KB Electronics KBPC-225D User Manual
Page 11
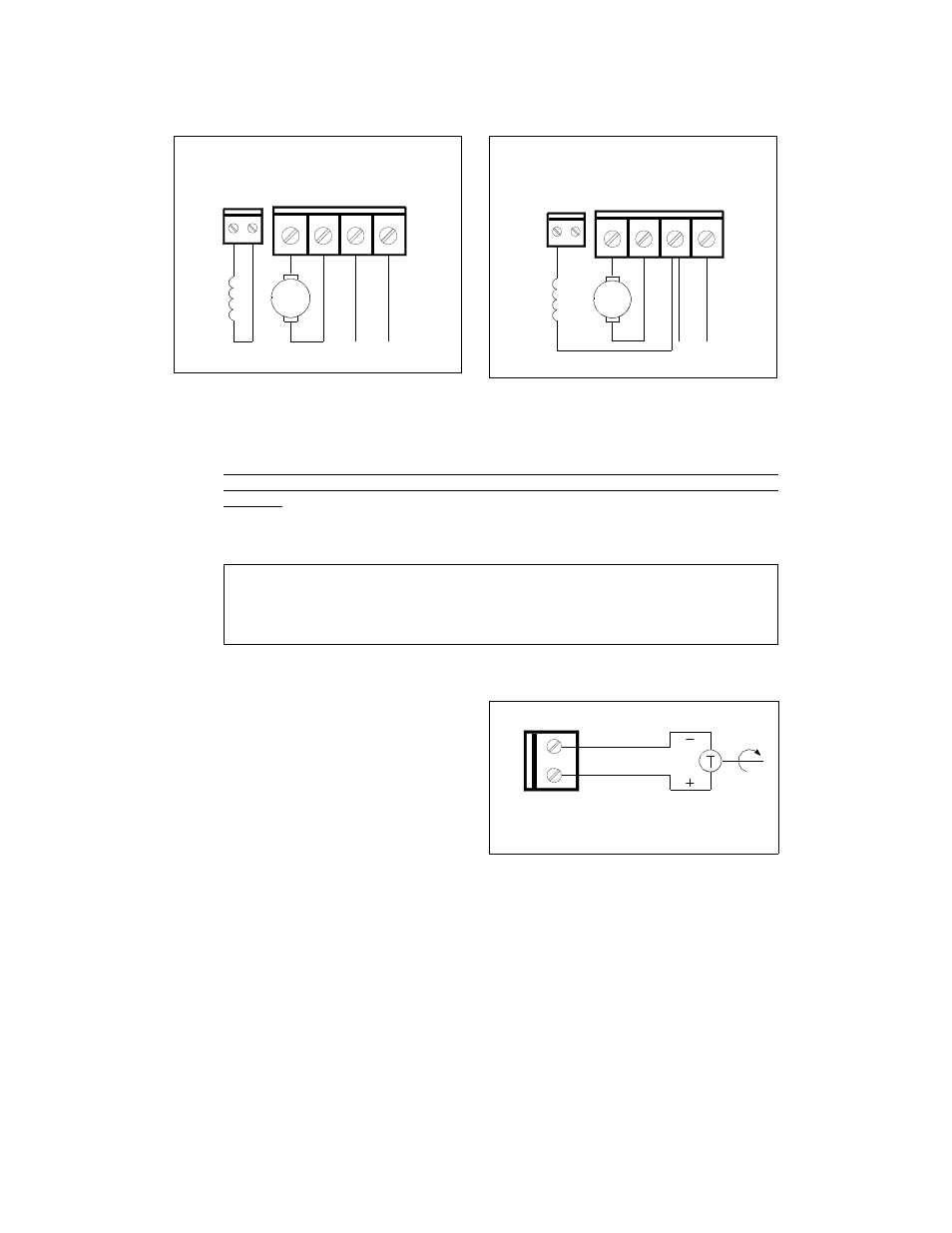
9
FIG. 6A – FULL VOLTAGE FIELD
180 VDC MOTORS WITH 200 VDC FIELDS
+
A1
F2
A2
L1
L2
FIELD
TB1
TB2
AC
LINE
ARM
F1
–
–
+
FIG. 6B – HALF VOLTAGE FIELD
180 VDC MOTORS WITH 100 VDC FIELDS
A1
F2
A2
L1
L2
F1
FIELD
TB2
TB1
+
AC
LINE
ARM
+
–
D. Ground – Be sure to ground (earth) the control by connecting a ground wire to the Green
Ground Screw located to the right of the terminal block. (See Fig. 1, p. 5)
E. DC Tachometer Input – If tachometer feedback is required, an analog tach signal must be
connected to the terminal block TB3.
Note: For tachometer feedback, Jumper J3 must be set to the "TFB" position, jumper J6
must be set for the proper tach voltage, and the IR COMP must be set to minimum (ccw)
position. (See Section III C, p. 7.)
Connect the tachometer so that when the motor rotates the positive tach voltage lead is
connected to T+ and the negative tach lead is connected to T–. (See Fig. 7.)
Note: If the tach voltage is connected backwards, the control will drive the motor
at full speed only. If the Forward-Brake-Reverse switch is used, provision must
be made to reverse the polarity of the tachometer leads when the control is
switched to "Reverse."
F. Main Potentiometer – The control is
supplied with the main potentiometer
prewired. However, the control can
also be operated from a remote
potentiometer, or from an Isolated
analog voltage for voltage following.
To operate from an external source
remove white, orange and violet
potentiometer leads from terminals P1,
P2 and P3. The leads may be taped
and left in the control. The
potentiometer itself may be removed,
provided a watertight seal is used to
cover the hole in the front cover.
FIG. 7 – TACHOMETER
CONNECTION DIAGRAM
TACHOMETER WIRES MUST BE CONNECTED SO THAT
TB3
T
–
T+
CORRECT POLARITY IS ACHIEVED WHEN TACH ROTATES
1. Remote Potentiometer – Connect remote potentiometer wires to terminals P1, P2 and
P3, so that the "high" side of the potentiometer connects to P3, the "wiper" to P2 and the
"low" side to P1. (See Fig. 8A p. 10)
2. Analog Input – An isolated 0 - 5 or 0 - 10 VDC analog voltage can also be used to drive
the control. Note: If an isolated signal voltage is not available, an optional signal isolator
can be installed (Model KBSI-240D, P/N 9431, see Fig. 14, p. 18, for signal isolator
wiring diagrams). Connect the isolated input voltage to terminal P2 (positive) and P1
(negative). (See Fig. 8B, p. 10) Note: Be sure jumper J7 corresponds to proper range
of input voltage 0 - 10 or 0 - 5 VDC. When the potentiometer is disconnected from P1,
P2, P3 to connect an analog input signal, the MIN trimpot will have to be adjusted
clockwise to achieve a 0
+
output voltage.