5electrical connection, 6 diagnosis, 1 interconnection of devices in the hazardous area – KROHNE UFC 030 PROFIBUS PA User Manual
Page 8: 2 bus cable, 3 shielding and grounding
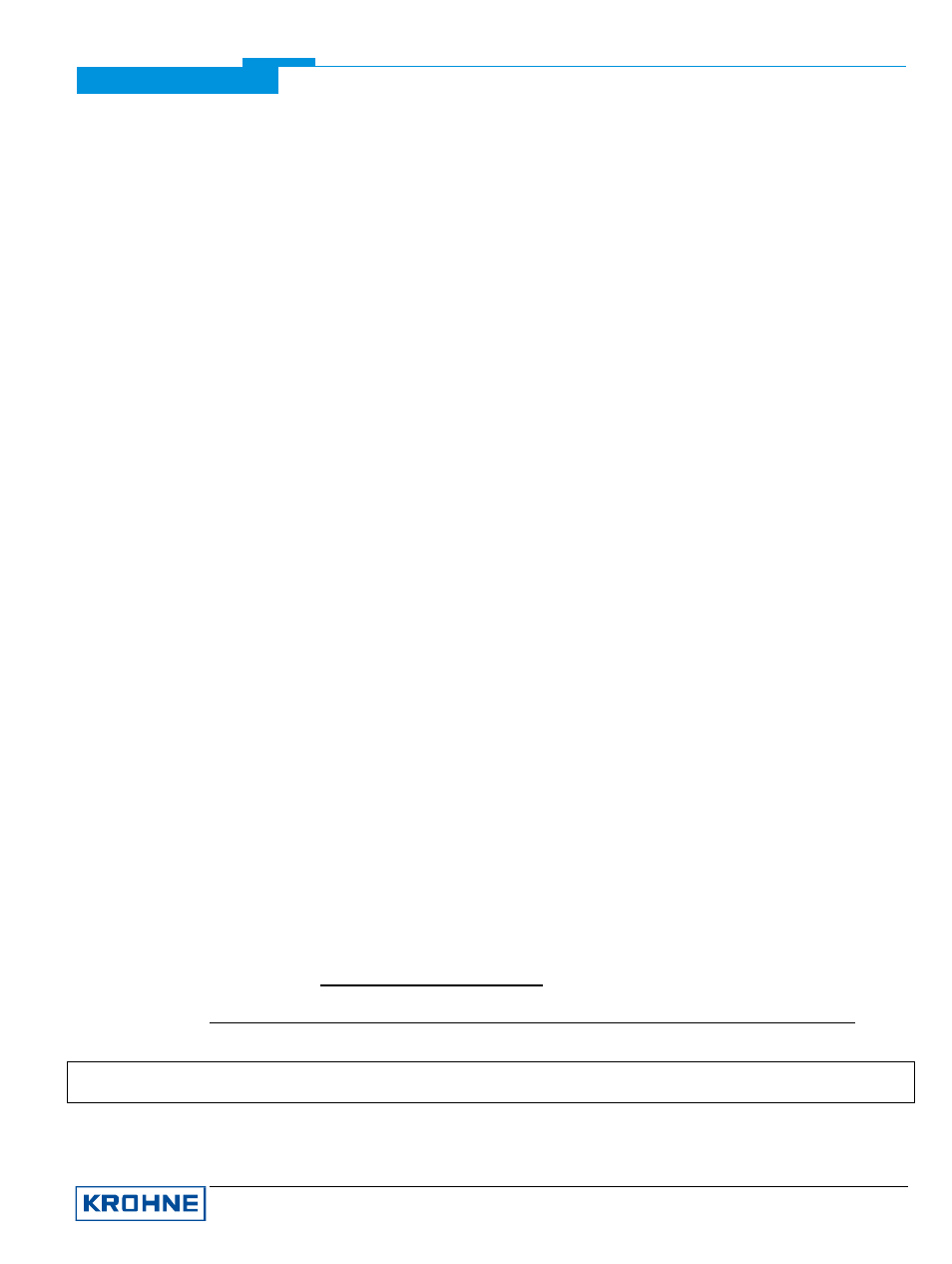
Supplementary documentation UFC030 with PROFIBUS-PA
KROHNE Messtechnik GmbH & Co. KG · Ludwig-Krohne-Str. 5
D-47058 Duisburg
8/17
Tel.: 0203-301 309
Fax: 0203-301389 · e-mail: [email protected]
The „Quality-Substatus“- and „Limit“-Bits will be used for further diagnostics or limit checking.
Attention:
The status should be watched always because a valid number will be transmitted even if the status of
the measurement value is bad or uncertain. This is the only way to check the meaning of the
transmitted measurement values.
4.6 Diagnosis
If the device internal diagnostic functions will detect an error additional information will be send to the Master (for
further information have a look at the UNIT_DIAG_BIT(i) definitions of the corresponding GSD-file)
5
Electrical Connection
For a detailed description please check the Installation and Operating Instructions manual of the device.
5.1 Interconnection of devices in the hazardous area
A PROFIBUS-PA network in the hazardous area should be projected in accordance with actual regulations:
•
all electrical components which should be connected to the bus must be approved according the hazardous area
regulations,
•
the approved input values of the field devices (Uo, Io, Po) must match with the output values of the power supply
(e.g. segment coupler) which means U
i
≤
Uo,
I
i
≤
I
o and P
i
≤
Po.
•
the maximum length of each trunk cable does not exceed 1000 m,
•
the maximum length of each spur cable does not exceed 30 m,
•
the values of the cable are within the following ranges R´=15...150
Ω
/km; L´=0,4...1mH/km; C´=80...200nF/km,
5.2 Bus cable
Cable length between any devices should be less then 1900 m. Further limitations to the cable than the hazardous
area limitations are not existent. Nevertheless a twisted pair and overall shielded cable is strongly recommended. A
good quality cable could have the following data (Type A):
impedance at 31.25 kHz
100
Ω
±20 %
DC resistance (per conductor)
22
Ω
/km
capacity unbalanced
< 2 nF/km
attenuation at 39 kHz
< 3,0 dB
5.3 Shielding and grounding
For an optimum electromagnetic compatibility of systems it is extremely important that the system
components and particularly the bus cables connecting the components be shielded. This shields should be
connected in a way that they will look like “one non interrupted, unbroken shield” (if possible).
Hence it follows that, for use in non-hazardous duty systems , the cable shield should be grounded as often
as possible.
In “Ex“ systems with adequate equipotential bonding in the hazardous and non-hazardous location along
the entire fieldbus installation, multiple grounding of the shield is also of advantage.
Note: The use of twisted and shielded cables is strongly recommended, otherwise EMC protection of the
ultrasonic flow meter cannot be assured.