I. introduction – MAHLE RTI BRC450 User Manual
Page 3
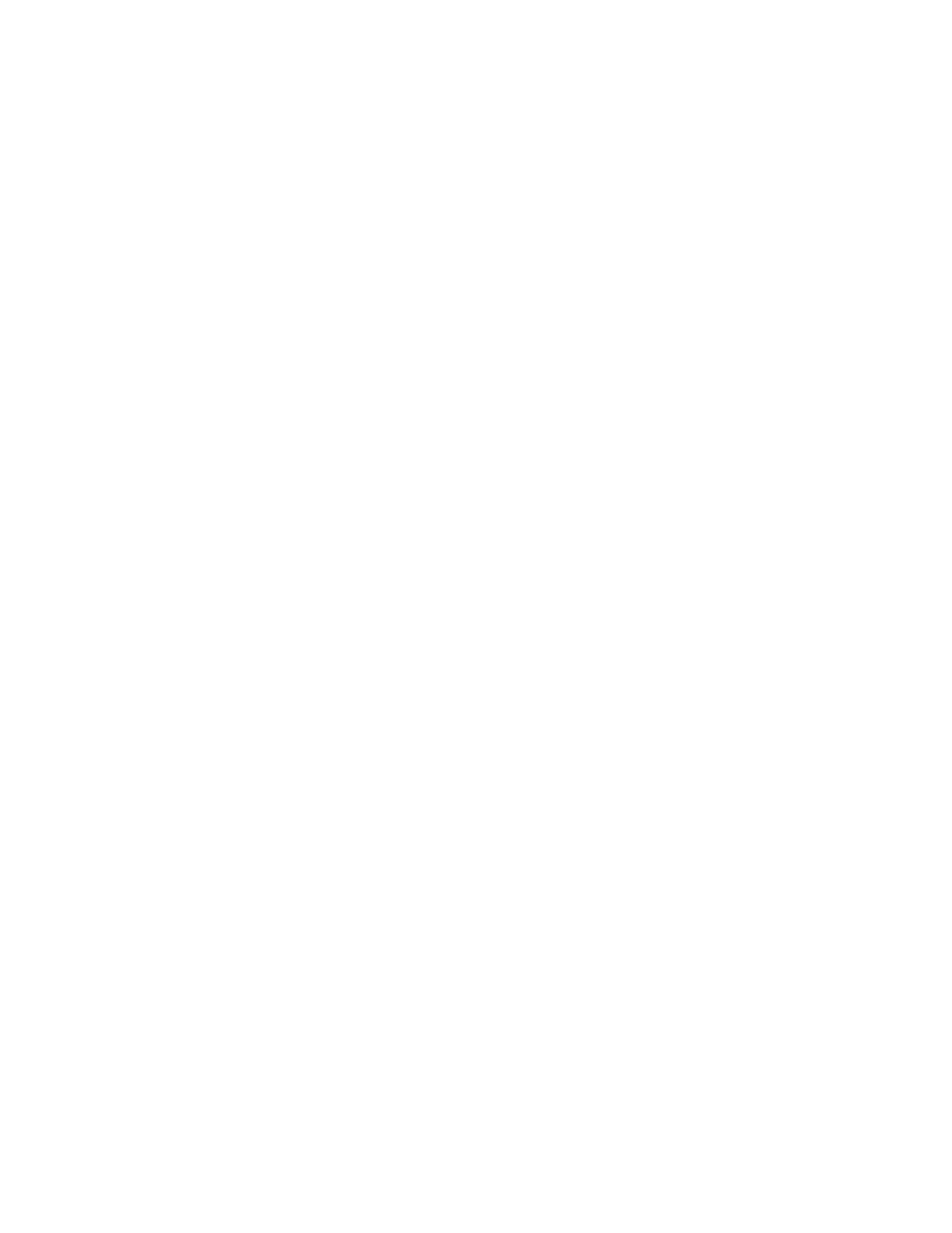
Page 1
I. Introduction
Thank you for your purchase of a BRC450 brake lathe. Congratulations on your choice! The BRC450
is designed to outperform every other comparable hub mounted brake lathe in all respects.
The BRC450 was designed as a completely new product. It is somewhat similar to a lathe supplied by
Hunter in the past, but the new BRC450 has many improvements and changes in design. The precision
machined components of the BRC450 are produced by RTI’s Worldwide partner and affiliate, Hunger
in Germany, using the most modern and sophisticated machine tools in the world. For more than 30
years, Hunger has been the leading automotive brake lathe manufacturer in Germany. The new
BRC450(E326a) is approved by Mercedes, GM, Chrysler and Ford in Europe. The hub drive
transmission system has been completely redesigned and the capacity of the lathe, in terms of
maximum rotor diameter and thickness that can be machined has been increased to allow machining
of the Dodge Ram rotors. The special hub adaption method designed by RTI for the BRC450 is brand
new and substantially improved. The BRC450 uses the same special cutting tips and special geometry
developed by RTI for the BRC35 and BRC500 models. The Transport/Setup Lift (not supplied with the
BRC450L) is designed and produced in the USA by RTI to make handling the BRC450 easier.
The BRC450 is designed to be easy to use. Once the unit is mounted to the hub it operates in much
the same way as a typical bench mounted lathe. (In fact, with a special kit, the BRC450 can be used
as a bench mounted disc only brake lathe!) Mounting the unit on the vehicle’s hub requires the axis of
the BRC450's drive to be aligned or compensated to the vehicle’s hub axis. The precision of this
alignment or compensation for the BRC450 or any other hub mounted lathe will determine the rotor
run out that is finally achieved. The time to achieve the necessary compensation or alignment of the
BRC450 is minimized. Less than two minutes per wheel to get around 0.002" (0.005 mm) of run out
and only slightly more time to achieve “near zero” or less an 0.001" (0.0025 mm) of run out. The
BRC450's hub plate is attached to the vehicle’s hub by means of 3, 4, 5 or 7 special “cranks” and the
compensation is achieved by simply lengthening or shortening the length of these “cranks” using a dial
indicator to determine the correct setting. Minimizing brake disc run out is an important aspect of
modern brake service. Elimination of pedal pulsation issues on wheels with pre-loaded wheel bearings
requires less than 0.001" (0.0025 mm) of run out. If the wheels do not run on pre-loaded wheel
bearings, run out of 0.002" (0.005 mm) is acceptable.
Running the BRC450 is simple. It has one spindle speed and one feed rate. The feed rate is set at the
factory for optimum speed and surface finish. It can be adjusted to be faster or slower with instructions
from RTI’s technical support department but such adjustment is not recommended. An exclusive
feature of the BRC450 is Offset Step Feed, where the feed is alternatively turned on and off
mechanically. This special Offset Step Feed improves the surface finish of the cut and produces a non-
directional finish automatically.
The BRC450 can be used as a “single pass-one cut” machine. However, RTI recommends a “two
pass” machining process with a rough “foundation” cut just deep enough to clean up the rotor, and an
extra fine finish cut, with a depth of only 0.001-0.002" (0.025-0.05 mm) per side, taking full advantage
of the special cutting tool design of the BRC450 This two pass technique will not remove any more
material than necessary, and even though it may take a few minutes longer, it will result in a more
perfect rotor in every respect.