Service instructions – AMETEK 1500 Induction Style Relay User Manual
Page 5
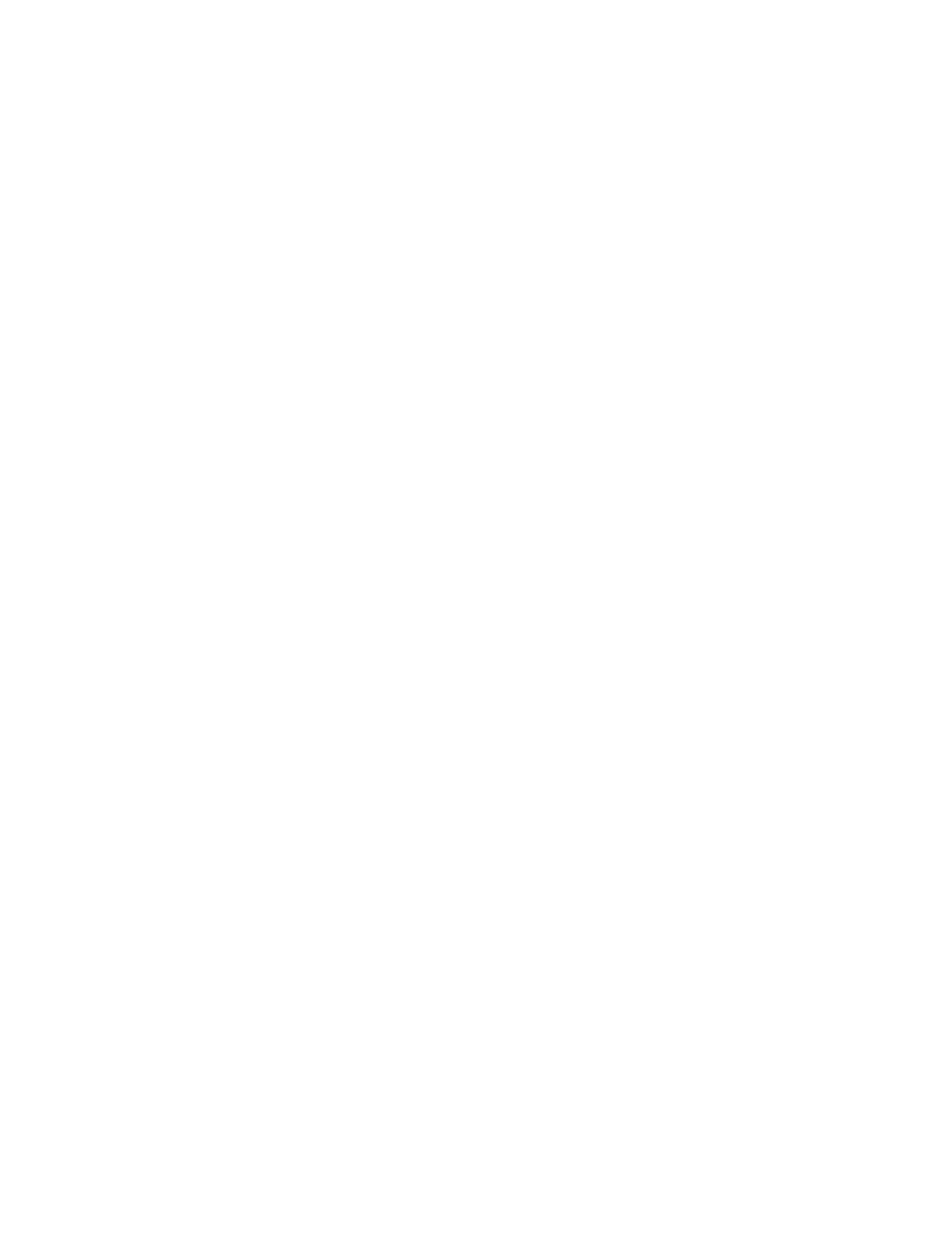
5
Service Instructions
CAUTION
Be sure to disconnect relay control
power before servicing electrodes
or electrode holders.
B/W relays are designed and built to require a minimum of service in the fi eld.
Each one is tested and adjusted at the factory to insure positive operation and
should not be altered or tampered with prior to installation. If a relay does not
operate properly after it has been installed, the following information will be
helpful in determining the probable cause.
A. Relay Will Not Pull In
If relay will not pull in when liquid contacts upper electrode, failure to operate
is probably caused by one of the following conditions:
1. Power Failure - A power failure to relay can be caused by broken wire,
blown fuse, an open switch, loose screw, corroded connection, etc. Check for
power failure with voltmeter or test light directly on relay line terminals (No.3
and 4 on all B/W relays). Also check voltage at motor starter line terminals
and overload heaters on motor starter to be sure they have not tripped.
2. Open Coils - Coils used in B/W relays very rarely fail unless struck by
lightning or subjected to some severe over-voltage condition. To check coils,
disconnect electrode connections from relay terminals, apply line voltage to
the primary coil, and touch both ends of secondary coil with an insulated
jumper wire. Relay should pull in when the jumper is connected and fall out
when the jumper is removed. Failure to do so indicates that one of the coils is
open. If an open coil is found, contact dealer or the factory for a replacement
relay.
3. Poor Ground Connections - B/W induction relays that operate from a
single electrode i.e., Types 1500-A, C, B, E and D will not function unless
a good dependable ground connection is made to complete the secondary
circuit from one end of the secondary coil through the electrode and liquid,
and back through ground to the other side of the secondary coil. If such a relay
does not operate when liquid contacts the electrode, check ground connection
to be sure it complies with installation instructions.
4. Broken Wires - A broken wire from relay to either electrode will prevent
relay from operating. Broken wires can be checked by shorting the upper and
lower electrode leads together at the electrode holder. If relay fails to pull in,
one or both of the electrode leads is open. The individual leads can then be
checked by running a temporary wire from the relay to holder outside conduit.
If relay pulls in, it may be assumed that break is between the holder and the
electrodes. This can be checked by shorting between the electrode tips with
an insulated jumper.
5. Low Secondary Voltage - If the secondary coil voltage is too low for the
resistance or conductivity of the liquid being controlled, the relay will not pull
in - or it will buzz and chatter before pulling in. In either case, the relay should
be replaced with one which has a higher voltage secondary coil. (See Table.)
If in doubt about proper coil selection, furnish factory with details on liquid - or
send sample for test.
6. Fouled Electrodes - Accumulation of dirt, grease or other deposits on
the upper electrode will insulate it and prevent relay from pulling in. If this
occurs, the electrodes should be inspected and cleaned at regular intervals
as required to eliminate the diffi culty. If unusual quantities of oil, grease, or
sludge and encountered, the electrodes can be mounted inside a pipe that is
fl ushed with clean water. A 4” pipe should be used - with the bottom located
below the lowest water level, and vent holes provided at top so that the level
inside and outside the pipe will be the same. A small fl ow of water entering the
top of the pipe will cause an outward fl ow of water from the bottom of the pipe
and prevent undesirable material from entering. Thus, the electrodes have a
clear surface on which to operate and will stay clean.
7. Electrodes Too Short - It is possible for an installation to be completed
in which the upper electrode is suspended at a point where the liquid cannot
make contact. All installations should, of course, be checked to make sure
that proper electrode lengths are provided.
B. Noisy Relay Operation
If the relay functions properly but is noisy in operation, it could be caused by
the following:
1. Poor Electrode Connections - If wire suspended electrodes are used
and have either been lost or not properly connected resultant increase
in resistance is secondary circuit may cause relay to buzz or chatter in
operation. This condition can be corrected by checking to see that proper
electrode connections are made. Excessive accumulation of dirt, grease or
other deposits on the electrodes can also result in noisy relay operation - in
which case periodic cleaning will eliminate the problem.
2. Low Secondary Voltage - If resistance of the liquid being controlled is
at the upper end of the sensitivity range of the relay secondary coil, noisy
operation may result. Sensitivity may be increased slightly by interchanging
the ground and lower electrode connections at the relay. If this does not
correct the condition, the relay should be replaced with one having a higher
voltage secondary coil.
C. One Level Operation
If a relay operates at one level only - starting and stopping at one electrode,
check the following:
1. Electrode Wires - If wires between relay and electrodes are interchanged,
relay will not operate over range in level but from upper electrode only. To
correct, simply reverse connections - either at relay or at electrodes.
2. Ground Connection - Poor ground connection will prevent holding circuit
from functioning and cause relay to operate from the upper electrode only.
This can be easily corrected by making sure that ground connections conform
with Installation Instructions.
3. Holding Circuit - If the holding circuit is not closing, the relay will operate
from the upper electrode only. Since the holding circuit contact carries only
a small current, a slight fi lm of grease or dirt can sometimes prevent proper
closure. To correct, rub contact surface with a clean paper. Do not use sand
paper or emery cloth.
4. Upper Electrode Lead - A ground in lead wire to the upper electrode
will cause relay to operate from lower electrode only. This condition can be
checked out as described below.
D. Relay Will Not Drop Out
If relay will not drop out when liquid falls below lower electrode, check the
following points:
1. Lower Electrode Lead - A ground in the lead wire from relay to lower
electrode will prevent relay from dropping out on low liquid level. If distance
from holder to relay is relatively short, the best way to check for a ground is
to connect a replacement wire from relay to the electrode holder outside the
conduit and test the relay for operation. If it drops out properly it is safe to
assume that a ground exists in the original lower electrode lead wire.
If relay is located a considerable distance from electrode holder, check for
ground as follows: Disconnect power to relay. Remove wires from terminals
in electrode holder and allow them to stick up to eliminate possibility of
contacting a grounded part. Then turn on power to relay. If relay pulls in,
a short is indicated between the electrode leads, from both electrodes to
ground, or secondary coil is shorted internally. If relay does not pull in, short
secondary coil with piece of insulated wire by bridging between relay terminal
connections for upper and lower electrodes. Relay should pull in when this
connection is made and drop out when connection is broken. If relay does not
drop out, a short to ground is indicated in lower electrode lead. This ground
may not be enough to pull in relay, but it can be suffi cient to hold relay in once
it has been closed in normal operation.
If any of these conditions exist, disconnect power to relay and replace
grounded wires.
2. Electrode Holder - Excessive dirt or moisture over insulation at electrode
holder or electrodes can cause faulty relay operation. Interior of electrode
holder and its underside should be kept clean and dry. Conduit connections
should be made so that no condensation can enter holder. Underside of
vertically mounted holders should never come in contact with the liquid.
Insulated rod electrodes should be used with horizontally mounted holders.
Electrodes should be kept relatively clean and free of dirt or grease. Check
them periodically to make sure they do not become fouled with fl oating debris
or insulating deposits.
3. Length of Lead Wires - On installations with excessive distance - over 900
feet - between relay and tank, relay may tend to hold in due to capacitance in
electrode lines and fail to drop out when liquid leaves lower electrode. Since
there are a number of ways to achieve reliable long distance control, complete
information regarding such applications should be submitted to factory for
recommendations.