Operation, Caution – Lincoln Electric IM698 PIPELINER 200G User Manual
Page 14
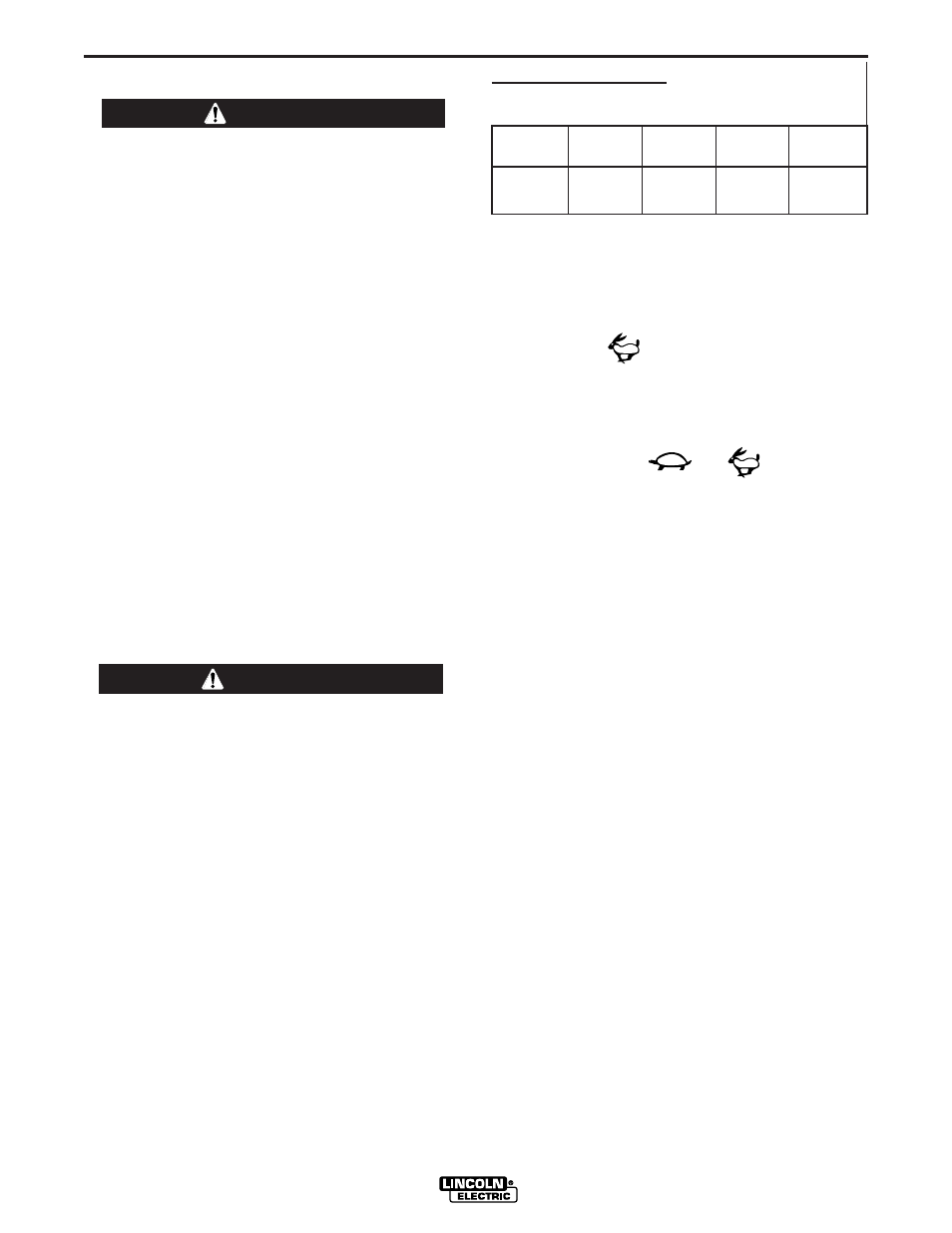
B-3
OPERATION
B-3
PIPELINER 200G
CONTROL OF WELDING CURRENT
DO NOT TURN THE “CURRENT RANGE SELEC-
TOR” WHILE WELDING because the current may
arc between the contacts and damage the switch.
------------------------------------------------------------------------
The “Current Range Selector” provides five overlap-
ping current ranges. The “Fine Current Adjustment”
adjusts the current from minimum to maximum within
each range. Open circuit voltage is also controlled by
the “Fine Current Adjustment” permitting control of the
arc characteristics.
A high open circuit voltage setting provides the soft
“buttering” arc with the best resistance to pop-outs
preferred for most welding. To get this characteristic,
set the “Current Range Selector” to the lowest setting
that still provides the current you need and set the
“Fine Current Adjustment” near maximum. For example: to
obtain 175 amps and a soft arc, set the “Current Range
Selector” to the 190-120 position and then adjust the “Fine
Current Adjustment” for 175 amps.
When a forceful “digging” arc is required, usually for
vertical and overhead welding, use a higher “Current
Range Selector” setting and lower open circuit volt-
age. For example: to obtain 175 amps and a forceful
arc, set the “Current Range Selector” to the 240-160
position and the “Fine Current Adjustment” setting to
get 175 amps.
DO NOT attempt to set the “Current Range Selector”
between the five points designated on the nameplate.
------------------------------------------------------------------------
These switches have a spring loaded cam which
almost eliminates the possibility of setting this switch
between the designated points.
TBI DEICING SYSTEM
The welder has been designed to allow continuous
year-round operation. Engine coolant is channeled
through the TBI housing to prevent the build up of ice
on the TBI throat around the throttle plate. the elec-
tronic controller is programmed to automatically com-
pensate for the build up of ice on the throttle plate.
There will be no noticeable change in the operation of
the welder should icing develop. On start-up, there is
a possibility for the engine to overspeed (to a maxi-
mum of 2000 RPM) for up to 10 seconds after throttle
body icing conditions have occurred. The electronic
governor will correct itself for the new operating condi-
tions and normal operation will resume.
IDLER OPERATION
The operating speeds are as follows:
The idler is controlled by the “Idler” toggle switch on
the welder control panel. The switch has two
positions as follows:
1. In the “High” position, the idler is off, and the
engine runs at the high speed controlled by the
governor. This speed can be adjusted between
1500 and 1600 RPM using the RPM dial on the
output rail.
2. In the “Automatic” / position, the
idler operates as follows:
• When welding or drawing power for lights or
tools (approximately 100-150 watts minimum)
from the receptacle, the engine operates at the
speed, set by the RPM dial.
• When welding ceases or the power load is
turned off, a preset time delay of 10 seconds
starts. This time delay cannot be adjusted.
• If the welding or power load is not re-started
before the end of the time delay, the idler reduces
the engine to low idle speed.
AUXILIARY POWER
1.75 kw of 120V DC auxiliary power is available at the
receptacle located on the control panel.
CAUTION
CAUTION
ORDERING
INFO.
ENGINE
FULL
LOAD
HIGH
IDLE
LOW
IDLE
K6090-7
GM 3.0L
1600-
1500
1600-
1500
1360