MAHLE RTI BRC450 User Manual
Page 13
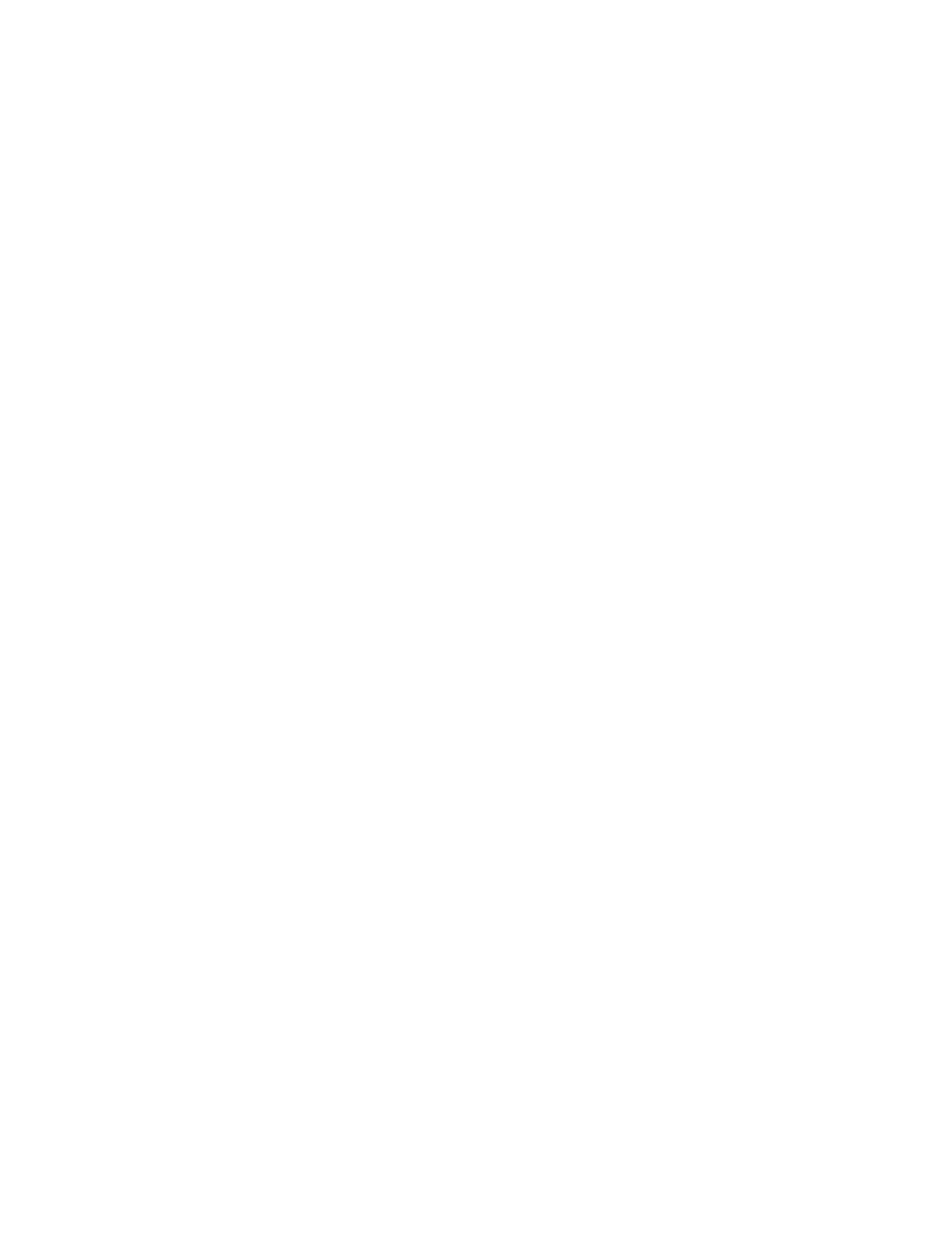
Page 11
NOTE:
At this point, the Transport/Setup Lift can be disconnected and moved out of the way if desired.
E. Set-up for Compensation. (See Figure 6) First, note the scribed marks on the large 27 mm nuts and
the body on each crank. Using the supplied 27 mm wrench, tighten each nut until the nut bottoms out
against the body of the Crank, then loosen the nut one full turn until the two scribe marks are aligned
and there is a small 0.5 mm (0.020") gap between the nut and the Crank body. (The small nuts will
need to be again tightened finger tight.) Now tighten the nuts holding the Cranks to the Centering
Plate/Bell using the wrench supplied. (Do not over-tighten.) Then install the dial indicator as shown in
the figure, clamping the base to a sturdy part of the vehicle hub/spindle/knuckle assembly. The dial
indicator stylus must be in contact with the flat non-moveable bottom section of the tool holder
assembly.
F. Compensation (See Figure 6) Turn the BRC450 on so that the spindle, hub and rotor are rotating
freely. Note the total movement of the dial indicator. Move the dial indicator bezel so that “0" is in the
middle of the needle’s total movement. (See part “a” of Figure 6) Stop the lathe. Using the on/off switch
“jog” the rotation so that the lathe stops at a point near the maximum needle travel in either direction
from “0". Note the color of the Crank that is furthest away from the dial indicator in the horizontal
position. Push on the lathe near the hand wheel and determine the direction of the dial indicator
needle. If the needle moves closer to “0" , when pushing on the lathe, the Crank must be lengthened
by loosening the small nut and the large adjustment nut. (See part “b” of Figure 6) If the needle moves
further away from “0" when pushing on the lathe, the Crank must be shortened by tightening the large
nut and the small nut. (See part “c” of Figure 6). Use the supplied wrenches for adjustment.
Each time adjustment is made, the goal is to have the adjustment cause the dial indicator to move ½
of the distance closer to “0". Repeat the “jog” rotation and adjustments as necessary so that the total
dial indicator movement is no more than 0.004" (0.1 mm). Note the color of each Crank adjusted. If a
Crank is lengthened, the opposite Crank(s), one for 4 lugs or two for 3 and 5 lugs, should be shortened
approximately the same amount so that the Centering Bell is not deformed. The process is much like
the process of adjusting the legs of a table so that the table is level and does not rock.) Note that the
total movement is about one-half of the mis-alignment of the lathe spindle axis and the vehicle’s hub
axis because the dial indicator is positioned twice as far from the center of the hub axis as is the rotor
surface. Now turn on the lathe and again read the total movement of the dial indicator. With 0.004" (0.1
mm) total movement of the dial indicator, the resulting run out of the rotor after machining will be one-
half of this figure or 0.002" (0.05 mm). This is the maximum recommended. Holding the large nut in
place, tighten each of the small nuts firmly and you are about ready to machine the rotor!
For a higher degree of precision, repeat the compensation process, changing the length of the Cranks
as necessary so that the total movement of the dial indicator is as close to 0.001" (0.025 mm) as
possible or less. With 0.001" (0.025 mm) or less movement of the dial indicator, the resulting rotor run
out will be 0.0005" (0.0127 mm) or “near zero”.
ONCE YOU HAVE PERFORMED THIS PROCEDURE SEVERAL TIMES IT WILL BE EASY.
IT IS LIKE RIDING A BICYCLE!
If there is significant wheel bearing play, precision compensation will be more difficult. If the play can
not be removed by adjustment, the play must be measured on the dial indicator and subtracted from
the needle movement during adjustment. During the final check with the lathe running, the bearing play
can be ignored as the rotor will tend to self center during rotation.