Dwyer instruments, inc – Dwyer MMA User Manual
Page 2
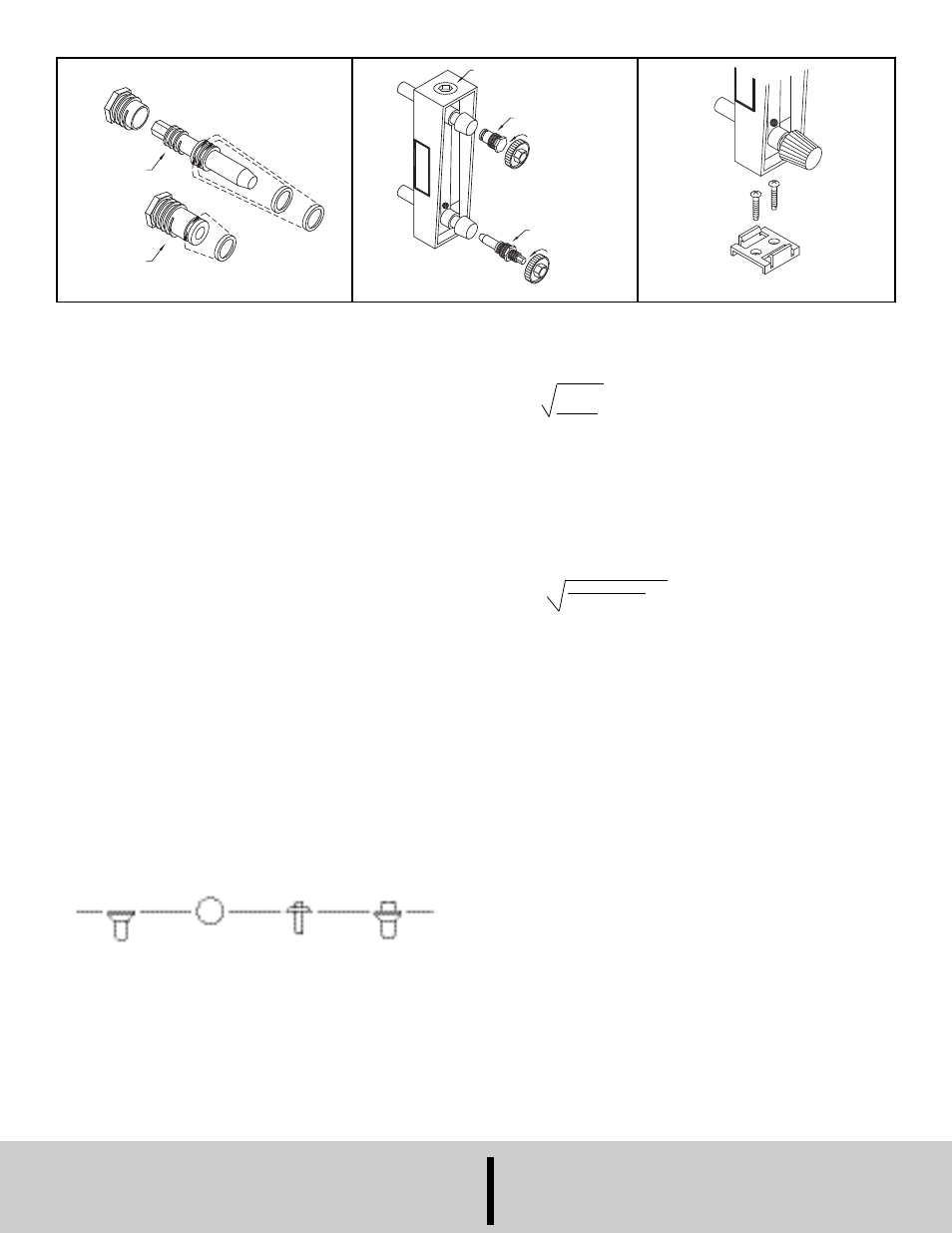
INSTALLATION AND MOUNTING
(Flowmeter must be installed in vertical position)
PANEL MOUNTING - Drill two 11/32˝ diameter holes on 3˝ centers on a vertical
line. Insert flowmeter from front and push on spring retainer clips from rear, pliers
may be necessary.
SURFACE MOUNTING - Attach plastic mounting clip to a horizontal surface using
#4 Phillips head B-type self-tapping screws provided. See figure C. Clip will bow
downward slightly when properly tightened. Snap flowmeter into clip. Be sure
flowmeter is vertical after mounting.
CONNECTIONS
CAUTION: Select tubing rating higher than supply pressure to flowmeter.
25 PSI MAXIMUM. Use 1/4˝ ID x 3/8˝ OD plastic tubing. Slip tubing onto
connections a minimum of 3/8˝.
50 PSI MAXIMUM. Use 1/4˝ ID x 3/8˝ OD plastic tubing. Slip tubing onto
connections a minimum of 3/8˝. Use pliers to expand spring type tubing clamps and
install on both connections.
100 PSI MAXIMUM. Use suitable 5/16˝ compression union with metal or semi-rigid
plastic tubing.
OPERATION
Once all connections are complete, introduce flow as slowly as possible to avoid
possible damage due to shock. With liquids, make sure all air has been purged
before taking readings.
The performance of low range units used in air or gas applications may be affected
by static electricity. Excessive static charge may cause the ball float to behave
erratically or provide a false reading. To ensure the proper function of the unit, the
application should be designed to minimize or dispel static electricity.
The standard technique for reading a Variable Area Flowmeter is to locate the
highest point of greatest diameter on the float, and then align that with the
theoretical center of the scale graduation. In the event that the float is not aligned
with a grad, an extrapolation of the float location must be made by the operator as
to its location between the two closest grads. The following are some sample floats
shown with reference to the proper location to read the float.
Variable Area Flowmeters used for gases are typically labeled with the prefix “S” or
“N”, which represents “Standard” for English units or “Normal” for metric units. Use
of this prefix designates that the flowmeter is calibrated to operate at a specific set
of conditions, and deviation from those standard conditions will require correction
for the calibration to be valid. In practice, the reading taken from the flowmeter
scale must be corrected back to standard conditions to be used with the scale units.
The correct location to measure the actual pressure and temperature is at the exit
of the flowmeter, except under vacuum applications where they should be
measured at the flowmeter inlet. The equation to correct for nonstandard operating
conditions is as follows:
Q
2
= Q
1
x P
1
x T
2
P
2
x T
1
Where:
Q
1
= Actual or Observed Flowmeter Reading
Q
2
= Standard Flow Corrected for Pressure and Temperature
P
1
= Actual Pressure (14.7 psia + Gage Pressure)
P
2
= Standard Pressure (14.7 psia, which is 0 psig)
T
1
= Actual Temperature (460 R + Temp °F)
T
2
= Standard Temperature (530 R, which is 70°F)
Example: A flowmeter with a scale of 10-100 SCFH Air. The float is sitting at the 60
grad on the flowmeter scale. Actual Pressure is measured at the exit of the meter
as 5 psig. Actual Temperature is measured at the exit of the meter as 85°F.
Q
2
= 60.0 x (14.7 + 5) x 530
14.7 x (460 + 85)
Q
2
= 68.5 SCFH Air
MAINTENANCE
The only maintenance normally required is occasional cleaning to assure proper
operation and good float visibility.
DISASSEMBLY: Use the circular black installation tool to remove valve (when
used) and plugs. Fittings on front turned CLOCKWISE to remove and top plug is
turned COUNTER-CLOCKWISE. Take care to prevent loss of float.
CLEANING: The flowmeter body and other parts can be washed in a mild soap and
water solution. A cotton swab or soft bristle brush will help when cleaning flow tube.
Avoid solvents and liquid soaps and avoid prolonged immersion.
RE-ASSEMBLY: Coat “O” rings and valve stem threads with silicone stop cock
grease or petroleum jelly. Check “O” rings after assembly to make sure they are
properly seated.
ADDITIONAL INFORMATION
For additional flowmeter information, conversion curves, correction factors and
other details on the entire line of Dwyer
®
flowmeters, please request a Dwyer
Instruments, Inc. full-line catalog.
VALVE STEM
PLUG
TOP PLUG
PLUG
VALVE ASSEMBLY
DWYER INSTRUMENTS, INC.
Phone: 219/879-8000
www.dwyer-inst.com
P.O. BOX 373 • MICHIGAN CITY, IN 46360, U.S.A.
Fax: 219/872-9057
e-mail: [email protected]
Fig. A
Fig. B
Fig. C
Mating Plug
Turn valve assembly and
plug assembly counter-
clockwise to install.
©Copyright 2012 Dwyer Instruments, Inc.
Printed in U.S.A. 4/12
FR# 59-440474-00 Rev. 8