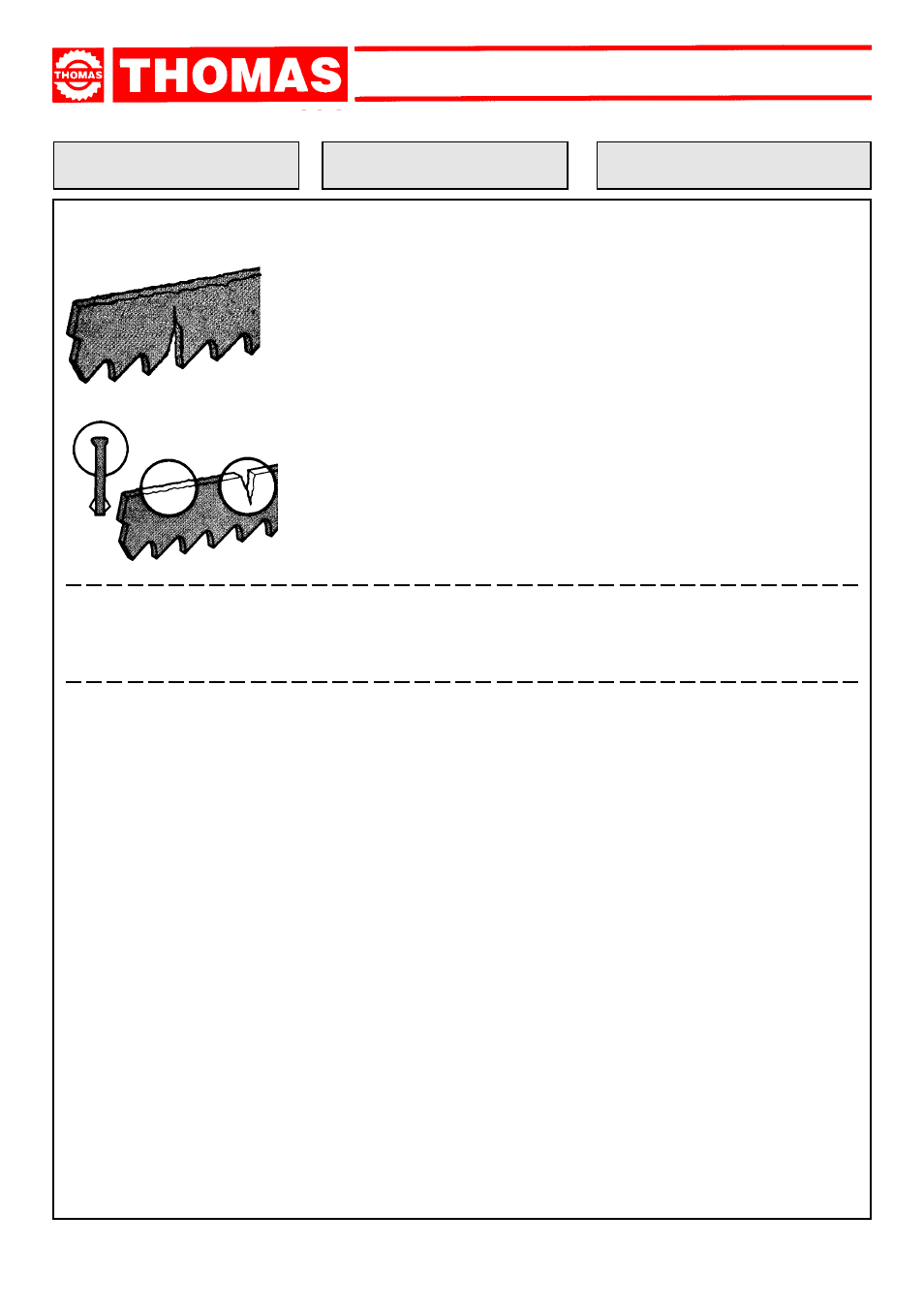
27
SAR 331 SA GDS
FAULT
PROBABLE CAUSE
REMEDY
Check distance between blocks (see “Ma-
chine adjustments” in the
Blade Guide
Blocks section): extremely accurate guiding
may cause cracks and breakage of the tooth.
Clean carefully.
Approach head as near as possible to ma-
terial to be cut so that only the blade section
employed in the cut is free, this will prevent
deflections that would excessively stress the
blade.
The back of blade rubs against the support
due to deformed or poorly welded bands (ta-
pered), causing cracks and swelling of the
back contour.
Check level of liquid in the tank. Increase the
flow of lubricating refrigerant, checking that
the hole and the liquid outlet pipe are not
blocked. Check the emulsion percentage.
Replace it.
Adjust it (see Chapter “Machine adjust-
ments” in
Blade guide section).
Check fastenings of the blade guide blocks
as to the counter-vice so that they are not
too loose and adjust blocks vertically; bring
into line the position of the degrees and if
necessary adjust the stop screws of the
degree cuts.
Check and vertically re-adjust the blade guide
blocks; reset proper side guide play (see
Chapter “Machine adjustments” in
Blade
guide section).
Decrease advance, exerting less cutting
pressure. Adjust the braking device if
mounted on the machine.
Approach it as near as possible to material
to be cut so that only the blade section em-
ployed in the cut is free, this will prevent de-
flections that would excessively stress the
blade.
Replace it.
Blade with major density of teeth is being
used, try using one with less teeth (see Chap-
ter “Material classification and blade se-
lection” in the
Blade Types section).
Blade guide pads not regulated or dirty
because of lack of maintenance
Blade guide block too far from material
to be cut
Improper position of blade on flywheels
Insufficient lubricating refrigerant or
wrong emulsion
Damaged or chipped blade guide
pad
Tight or slackened blade guide bearing
Blade not parallel as to the counter-vice
Blade not perpendicular due to the ex-
cessive play between the guide pads
and maladjustment of the blocks
Too fast advance
Blade guide block too far from material
to be cut
Worn out blade
Wrong tooth pitch
STREAKED OR ETCHED BANDS
CUTS OFF THE STRAIGHT