KROHNE DA Flap-type EN User Manual
Page 16
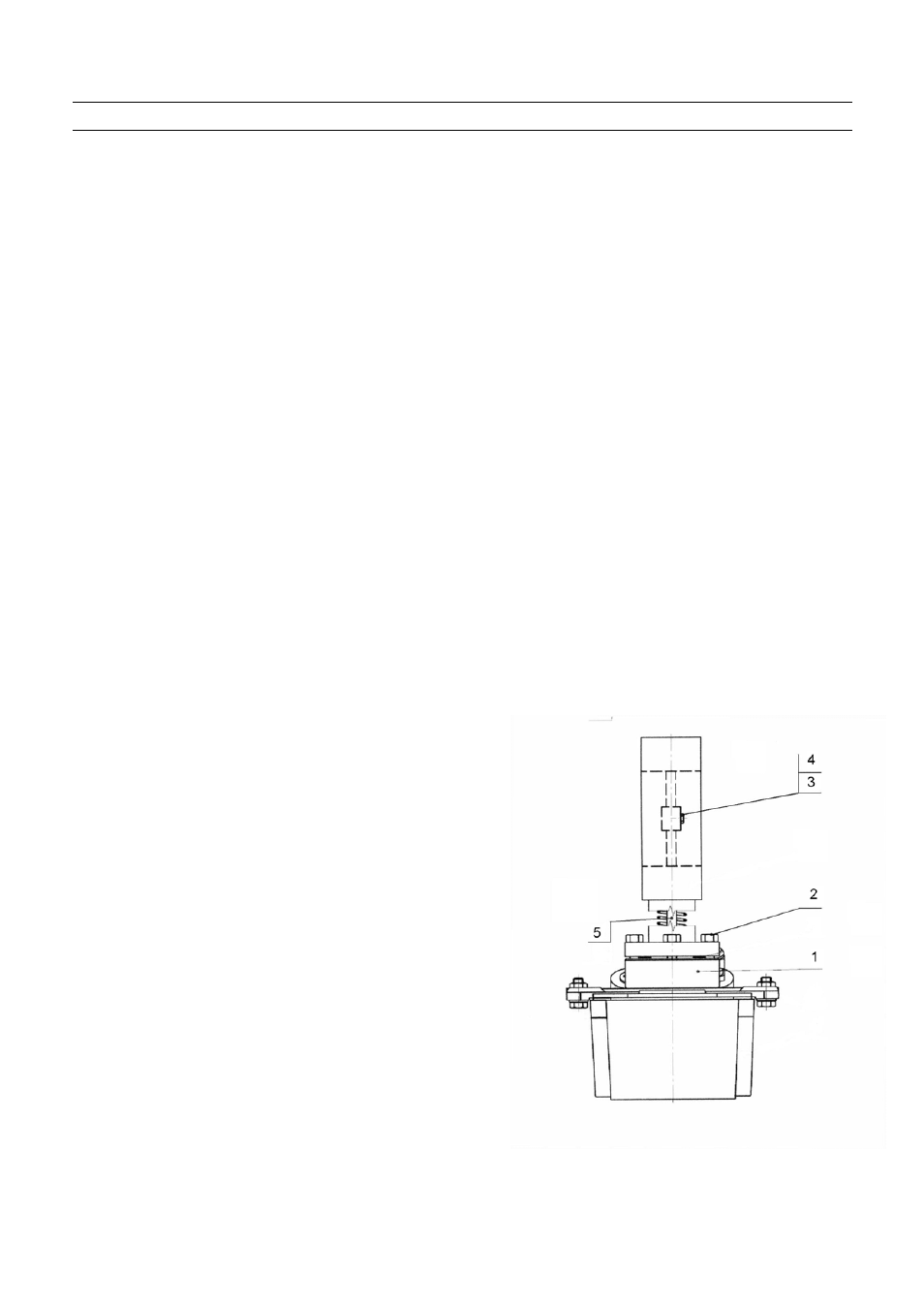
10 Maintenance
The flowmeter is also to be inspected for soiling, corrosive erosion and mechanical wear or damage to the measuring
tube and the display in the context of the routine operational maintenance of the installation and the pipelines. We
recommend at least annual inspections. In order to clean the instrument remove it from the pipeline.
Note
Pressurized lines have to be relieved before the measuring unit is removed.
Corresponding safety precautions with regard to residual liquids in the measuring unit in case of instruments which are
used to measure aggressive media.
New seals must always be used when remounting the measuring unit in the pipeline.
Electrostatic charges are to be avoided when the surfaces (e.g. viewing window) are cleaned!
Maintenance
The device is normally maintenance-free. Should it become soiled, it will need
to be removed from the pipeline for cleaning. Devices fitted with contacts
must be disconnected from supply and de-energized.
To dismantle the device you will need the following tools:
2x open-jawed spanner, jaw span 13mm
1x open-jawed spanner, jaw span 7mm
1x screwdriver 4x 0.6mm
1x socket spanner, size 7mm up to DN 100 or
1x socket spanner, size 8mm, up to DN 250 or
1x socket spanner, size 10mm, for DN 300 and higher.
Required spares: 2x gasket
If necessary, wear personal protective gear (safety goggles,
protective gloves, conductive footwear).
Depressurize the pipe.
Caution: Slacken screws/bolts only when the system has been de-
energized, the pipe depressurized and free of fluid product.
Drain the pipes.
Remove the device from the pipeline in the reverse order
Detach the dial gauge with magnet casing from the neck of the
device by removing the four M8 screws (Item 1 or 2).
Unscrew the fastening screws (3) between spindle and flap (4).
Pull the spindle together with the magnet casing and the spring
assembly (5) out of the device.
Clean all mechanical parts with appropriate cleaning agents. If
necessary, clean the indicator part with a damp cloth that has been
rinsed in soap suds and wrung out.
Reassemble in the reverse order, paying special attention to the
position of the flap. The bearing marked with a centre punch must
point towards the spring. Do not change the original orientation of
the flap (maintaining the direction of rotation appropriate to the
indicator part ). The flap requires a minimum of 1 mm clearance on
both sides (risk of jamming and sparking).
Hazardous areas: Do not on any account remove the labelling on
the scale casing containing information on explosion protection.