Eliminating vibration with damped boring bars – Sandvik Coromant Silent tools - How to reduce vibration in metal cutting User Manual
Page 27
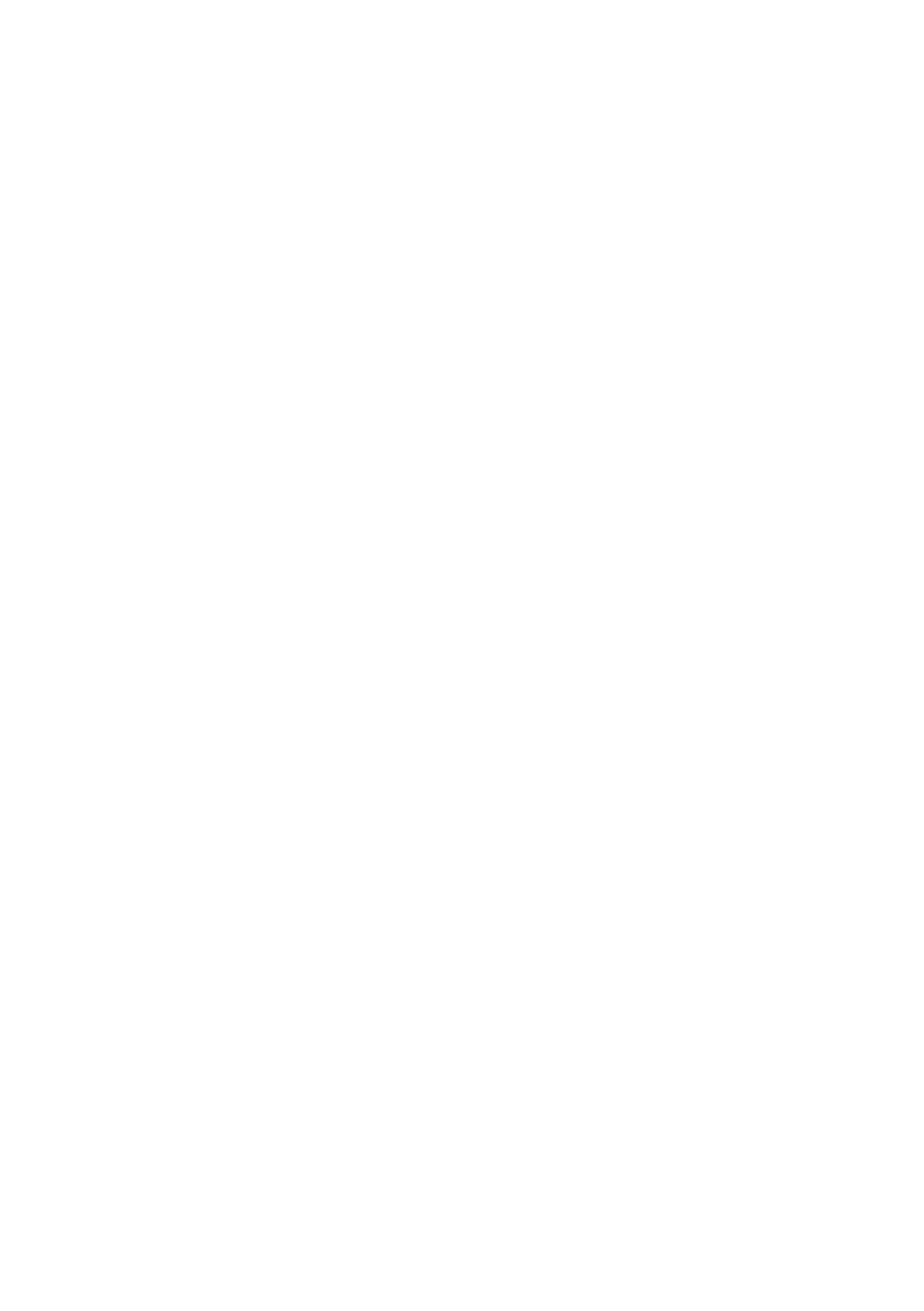
Sandvik Coromant – How to reduce vibration in metal cutting
23
Eliminating vibration
with damped boring bars
The usual cause of vibrations during machining is the dynamic interaction
between the cutting process and the machine tool structure. The source is
the variation of cutting force generated between the tool and workpiece.
This force strains the structure elastically and can cause a deflection of the
tool and workpiece, which alters the tool-work engagement. A disturbance
in the cutting process, such as a hard spot in the work material, causes a
typical deflection which then alters the cutting force. This may then cause
the initial vibration to be self-sustaining and to build up with the machine
oscillating in one of its natural modes of vibration. A long boring bar over-
hang can be a weak link in the set-up involving machine tool, – tool, – work-
piece and the source of vibration.
In order to achieve sufficient process stability, the metal removal rate is
often reduced or the cutting tool changed. But as productivity is normally a
priority in manufacturing, this is the wrong route to go. Instead the means
of eliminating vibrations and being able to machine at higher rates should
be examined. The use of damped boring bars, with damping elements in-
tegrated in the boring bars, improves the dynamic behaviour of the tools,
making the process more stable.
Generally, machining up to four times the diameter of boring bars does
not cause any problems from the vibration point of view, provided that
correct conditions apply as regards cutting data and inserts. With an over-
hang of more than 4 times the tool diameter, vibration tendencies can be-
come more apparent and damped bars come into the picture as the solution.
With a pre-tuned boring bar, machining of holes with a depth of up to 14
times the diameter of the bar can be performed with good results.
An increased length from 4 to 10 times the bar diameter will give a 16
times larger deflection for a bar being subjected to the same cutting force.
A further extension from 10 to 12 times the bar diameter, gives another
70 % increase in deflection from the same cutting force. Holding the bar
length constant while changing the bar diameter from 25 to 32 mm, reduces
deflection by 62% for equal cutting forces. Reduced weight of cutting units