Dismantling & assembly instruction, Safety rules for a screwdriver, Reassembly – Universal Air Tools UT5964A User Manual
Page 2
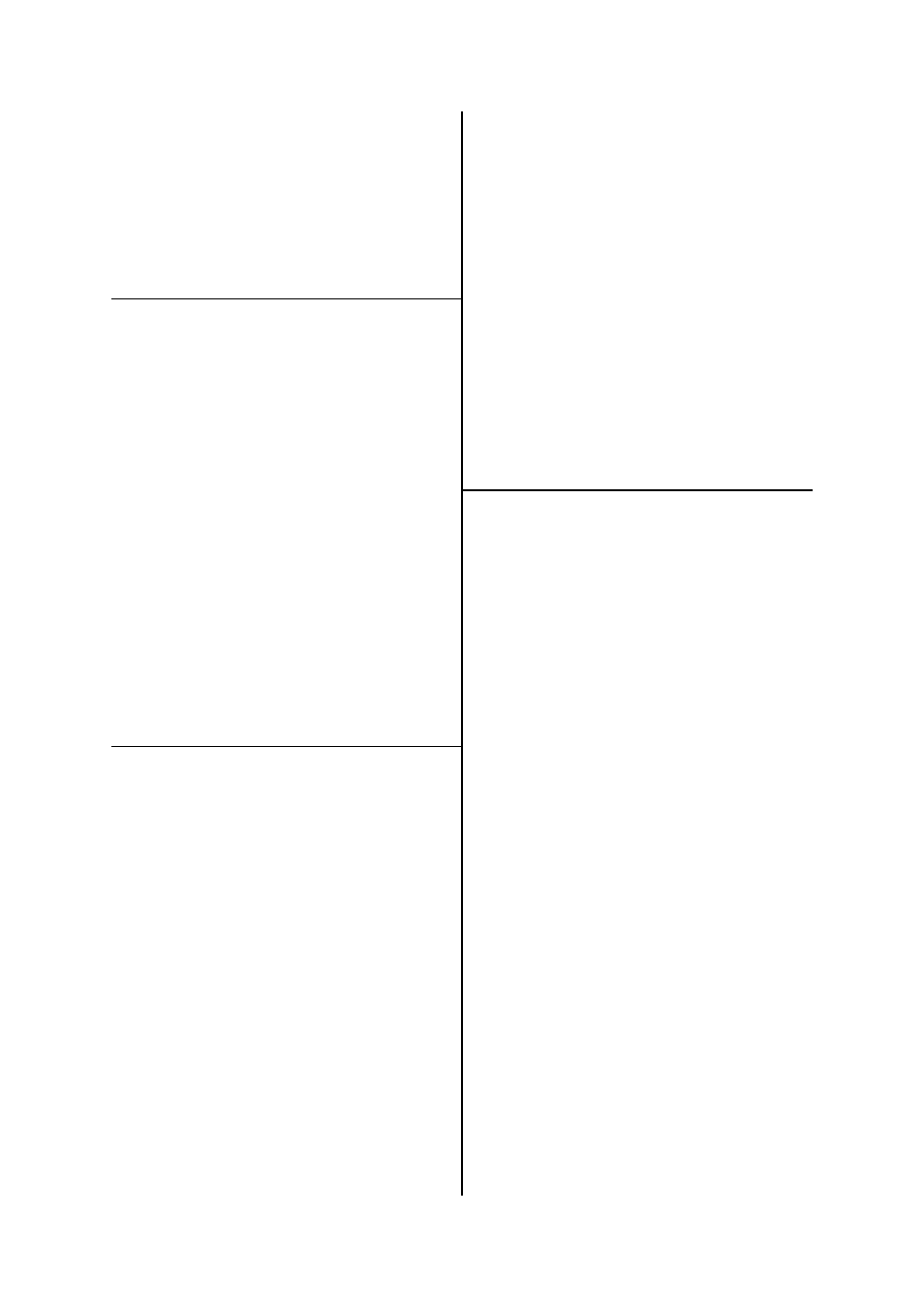
Operating
Select the correct screwdriver bit or fastener driver to suit the
screw or fastener to be tightened or loosened. Slide back the
sleeve (44) and insert appropriate drive bit. This model has
an external adjustable clutch so that the torque applied to the
fastener can be adjusted easily to give the required tightness
within the torque range of the tool. To set the tool to give a
particular torque output, turn the adjust ring (49) If the fastener
is not sufficiently tightened or cannot be loosened then the
tool in adjustable clutch mode has insufficient capacity. Select
a more powerful tool. The person setting up the tool must
be aware of this torque reaction at high setting levels of the
clutch and that the tool will try to turn against the hand. All
that is required is a firm grip. The tool, when the stall torque
position has been reached, can still be used to set or loosen
fasteners, provided the operator is aware of the need to resist
the torque reaction of the tool. The only thing that will affect
the output is a change in the air supply pressure. The output
can be increased up to the use of the maximum allowed
supply pressure and decreased with a reduction in supply
pressure until the tool fails to operate. It must also be
understood that even if the clutch is set to slip it may not do
so if the supply air pressure falls below the pressure at which
the clutch was set. It is therefore strongly recommended that
a pressure control valve is used. Information as to suitable
equipment can be obtained from your supplier. When using
the tool keep the screwdriver bit pressed firmly into the screw
head to avoid cam out and screw head damage.
Dismantling & Assembly Instruction
Disconnect tool from air supply.
Grip the tool by hand then unscrew and remove clutch
housing (7) from clamp nut (41) – left hand thread.
Remove adjust cover (47) from clutch housing (7). Pull out
the clutch assembly grip the clutch assembly and with a
sharp pointed needle tool prise out retaining ring (31) and
remove washer (46), spring (45), and ball retainer (44)
being careful not lose screwdriver bit retaining ball (35).
Again with the sharp pointed tool, remove second retaining
ring (31) and pull off spacer (43). Unscrew adjust nut (47)
and pull off washer (46), clutch spring (39) and washer
(38). Tap front end to remove 4 off balls (37). Remove
retaining ring (33) and separate clutch (36). Remove a third
retaining ring (31) and pull off drive clutch (30). Unscrew
clamp nut (41) and push out the internal assembly and
ball bearing(29), internal gear (32), 3 off planet gears (25)
and work spindle (28). Do not remove the 3 off pins from
work spindle (27). Drive out pin (6), unscrew set screw
(23) and pull off trigger (24) and remove spring (22). Grip
valve stem (21) and pull out the complete valve assembly.
Separate reverse lever (20), reverse retainer (19), o-ring
(18), reverse bushing (17) and o-ring (16). Unscrew air
inlet (2) and screw (3) and remove exhaust diffuser (4) and
damping material (5). Grip end of rotor (13) and pull out
the complete motor assembly. Remove 2 pins (11), motor
gasket (9) Grip spacer (15) and with a non metallic or soft
metal (lead of aluminium) hammer tap the splined end of
the rotor (13) to drive it through bearing (8). Remove
cylinder (12) and take out 5 off rotor blades (14) from the
rotor (12). Support end plate (10) and tap the rotor (13)
through the end plate (10) and bearing (8).
Reassembly
Clean all component parts and examine to wear before
reassembling. Look in particular for wear and cuts on o-rings,
wear on rotor blades, gear, and clutch components. Coat
all parts with pneumatic tool lubricating oil and grease all
bearings, gears, and clutch parts with a molybdenum or
lithium based general purpose grease. Before reassembling
the motor make sure that the faces of end plates (10) that
abut cylinder (12) are flat and free from burrs. If necessary,
lap on a flat very fine grade of abrasive paper. Reassemble
in the reverse order. When refitting the complete motor
assembly to housing (7) first make sure that the assembly
is clamped tightly together and the rotor spins freely, slide
the assembly with gasket into the housing (7) ensuring that
motor pin (11) locates in the motor assembly and in the
hole in the bottom of the main bore of housing (7) suited
between the two main ports. Reset the clutch as required
and/ or set the correct air pressure – see Operating.
trigger on the tool. Disconnect the air line and pour into the
intake bushing a teaspoonful (5ml) of a suitable pneumatic
motor lubricating oil preferably incorporating a rust inhibitor.
Reconnect tool to air supply and run tool slowly for a few
seconds to allow air to circulate the oil. If tool is used
frequently lubricate on daily basis and if tool starts to slow
or lose power.
It is recommended that the air pressure at the tool whilst
the tool is running is 90 p.s.i./6.3 bar. The tool can run at
lower and higher pressures with the maximum permitted
working air pressure of 100 p.s.i./7.0 bar.
Page No 2
Safety Rules For A Screwdriver
1) Read all the instructions before using this tool. All operators
must be fully trained in its use and aware of these safety
rules.
2) Do not exceed the maximum working air pressure.
3) Use personal safety equipment.
4) Use only compressed air at the recommended conditions.
5) If the tool appears to malfunction remove from use
immediately and arrange for service and repair.
6) If the tool is used with a balancer or other support device
ensure that it is fixed securely.
7) Always keep hands away from the working attachment
fitted to the tool.
8) The tool is not electrically insulated. Never use the tool
if there is any chance of it coming into contact with live
electricity.
9) Always when using the tool adopt a firm footing and/or
position and grip the tool firmly to be able to counteract
any forces or reaction forces that may be generated whilst
using the tool.
10) Use only correct spare parts. Do not improvise or make
temporary repairs.
11) Do not lock, tape, wire, etc. the on/off valve in the run
position. The trigger/lever etc. must always be free to return
to the 'off' position when it is released.
12) Always shut off the air supply to the tool, and depress
the trigger/lever etc. to exhaust air from the feed hose before
fitting, adjusting or removing the working attachment.
13) Check hose and fittings regularly for wear. Replace if
necessary. Do not carry the tool by its hose and ensure the
hand is remote from the on/off control when carrying the
tool with the air supply connected.
14) Take care against entanglement of moving parts of the
tool with clothing, ties, hair, cleaning rags, etc. This will
cause the body to be drawn towards the tool and can be
very dangerous.
15) It is expected that users will adopt safe working practices
and observe all relevant legal requirements when installing,
using or maintaining the tool.
16) Do not install the tool unless an easily accessible and
easily operable on/off valve is incorporated in the air supply.
17) Take care that the tool exhaust air does not cause a
problem or blows on another person.
18) Never lay a tool down unless the working attachment
has stopped moving.