Operation – Lincoln Electric IM876 eCELL WIRE DRIVE SYSTEM User Manual
Page 20
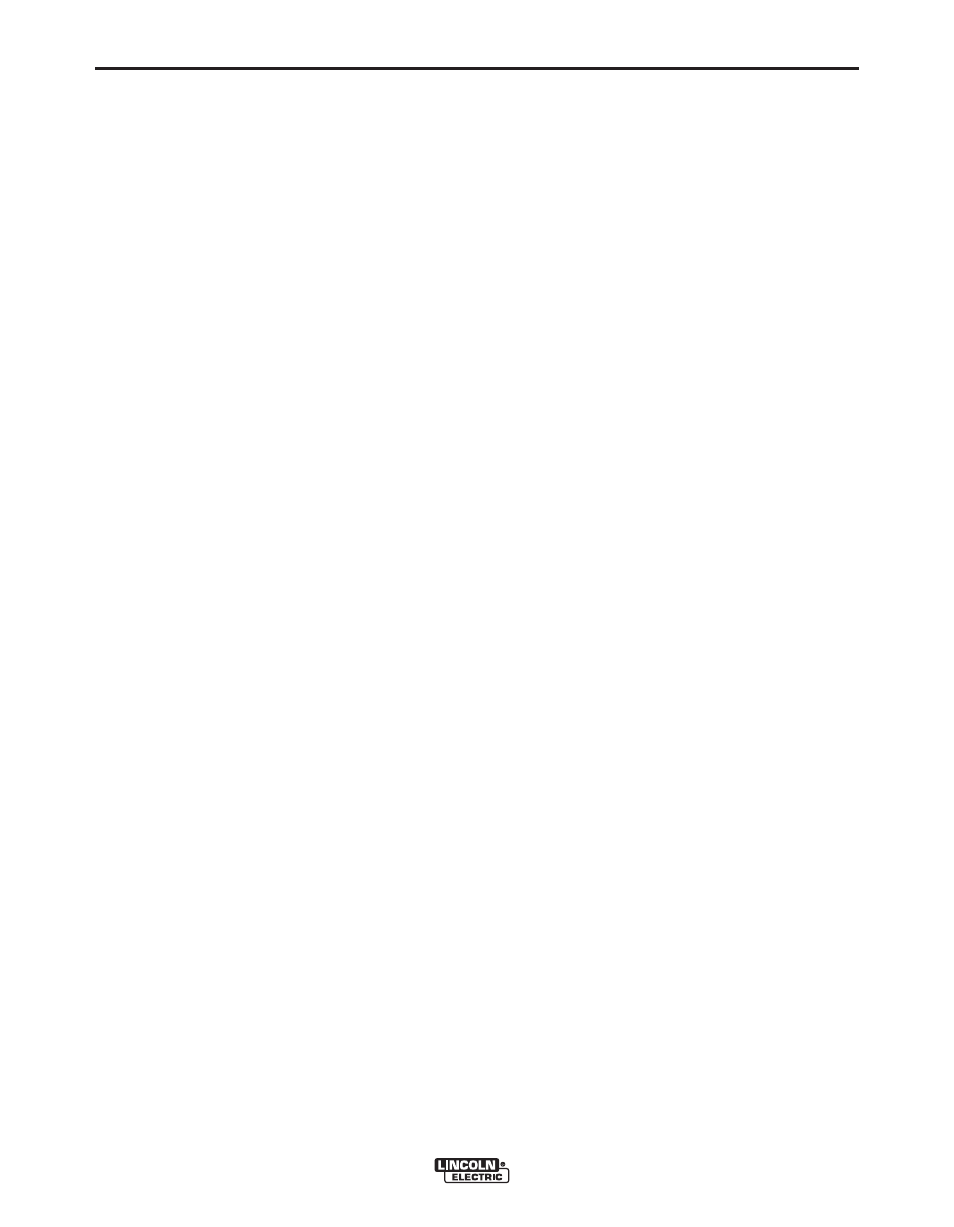
B-2
OPERATION
B-2
eCELL
™
WIRE DRIVE SYSTEM
RECOMMENDED PROCESSES
•
GMAW AND GMAW-STT
•
FCAW
PROCESS LIMITATIONS
• The eCell™ Wire Drive is not recommended for
GTAW, CAG, SMAW, SAW
• The eCell™ Wire Drive is not compatible with push-
pull equipment.
REQUIRED EQUIPMENT
All power sources must be part of the eCell™ system.
These include:
• PowerWave 355M
• PowerWave 455M
• PowerWave 455M/STT
• PowerWave 455M Robotic
• PowerWave 455M/STT Robotic
EQUIPMENT LIMITATIONS
• Maximum GMAW gun length =25’ (7.6m)
• Maximum conduit length = 25' (7.6m)
• Maximum total control cable length = 100ft (31m)
• The eCell™ Wire Drive works only with ArcLink
equipment.
• Other gun bushings are required for welding guns
that do not have a "Lincoln" back-end.
PRODUCT DESCRIPTION
General Physical Description
The eCell™ Wire Drive System is the wire feeder for
the eCell™. It consists of a 4 roll wire drive with con-
nections for the torch, electrode conduit and shielding
gas. The small, lightweight feeder mounts at the rear
of the eCell™.
General Functional Description
The eCell™ Wire Drive System is a robotic wire drive
that operates only with the eCell™. All welding para-
meters (WFS, voltage, etc.) are set through the robot-
ic controller. Integrated in the wire drive is a robotic
wire drive module. The eCell™ Wire Drive module
communicates with the robotic control and Power
Wave power source via ArcLink.
The wire drive is capable of wire feed speeds of 50 –
800 ipm. Accurate speed control is obtained with a
tachometer integrated in the motor. The wire drive is
capable of feeding both forward and reverse.
The heart of the eCell™ Wire Drive is the MaxTrac™
4 roll wire drive.
This new 4 roll drive MaxTrac™ technology delivers
great feeding because:
• Patent pending drive rolls improve traction.
• The precision machined, rigid aluminum
alloy frame results in maximum drive roll
clamping pressure.
• Drive hubs with steel inner cores have 3 ball
bearings inside each hub.
• The drive hubs are supported by large, heat
treated and ground shafts for maximum
rigidity and accurate drive roll alignment.
• Patent pending dual spring pressure arms
have sensitivity for feeding soft wires without
crushing them, and have plenty of compres-
sion force for feeding solid or stiff wires.
E a s y t o c o n f i g u r e , e a s y t o s e r v i c e p a r t s g i v e
MaxTrac™ drives the edge in productivity.
• Patented split wire guides fully support the
wire and virtually eliminate birdnesting.
• No tools required to change the drive rolls
and wire guides.
• Changeable gun bushings easily accept
guns from many manufacturers.
• Brass-to-brass connections between the
electrode connection and the gun minimize
voltage drop variations, resulting in consis-
tent arc performance all day, every day.
Functions that can be operated without the robot con-
troller are gas purge and cold feed.