Sar 331 sa gds – Dake Model SAR 331 User Manual
Page 26
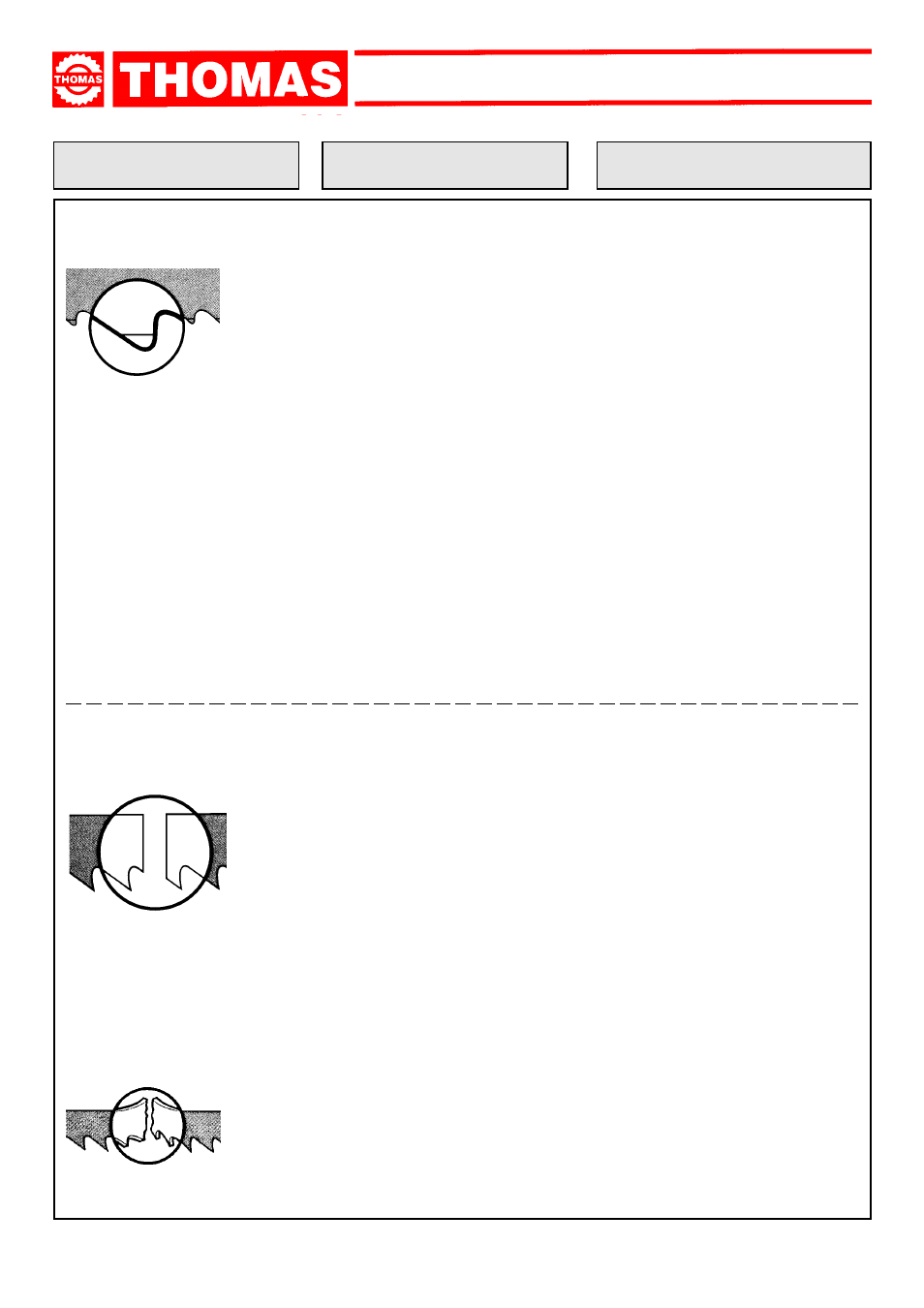
26
SAR 331 SA GDS
FAULT
PROBABLE CAUSE
REMEDY
See “Material classification and blade se-
lection” in the
Blade running-in section.
Turn teeth in correct direction.
Use a superior quality blade.
Decrease advance, exerting less cutting
pressure. Adjust the braking device if
mounted on the machine.
Change speed and/or type of blade.
See chapter on “Material classification and
blade selection”, in the section
Blade selec-
tion table according to cutting and feed
speed.
Material surfaces can be oxidised or covered
with impurities making them, at the begin-
ning of the cut, harder that the blade itself,
or have hardened areas or inclusions inside
the section due to productive agents used
such as casting sand, welding wastes, etc.
Avoid cutting these materials or in any case
perform cutting with extreme care, clean-
ing and removing such impurities as quickly
as possible.
Check level of liquid in the tank. Increase the
flow of lubricating refrigerant, checking that
the hole and the liquid outlet pipe are not
blocked.
Check the emulsion percentage.
The welding of the blade is of utmost impor-
tance. The meeting surfaces must perfectly
match and once they are welded they must
have no inclusions or bubbles; the welded
part must be perfectly smooth and even.
They must be evenly thick and have no bulges
that can cause dents or instant breakage
when sliding between the blade guide pads.
Decrease advance, exerting less cutting
pressure. Adjust the braking device if
mounted on the machine.
Change speed and/or type of blade.
See chapter on “Material classification and
blade selection”, in the section
Blade selec-
tion table according to cutting and feed
speed.
Choose a suitable blade. See Chapter “Ma-
terial classification and blade selection”.
Check the gripping of the part.
At the beginning of the cutting process,
never lower the saw frame before starting
the blade motor.
PREMATURE BLADE WEAR
Faulty running-in of blade
Teeth positioned in the direction oppo-
site the cutting direction
Poor quality blade
Too fast advance
Wrong cutting speed
Defects on the material or material too
hard
Insufficient lubricating refrigerant or
wrong emulsion
Faulty welding of blade
Too fast advance
Wrong cutting speed
Wrong tooth pitch
Ineffective gripping of the part in the vice
Blade touching material at beginning of
cut
BLADE BREAKAGE