Installing masonry anchors – Vestil LPRO User Manual
Page 3
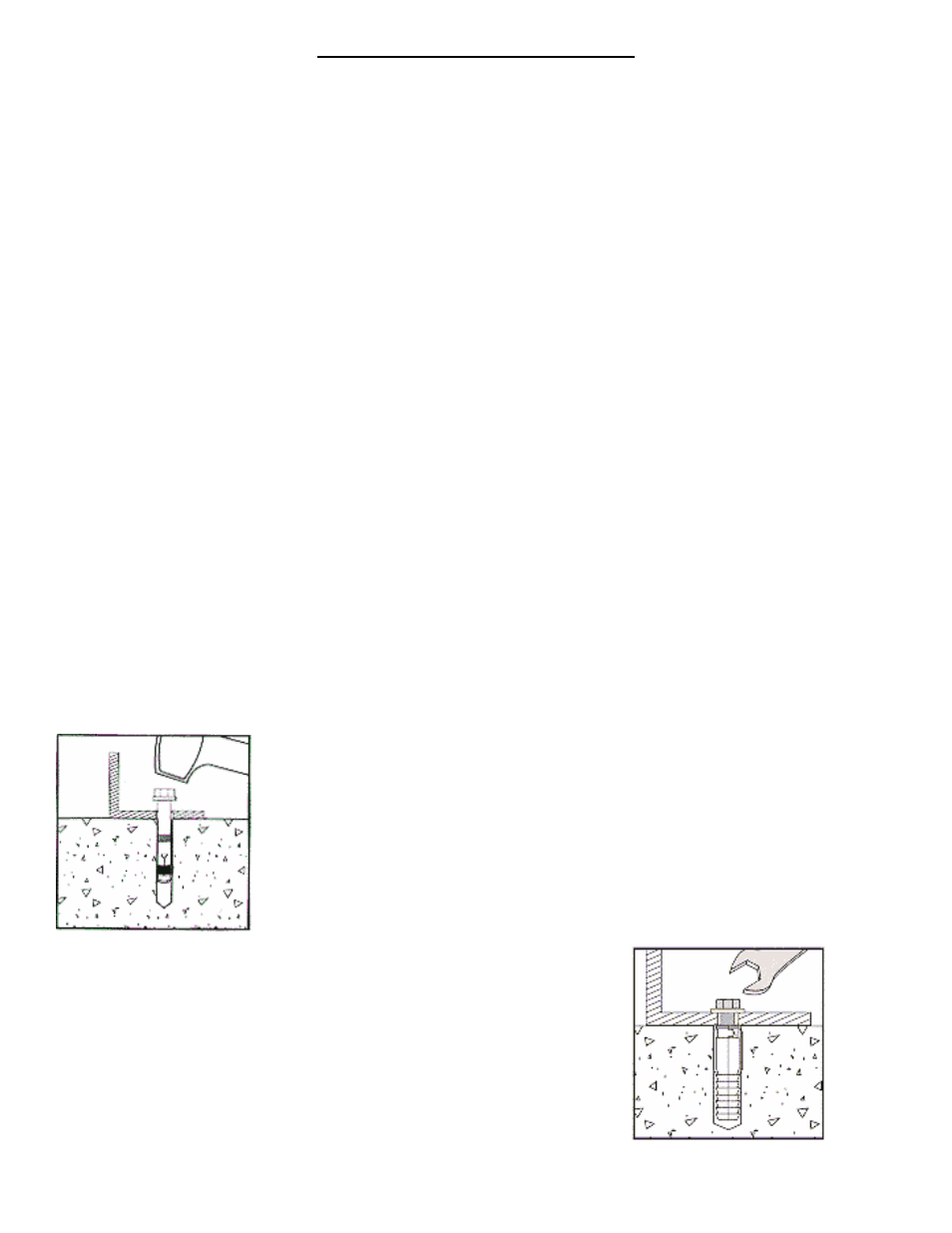
concrete anchors, installation, 1005.doc
3 of 4
Vestil Mfg Co / T&S Eqpt Co
INSTALLING MASONRY ANCHORS
The most important factor in choosing the proper anchor is the type of load it will carry. Shear loads are caused when the
weight of the fixture exerts force parallel to, or along, the surface of the concrete. Tensile loads are caused when the fixture
exerts force perpendicular to, or away from, the concrete surface.
Because precise knowledge of the condition of concrete at a given location is typically lacking, the standard recommendation is
that the anchor you choose should be rated for about four times the load’s weight it will carry if it will bear a static load, and eight
times the load’s weight if it will carry a dynamic or impact load. Static loads are loads that merely sit or hang without ever
experiencing a change in load conditions. Impact, or dynamic, loads have forces that vary in some way, such as when a load is
driven across an edge-of-dock dockleveler or a speed bump.
The holding power of any anchor depends on: the quality of the concrete -- if the concrete is old and crumbly, the holding
power of the fastener will be reduced, and; its position -- if the anchor is placed near the edge of the concrete, or if two anchors
are placed too close together, the force generated by the anchor might break the concrete.
*
An anchor should be placed no closer to the edge of the concrete than the distance equal to five times the anchor’s width .
Therefore, a ½" diameter anchor should be no closer than 2½" (½” times five) from the edge of the concrete. Also, two anchors
should never be placed closer than ten times the anchor’s width from each other. In other words, two ½" anchors should be at
least 5" (½" x ten) apart.
♦
Two types of one-piece, mechanical expansion anchors are popular.
Sleeve anchors have a steel sleeve on the shank, split at the bottom so it can expand. The bolt has a cone-shaped plug at the
base, and a nut on the top. When you place the anchor in the hole and tighten the nut, it draws the bolt upward, pulling the plug
into the sleeve and expanding it against the hole. Once installed, sleeve anchors cannot be removed. They are available in a
variety of head styles, however -- a removable hex head, an acorn nut, or either round- or flat-head screws.
The shank of a wedge anchor is similar to a sleeve anchor -- a solid shank, threaded at the top and with a cone-shaped plug at
the bottom. But the shank of a wedge anchor is grooved on opposite sides. In each groove is a rectangular shank with a spade-
shaped wedge on the end. As the nut on top is tightened, the washer pushes the rectangular shanks down, which spreads the
wedges over the plug. A wedge anchor cannot be removed once it is installed. Wedge anchors always have a hex head screw with a
washer so the material can be removed and reinstalled.
*
As a rule, use sleeve anchors when working with soft concrete or installing them in the mortar joints between block or brick.
Also use sleeve anchors when you suspect that the concrete may have voids in it. Sleeve anchors have a larger bearing surface
than wedge anchors. Use wedge anchors for maximum holding power in hard concrete.
♦
Once the proper type of anchor is determined, select the size of fastener that is closest to the size of the anchoring hole in
the product. Anchoring products’ specifications vary from one manufacturer to the next -- if the manufacturer's installation
instructions differ from the information in this document, always follow the manufacturer's instructions. When drilling a
hole for a masonry screw, it is a good idea to utilize the special bit sold by the screw manufacturer. Proper hole sizing is
critical for optimal holding power. Never use a dull bit, because it tends to produce a larger hole than the same size of
sharp bit. When drilling large holes in masonry, it is much easier and more accurate to start with a smaller bit and step up
gradually to the required bit diameter. Eye protection and a dust mask should be worn when drilling and cleaning the holes.
•
To install wedge or sleeve anchors, first position the material you want to anchor. Mark the
locations of the product’s anchor holes on the concrete. The product can be left in place if
there is adequate clearance to allow for drilling the holes. Use a hammer drill to drill the holes
in the concrete at the product’s bolt hole location. Make sure the holes are the specified
diameter for the anchor that you plan to use, and at least ¼" deeper than the length of the
anchor. Blow the dust out of the drilled holes with compressed air or a blow-out bulb. Place
the product over the anchor holes and insert the anchors into the holes. Use an appropriately-
sized washer between the bolt head and the product if necessary to prevent the product’s hole
from eventually pulling over the bolt head. Tighten a sleeve anchor two to three turns to
expand it. Tighten a wedge anchor three to five turns. The anchor manufacturer’s instructions
might specify that the anchor is to be tightened with a torque wrench to a certain number of
foot-pounds.
•
Installing a two-step mechanical anchor: For a two-step anchor, tap the
anchor into the hole, then position the item being mounted and install the
fastener. Again, use washers if necessary if there is a possibility that the product
could eventually pull off of the bolt head. Tighten the fastener until its head is
fully seated against the mounted item and secure in the hole. Do not over tighten
it, or you might break the fastener or ruin the anchor’s bond with the concrete.
Note: To determine the proper type of concrete fastener to use for a specific
application, consultation with the building’s architect or facility engineer
is recommended.